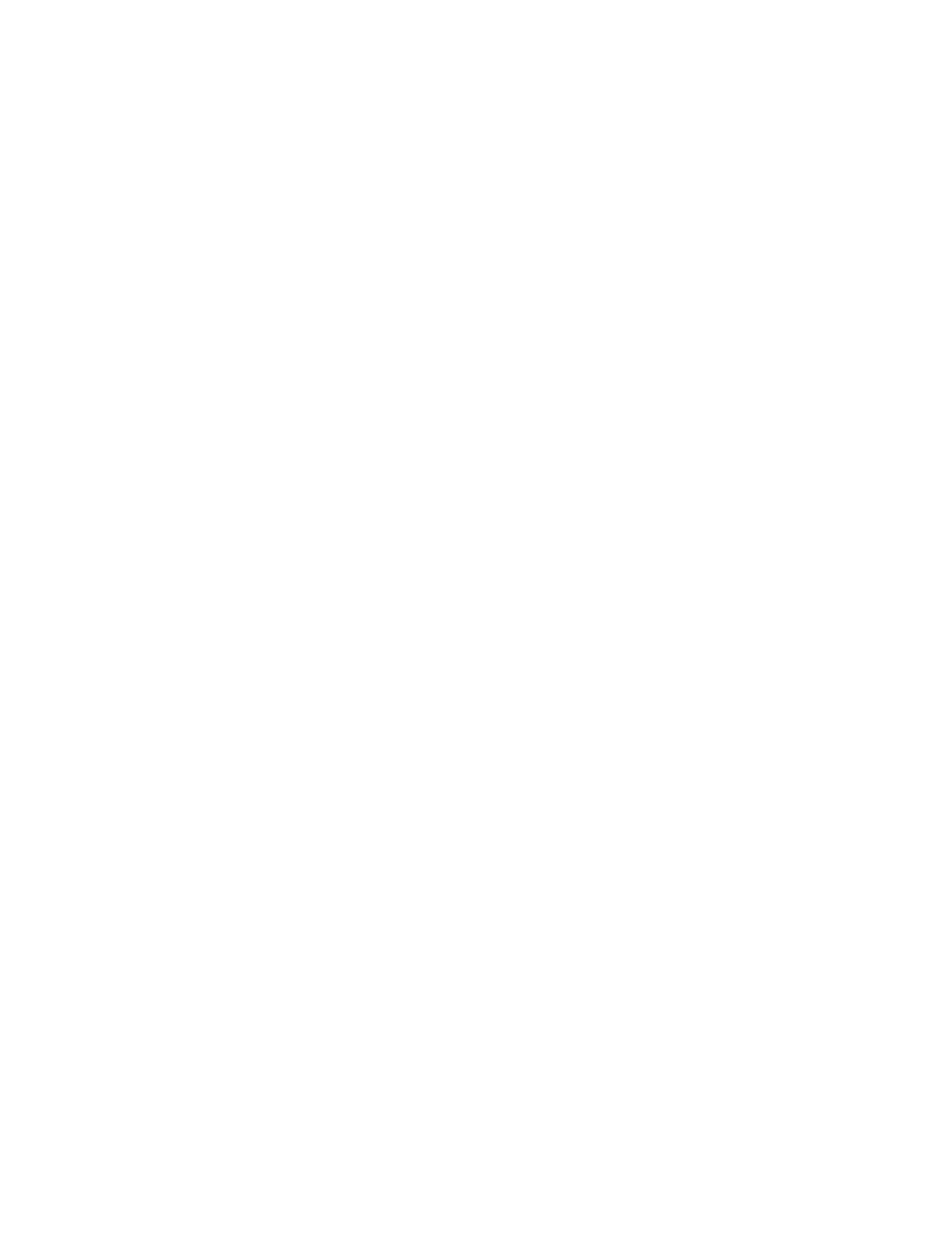
would be associated with the discharge of heat-treated ballast
water. A number of factors will limit the practicality of thermal
treatment primarily related to the volume of water that is associ-
ated with large vessels and the amount of energy required to heat
the volume. Thermal treatment may be more applicable to ballast
water originating from warmer environments. Heat required for
thermal treatment could be reduced where water temperatures are
at tropical or summer levels (30 deg C or higher). The heat loss to
the ambient waters outside of the hull must be considered. Dif-
ferent types of organisms or organisms from different parts of the
world may have different sensitivities to heat. A few recent studies
suggest that heating ballast water is the best method for killing a
variety of higher organisms and microorganisms that are found in
ballast water. Rigby et al. (1999) showed how a cost-effective
heating technique using waste heat from a ship engine could be
used to kill many unwanted organisms. In an ocean trial, heated
water flushed through one of the ballast tanks resulted in the
destruction of all zooplankton with very limited survival of the
original phytoplankton.
Electric pulse. Small-scale experiments have been performed
by applying electrical voltages in the 15 to 45 kV range with pulse
duration of 1 µs. Large energy sources would be required for
systems capable of treating large volumes of ballast water (Na-
tional Research Council 1996).
Filtration. The physical separation and removal of organisms
can be accomplished during ballasting operations using a ship-
board filtration system. Some would argue that this technology is
the most promising choice. Filtering ballast water as it is loaded is
an attractive option since it would minimize the introduction of
unwanted organisms. The options for onboard filtration systems
are either mesh strainers or deep media filtration. Many problems
associated with a strainer technology have been solved with the
development of commercially available continuously cleaned
screening systems. Media filters are attractive in principal because
small-size particles can be removed, but these filters are most
likely unrealistic for on-board treatment of ballast water because
of the large footprint that would be required. The primary disad-
vantage of the strainer filters is that many organisms are smaller
than strainers and would pass through the treatment system. A
study for the Canadian Coast Guard (1992) concluded that the
physical removal of organisms by filtering may be an effective
stand-alone treatment process or may be used in conjunction with
other technologies, such as chemical treatment or UV sterilization.
Flow-through centrifugation systems can separate particles prior
to filtering to reduce filter clogging.
Biocides. The addition of chemicals that would kill or inactivate
a variety of organisms found in ballast water is an attractive treat-
ment technology because of the ease of application. A biocide
could simply be added to the ballast tank and allowed to react for
a specified period. Biocides are among the most widely used in-
dustrial chemicals, and there is a large body of knowledge about
their use in wastewater treatment. If similar concentrations were
required to inactivate organisms found in ballast water, then a
large ship would need to carry only a few cubic meters of biocide
per voyage. The use of biocides for ballast water treatment has
been rejected by some for several reasons, including the reluctance
to add toxic chemicals to water that may be discharged back into
the ocean, the unknown effectiveness of biocides against target
organisms, and compliance with discharge regulations around the
world. Oxidizing biocides such as chlorine, chlorine salts, and
ozone have been used for decades in a variety of sanitizing appli-
cations. Ozone is a strong oxidizing agent used for treatment of
potable and industrial waters. With the increasing environmental
concern associated with the use of chlorine, ozone has received
greater attention in recent years. Ozone is an unstable gas that
must be generated as needed, and some reviewers have concluded
that ozone may not be practical for shipboard use (National Re-
search Council 1996). Along with generation, ozone efficacy is a
problem due to the gas–liquid contact requiring elaborate diffu-
sion equipment. In salt water, ozone produces many of the similar
residual compounds as chlorination. Nonoxidizing biocides such
as glutaraldehyde or vitamin K have also have been suggested.
2. Electrochlorination
2.1. Background
Seawater (normally between 15 and 35 grams/liter) or other
water containing NaCl may be used to generate a disinfecting
solution containing chlorine by passing a direct electrical current
through the solution. On-site generation of hypochlorite from sea-
water has been used for over 25 years. These systems can be
purchased as completely skid-mounted systems that generate so-
dium hypochlorite from seawater. These systems are used in re-
fining, petrochemical power plants, offshore drilling production,
and marine applications around the world. Systems can be scaled
to the appropriate size depending on the quantity of hypochlorite
required.
The type of electrolytic cell commonly used in these marine and
offshore applications is a “tube within a tube.”A cell consists of
one anode, one cathode, and one bipolar tube with the necessary
ancillary hardware to facilitate assembly. The outer anode and
cathode are manufactured from seamless titanium pipe. The anode
surface is coated with proprietary precious metal oxides, primarily
ruthenium and iridium. Seawater enters one end of the cell and
passes between the cathode, the anode, and bipolar tube annular
spaces. When direct current is applied to the cell, sodium hypo-
chlorite results. One cell can produce up to 5.5 kg/day, and a
maximum of 12 cells can be connected in series for a capacity of
65 kg/day per train.
In some applications, such as ballast water treatment, a dechlo-
rination step can be added to the process. This requires adding a
reducing agent, such as sodium sulfite, to the end of the system to
neutralize any residual chlorine at the point of discharge. The end
result is a nontoxic stream with no free chlorine.
2.2. Chemistry
The process is based on the partial electrolysis of NaCl present
in seawater as it flows through an unseparated electrolytic cell.
The resulting solution exiting the cell is a mixture of seawater,
sodium hypochlorite (hypo), hydrogen gas, and hypochlorous
acid. Electrolysis of sodium chloride solution (seawater in this
study) is the passage of direct current between an anode (positive
pole) and a cathode (negative pole) to separate salt and water into
their basic elements. Chlorine generated at the anode immediately
goes through chemical reactions to form sodium hypochlorite and
hypochlorous acid. Reactions are shown below:
Cl
−
→Cl
2
(aq) + 2e
−
Eo ⳱1.396 V (1)
162 AUGUST 2006 JOURNAL OF SHIP PRODUCTION