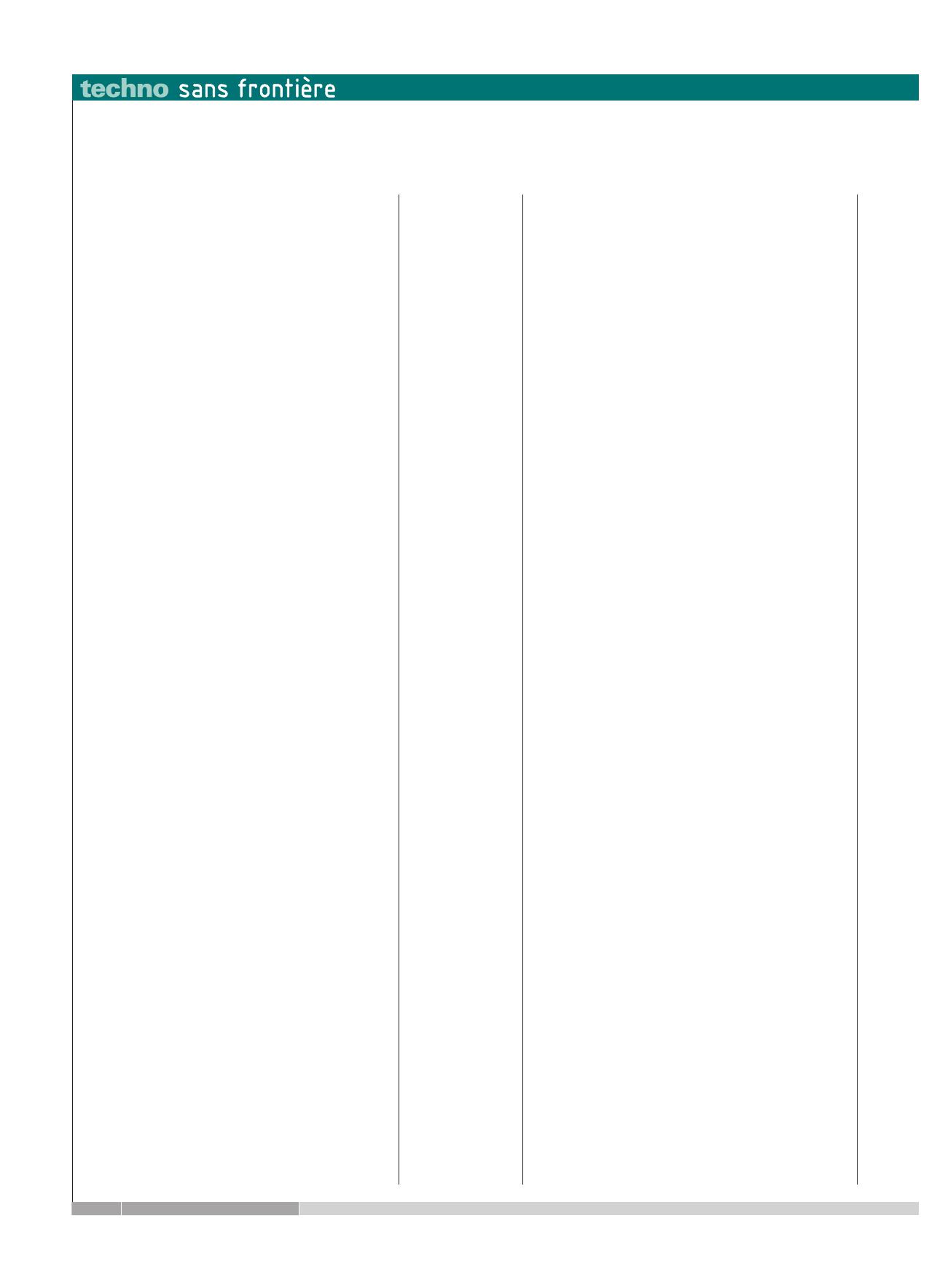
TECHNOLOGIE MAI-JUIN 2016
MAI-JUIN 2016 TECHNOLOGIE
les conducteurs sera directement liée à la capacité à
évacuer efcacement l’énergie produite au travers de
l’entrefer ou par conduction à l’intérieur des matériaux.
La forme du conducteur est plus au moins propice à
l’augmentation de la densité de courant admissible. En
effet, plus la surface d’évacuation sera importante, plus
le refroidissement sera aisé. Ainsi, si l’on souhaite aug-
menter le courant dans un conducteur cylindrique, il est
préférable d’utiliser un grand nombre de petits conduc-
teurs qu’un seul conducteur de section plus importante.
Ce choix est conforté si l’on doit tenir compte de l’ef-
fet de peau qui apparaît lorsque la fréquence des cou-
rants atteint quelques kHz (automobile). Par ailleurs, on
montre que la densité de courant atteignable dans des
conducteurs de section rectangulaire très aplatie (cir-
cuits imprimés) est beaucoup plus importante que pour
les conducteurs à section cylindrique. La diminution des
pertes par effet Joule passe aussi par l’optimisation de
la longueur active des bobines. Une bonne géométrie
des pôles du rotor de la MS augmente le rapport entre
longueur active et totale du conducteur. On dénit le
coefcient global de remplissage des encoches par le
rapport de la surface de cuivre (surface active) sur la
surface de l’encoche (classiquement 40 à 50 %). L’aug-
mentation de la valeur du coefcient de remplissage a
deux effets. D’une part, les pertes Joule augmentent car
la concentration du bobinage n’est pas optimale ; d’autre
part, l’évacuation de la chaleur est plus difcile. Enn,
les propriétés thermiques des isolants électriques pré-
sents dans les encoches joueront un rôle important dans
l’évacuation des pertes par effet Joule.
Pertes magnétiques
Les pertes magnétiques regroupent les pertes par
courants de Foucault qui résultent de la circulation
de courants induits dans le matériau magnétique et
les pertes par hystérésis dues à l’effet mémoire du
matériau magnétique qui entraîne des pertes énergé-
tiques lors des cycles magnétiques. Les premières sont
directement liées à la variation temporelle du champ
magnétique, c’est-à-dire au phénomène d’induction. Un
feuilletage des tôles magnétiques limite la circulation
des courants induits. L’épaisseur de ces tôles est très
importante car elle intervient au carré dans l’expres-
sion des pertes. Les pertes par hystérésis sont elles
aussi dépendantes de la fréquence et de la variation
d’amplitude du champ magnétique. À titre d’exemple,
pour des tôles usuelles de Fe-Si à 3 % à grains non
orientés et une épaisseur de tôle de 0,5 mm, on obtient
sous une amplitude maximum de 1,5 tesla, à 50 Hz,
des pertes fer de 6,5 W.kg
-1
. Par comparaison, des tôles
de Fe-Ni (50-50) de 0,1 mm d’épaisseur limiteront
dans les mêmes conditions ces pertes à 0,84 W.kg
-1
.
On notera aussi que, ces pertes dépendant de la fré-
quence, l’utilisation de la ferrite, caractérisée par une
forte résistivité à haute fréquence, limite ces pertes
que l’on retrouve aussi dans les aimants permanents.
Pertes mécaniques
Les frottements mécaniques dans les machines tour-
nantes sont principalement causés par les points de
contacts mécaniques localisés au niveau des systèmes
collecteur-balais, bagues-balais ou des paliers.
Les pertes aérodynamiques sont, elles, dues à la
rotation du rotor. Pour xer les idées, on peut en esti-
mer l’importance dans le cas de l’air avec un entrefer
de 5 mm. Alors que pour une vitesse périphérique
de 100 m/s on trouve des pertes aérodynamiques de
660 W.m
-2
d’entrefer, pour une vitesse trois fois plus
élevée, ces mêmes pertes atteignent 13,7 kW.m-2.
Les pertes aérodynamiques, à très grande vitesse,
peuvent donc être responsables d’échauffements très
importants. La saillance éventuelle du rotor accroît
bien entendu ce type de pertes. On peut diminuer ces
pertes aérodynamiques en remplaçant l’air par un
uide caloporteur mono ou multiphasique.
Évacuation des pertes
Les pertes Joule et magnétiques sont à l’origine
d’échauffements à l’intérieur même des matériaux
composant les moteurs. Pour un même matériau, les
petits systèmes auront une plus grande capacité à
accepter une plus forte densité de pertes. En effet, si
par exemple on soumet un matériau magnétique (fer
silicium) à un échauffement de 5 K entre le cœur et la
surface extérieure, il sera capable d’évacuer un ux
thermique de 2 kW.m-2 si la distance cœur-surface
est de 20 mm, alors que ce transfert ne sera que de
90 W.m-2 pour une distance 5 fois plus grande. Cette
limitation de la capacité à accepter des pertes volu-
miques importantes entraînera une limitation de la
dimension de la machine ou la nécessité de modier
les conditions de refroidissement en surface.
Limites en vitesses
La vitesse de rotation des moteurs est limitée par
leur vitesse périphérique maximale qui dépend
principalement de la géométrie et de la nature des
matériaux utilisées (cuivre, aluminium, acier…). On
peut calculer les ordres de grandeur des vitesses
périphériques maximales pour les principaux consti-
tuants des machines classiques. Ainsi, on trouve que
le collecteur des MCC possède la vitesse périphé-
rique la plus faible (80 m/s), que les MS à aimants
permanents voient cette vitesse beaucoup varier
en fonction du mode de pose des aimants sur le
rotor (de 100 m/s pour des aimants tuiles collés à
230 m/s pour des aimants frettés collés en surface),
et les vitesses périphériques maximales (300 m/s)
sont atteintes avec des MAS à cage d’écureuil à
encoches fermées et des machines à reluctance
variable à rotor massif.
Cette frontière de la vitesse périphérique maximale
limitera d’autant plus la vitesse de rotation du moteur
que le diamètre du rotor sera grand.