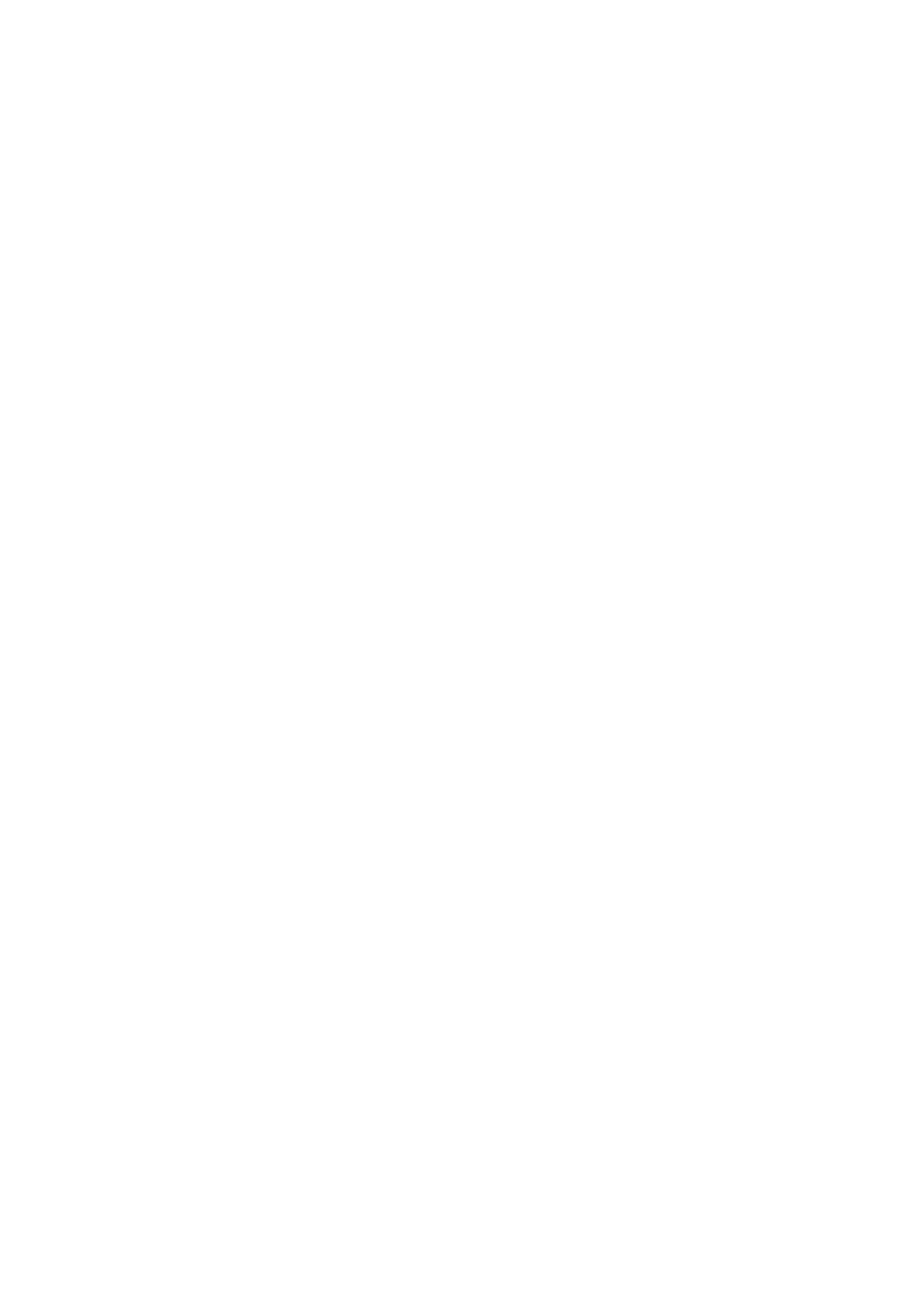
2
Sommaire
Remerciements ........................................................................................................................... 3
Liste des figures ......................................................................................................................... 4
Introduction générale .................................................................................................................. 5
Présentation de l’entreprise ........................................................................................................ 6
Introduction ................................................................................................................................ 8
1. Généralités sur les ciments ................................................................................................. 8
1.1. Définition ..................................................................................................................... 8
1.2. Composition des ciments ............................................................................................. 8
2. Processus de fabrication des ciments ................................................................................. 9
2.1. Extraction des matières premières ............................................................................. 10
2.2. Concassage ................................................................................................................ 10
2.3. Pré-homogénéisation ................................................................................................. 10
2.4. Broyage de matière première ..................................................................................... 12
2.5. Homogénéisation de la poudre crue .......................................................................... 13
2.6. Cuisson et clinkérisation ............................................................................................ 13
2.7. Refroidissement ......................................................................................................... 15
2.8. Broyage du clinker ..................................................................................................... 15
2.9. Stockage, Ensachage et Expédition ........................................................................... 15
Conclusion ................................................................................................................................ 16
Chapitre 2 : Les capteurs .......................................................................................................... 17
Introduction .............................................................................................................................. 17
1. Généralités sur les capteurs .............................................................................................. 17
1.1. Définition ................................................................................................................... 17
1.2. Les types des capteurs ............................................................................................... 17
2. Le choix des capteurs PT100 ........................................................................................... 18
Conclusion ................................................................................................................................ 20
Conclusion générale ................................................................................................................. 21
Références bibliographiques .................................................................................................... 22