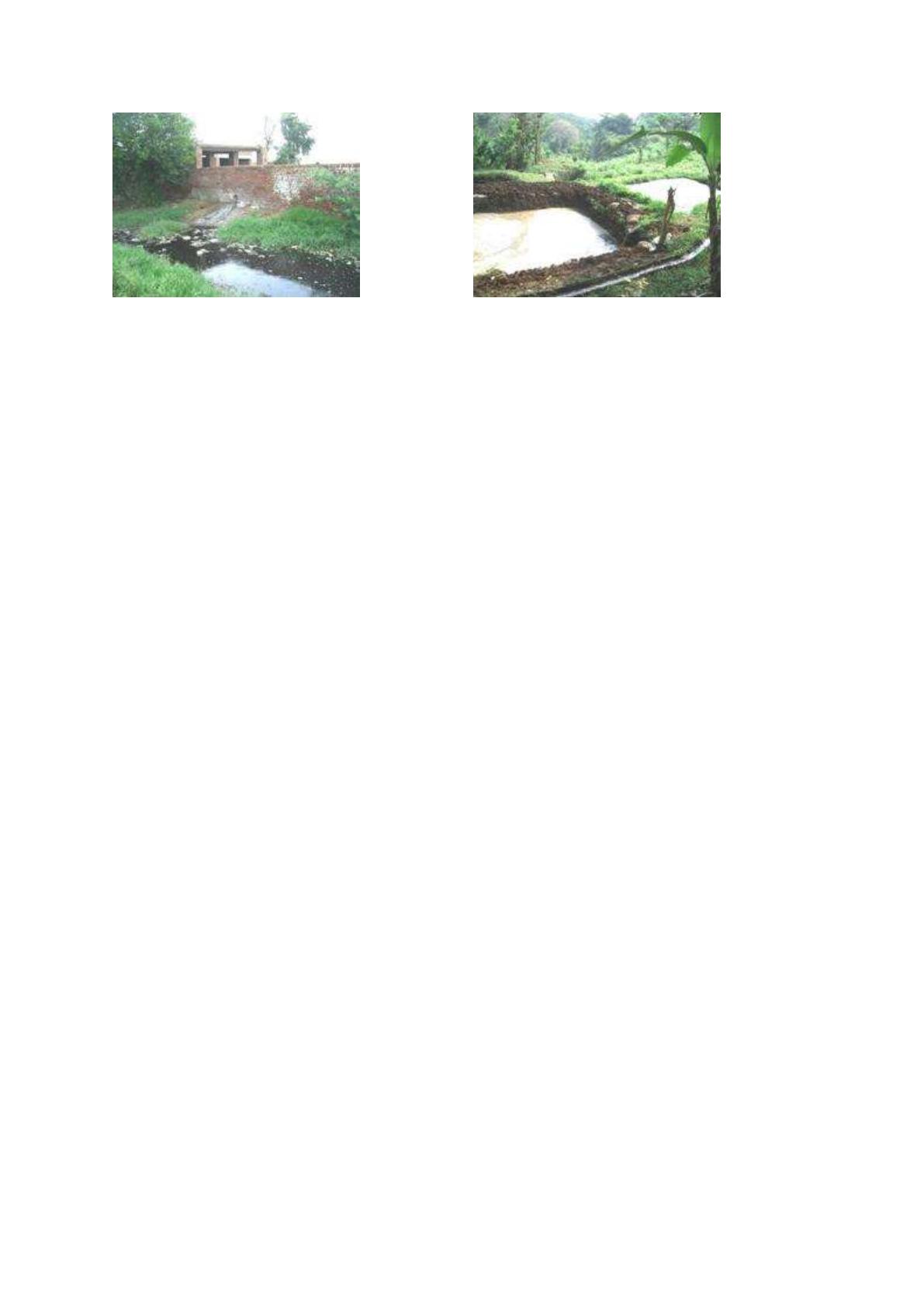
Fig. 83: Effluents dumped untreated
beyond the walls of a rural abattoir
Fig. 84: Lagoon system combined with
initial solid screening: This system is not
ideal but is used for effluent treatment by an
abattoir producing meat for top-quality
markets.
Effluent treatment in small- to medium-sized abattoirs is a difficult issue and yet a major
cause of poor hygiene. Highly efficient, combined mechanical and biological treatment plants
are beyond the reach of such abattoirs because they are too costly in initial investment and
day-to-day running. But simple treatment facilities such as soak-away pits or septic tanks do
not produce the necessary results and are not capable of significantly reducing the pollution.
One solution out of this dilemma is the introduction of biogas digesters for abattoir effluent
treatment. Biogas digesters are relatively inexpensive; construction costs for a 30 cubic
meter digester is approximately US$10 000. They require little maintenance and generate
energy (gas to be used for energy requirements at the abattoir) and the solid residues can
be used as fertilizer.
FAO has promoted this technology and initiated the construction of some prototype biogas
digesters in connection with abattoirs, the most advanced installed at the Animal Products
Development Center, a national meat training centre in Manila, Philippines.
Biogas digestion is the breakdown of organic substances that make up almost 100 percent
of the pollutant load of farm or abattoir effluents, primarily to methane gas but also to CO2 (to
a minor extent) and traces of other gases through the activity of anaerobic bacteria.
Anaerobic conditions are created through the construction of air-tight chambers usually
submerged in the ground. The construction materials used are hollow blocks, cement, sand,
gravel, rebars and pipes. The capacity of the digester chamber depends on the volume of
effluent to be treated and the retention time; but generally for small- to medium-sized
abattoirs it holds 30 cubic meters. When biogas digestion is completed, most organic matter
is broken down to methane, CO2 and water. Remaining solid materials are primarily sludge.
Observations made during the research for this report indicates that the biogas digesters
used for farm purposes need to be modified for abattoirs because the effluents from these
facilities contain higher amounts of fat residues. Such fat residues have a tendency to
generate a fatty layer or scam at the surface of the liquid in the chamber, which creates
problems for the proper anaerobic digestion of the effluents. To tackle this situation, a
double-chamber “digester” for abattoir waste treatment was developed, as illustrated in Fig.
85. Periodic release of the gas produced creates a mixing of the liquid contained in both
chambers of the fixed-dome digester and prevents the formation of the fatty scam, as the
following explains: