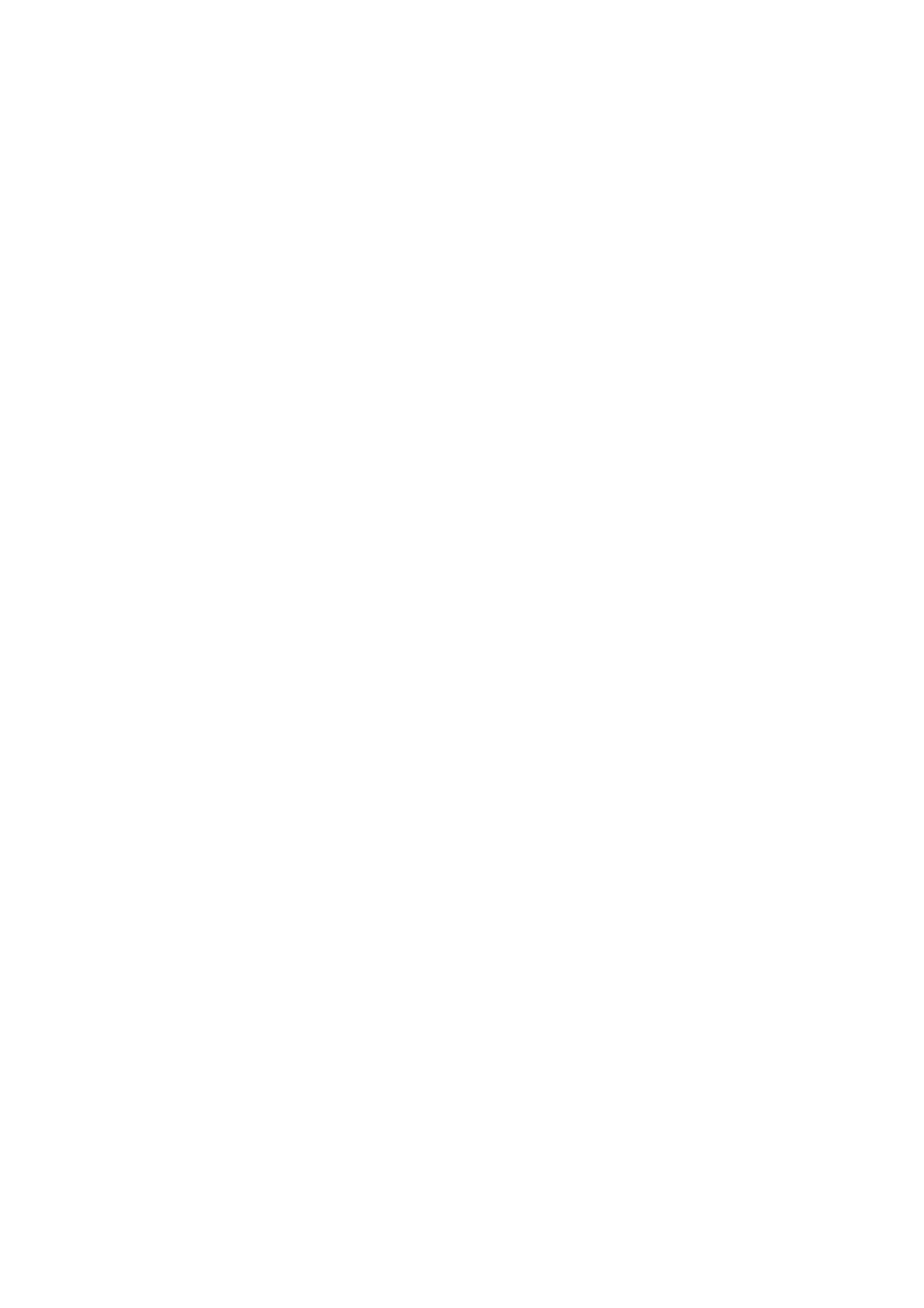
Comparison of carrier signal based approaches for
sensorless wound rotor synchronous machines
Alexander Rambetius, and Bernhard Piepenbreier, Senior Member, IEEE
Chair of Electrical Drives and Machines, University of Erlangen-Nuremberg, Germany
Abstract—Wound rotor synchronous machines enable a large
variety of approaches for carrier signal based sensorless control
since the rotor voltage serves as an additional input to the system
and the rotor current as an additional, easy to measure, state
variable. Consequently it is possible to use the rotor winding
either as the transmitter or as the receiver of a carrier signal. In
these cases the mutual inductance between the d-axis and the
rotor winding is of major importance. Moreover a rotor saliency
can be evaluated if the stator is used as the transmitter and as the
receiver of the carrier signal. If voltage injection is used, the
rotor winding acts like a damper winding for the carrier signal
and consequently the evaluated saliency differs from the saliency
which is utilized for sensorless control of permanent magnet syn-
chronous machines. Carrier current control on the other hand
offers the possibility to evaluate a magnetic saliency regarding
the inductances in the d- and q-axis. This work provides a de-
tailed review of the aforementioned approaches and analyses the
prerequisites. In addition to this the different approaches are
made comparable in terms of signal-to-noise ratio and cross
saturation. This is done by introducing suitable intensity terms.
With the help of identified parameters the most promising
approach for the investigated machine is found. Experimental
results confirm the validity of the comparison.
Keywords—wound rotor synchronous machine, wound field
synchronous machine, electrically excited synchronous machine,
sensorless control, high frequency injection, traction motor
I. INTRODUCTION
Wound rotor synchronous machines (WRSM) are synchro-
nous machines (SM), in which the rotor flux is generated by an
electrical winding. Besides WRSM, other notations are used in
the literature as well. Some of the most common ones are:
• Wound rotor [1-6] or wound field SM [7-9]
• Electrically excited [10-12] or energized SM [13]
• Externally excited SM [14]
• DC-excited SM [15]
In the following the term WRSM will be used. WRSMs feature
certain characteristics that suite the needs of automotive
traction applications very well [1], [14-15]. If field oriented
current control is applied to a WRSM, information about the
rotor position is required. This information is usually obtained
by a motion sensor (incremental encoder, resolver, etc.).
Leaving out this sensor reduces cost and may increase the
reliability of the whole drive system. Therefore sensorless
control is highly desirable in automotive traction [15]. At high
speed the rotor position can be obtained by evaluating the
motional electromotive force (EMF) [4], [15]. These methods
however fail at standstill and low speed. A common approach
to overcome this limitation is the injection of a carrier signal.
This carrier signal usually has got a higher frequency than the
fundamental wave and is therefore often referred to as high-
frequency (HF) signal. The conventional approaches for
permanent magnet synchronous machines (PMSM) inject
continuous HF-voltages into the stator and evaluate the
resulting current response. In contrast to PMSMs WRSMs
allow to use the rotor winding as the transmitter or as the
receiver of the carrier signal, which results in the following
possibilities for the transmission:
• Stator Stator [7], [10], [16]
• Rotor Stator [2], [5-6], [8-9], [12-13], [17-20]
• Stator Rotor [10], [21]
Furthermore it is possible to use the rotor as the transmitter and
as the receiver. In this case the stator slots represent a position
dependent saliency which can be evaluated. The stator teeth
however saturate very quickly and consequently the rotor
position estimation becomes complex. Therefore this approach
is not addressed in this paper. A method to estimate the rotor
speed by evaluating stator slotting harmonics in the rotor
current can be found in [4].
The most intuitive approach of the aforementioned methods
is to emulate a resolver by using the rotor as the transmitter and
the stator as the receiver of the HF-signal. Since the rotor self-
inductance is usually quite large this is not necessarily the
approach to be favored since large rotor voltages might be
necessary to create detectable stator currents [2]. If a rotating
diode rectifier is used to inductively transmit the rotor power,
the pulsation of this rectifier can be used as a carrier signal.
The resulting current response can either be evaluated in the
stator [5-6], [8] or in the rotor [22].
If the stator is used as the transmitter and as the receiver of
the carrier signal (like for PMSM [23-25]) the rotor winding
acts like a damper winding for the HF-signal and consequently
the required saliency differs from the saliency which is
necessary for sensorless control of PMSMs [10].
Recently HF-current control has been applied to PMSMs
instead of HF-voltage injection [26-30]. If this approach is
applied to WRSMs, the prerequisites chance compared to HF-
voltage injection: Since the HF-current in the rotor can be
controlled to zero, the rotor winding does not act like a damper
winding anymore. Consequently a differential magnetic sali-
ency regarding the inductances in the d- and q-axis is
evaluated.
The aim of this paper is to make the aforementioned
approaches comparable in terms of signal-to-noise ratio and
978-1-4799-4749-2/14/$31.00 ©2014 IEEE
2014
International Symposium on Power Electronics,
Electrical Drives, Automation and Motion