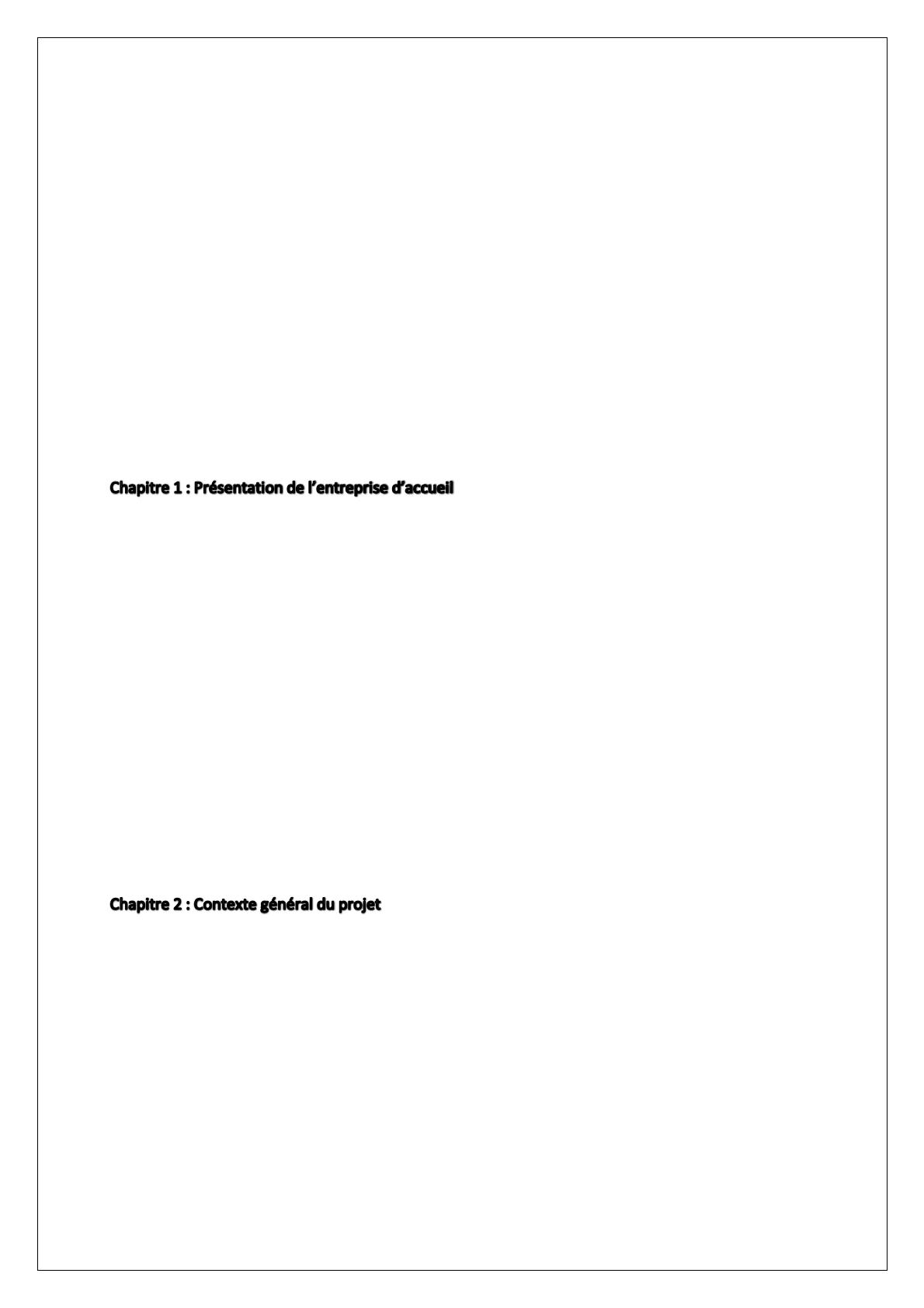
4
Table des matières
Dédicace .............................................................................................................................................1
Remerciement ....................................................................................................................................2
Acknowledgements ............................................................................................................................3
Table des matières .............................................................................................................................4
Liste des tableaux et figures ...............................................................................................................8
Liste des équations ........................................................................................................................... 10
Liste des acronymes ......................................................................................................................... 11
Introduction générale ...................................................................................................................... 12
............................................................................ 13
1. Introduction .............................................................................................................................. 14
2. Domaine d’activité de l’entreprise............................................................................................. 14
2.1. Electricité Industrielle ........................................................................................................ 14
2.2. Automatisme Industriel ..................................................................................................... 14
2.3. Maintenance Electronique ................................................................................................. 15
3. Fiche technique ......................................................................................................................... 15
4. Structure et organisation générale ............................................................................................ 16
5. Présentation du service ............................................................................................................. 16
5.1. Electricité Industrielle ........................................................................................................ 16
5.2. Maintenance électronique ................................................................................................. 16
5.3. Automatisme Industriel ..................................................................................................... 16
6. Conclusion ................................................................................................................................ 16
............................................................................................ 17
1. Introduction .............................................................................................................................. 18
2. Cahier de charges ...................................................................................................................... 18
2.1. Contexte et définition du problème ................................................................................... 18
2.2. Les objectifs du projet :...................................................................................................... 19
2.3. Spécification du projet : ..................................................................................................... 19
2.3.1. Besoins fonctionnels : ................................................................................................ 20
2.3.2. Besoins non fonctionnels: .......................................................................................... 20
3. Etude préalable : ....................................................................................................................... 20