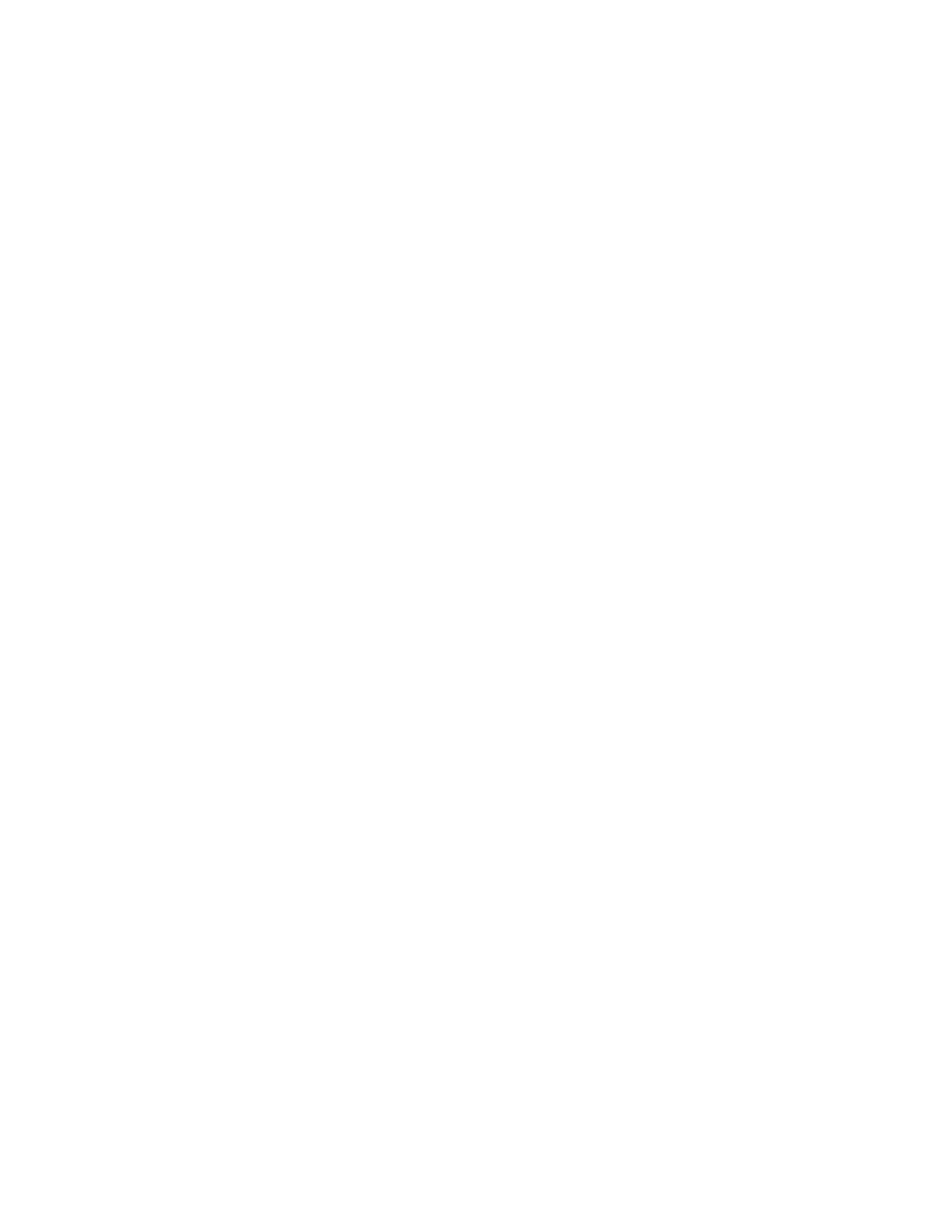
Vehicle Trajectory Optimization for Application in
Eco-Driving
Felicitas Mensing1,2, Rochdi Trigui1, Eric Bideaux2
1 IFSTTAR Bron - LTE
2 AMPERE - INSA Lyon
Abstract—To reduce fuel consumption in the transportation
sector research focuses mainly on the development of more
efficient drive train technologies and alternative drive train
designs. Another and immidiately applicable way found to reduce
fuel consumption in road vehicles is to change vehicle operation
such that system efficiency is maximized. The concept of Eco-
driving refers to the change of driver behavior in a fuel saving
way or more generally in an energy saving way.
In this paper system efficiency of a vehicle is optimized using
a dynamic programming optimization approach. Given a drive
cycle a so called ’eco-drive cycle’ is identified in which a vehicle
performs the same distance with the same stops in equivalent
time, while consuming less fuel.
I. INTRODUCTION
The transportation sector is a major contributor to air
pollution and consumer of scarce non-renewable fossil fuels
[1]. With the rising fuel prizes and environmental concerns
researchers are currently investigating new technologies to
increase fuel efficiency and reduce emissions for road vehicles.
Alternative drive train designs like the electric and hybrid
vehicles are expected to have high potentials to decrease fuel
consumption due to their ability to regenerate kinetic energy in
the braking phase. In addition, in electric vehicles the electric-
ity used can be generated from alternative, renewable energy
sources. Another approach taken to increase system efficiency
in vehicles is to improve current drive train technologies. By
increasing the efficiency of individual components in the drive
train overall system efficiency is maximized.
A third way to reduce fuel consumption of road vehicles
is to adapt driver behavior such that vehicle operation is
optimized. Here an already existing vehicle configuration is
used such that, for a desired mission, the fuel consumed is
minimized. This concept of adapting driver behavior in a fuel
saving way is often referred to as ’Eco-Driving’.
It is well known that fuel economy in road vehicles does
not only depend on the drive train but also on its operation.
This has first been demonstrated in 1977 by Schwarzkopf [2].
Since then several works have shown that optimizing vehicle
operation for a given mission can result in significant gains
in system efficiency [3], [4], [5], [6]. Another study done
by Ericsson [7] shows that certain driving patterns have an
important effect on emissions and fuel consumption.
Implementing and applying their results in real time driving
has been difficult since an interface between the optimization
and the driver has to be designed. Today several approaches to
develop eco-driving strategies can be found. In most countries
eco-driving courses are offered. But these have shown to
reduce fuel consumption only for a short time period [8].
Other eco-driving tools consist of a display, which gives the
driver advice on the optimal vehicle operation [9], or an active
accelerator pedal, which influences the rate of acceleration of
the driver by applying a resistance on the gas pedal [10].
In this work we suggest a strategy to compute a so called
eco-drive cycle, given a general drive cycle. Using numerical
optimization tools the best operation, which results in the
same trip distance, with equivalent stops, in the same final
time, will be computed for a given drive train configuration.
For verification the vehicle will be simulated in a forward
facing manner over the original drive cycle as well as over
the determined eco-drive cycle. It is expected that the fuel
consumption will be reduced from the original drive cycle to
the eco-drive cycle. In analyzing the results the potentials in
applying the suggested optimization algorithm to eco-driving
will be investigated.
In the following the system considered for optimization is
presented. In Section III the approach suggested in this work
is introduced. The method of optimization is discussed and the
generation of an eco-drive cycle, given a general drive cycle,
is explained. Results of application of the proposed strategy
in simulation will be shown in Section IV.
II. SYSTEM MODEL
The concept suggested in this paper is applicable to any
vehicle architecture: conventional, electric or hybrid drive-
train. For simplicity it will here be demonstrated on the exam-
ple of a conventional drive-train. For optimization purposes a
backward (inverse) vehicle model, where the engine operation
is computed given the operation of the vehicle, is needed.
The vehicle considered is a compact passenger car with a
mass (M) of 1020kg. The vehicle can be modeled as a standard
drive train as seen in the schematic in Figure 1 including the
final drive reduction, a 5-speed gear box, a clutch, auxiliary
losses and the engine. The engine used in this work represents
a 1.5L diesel engine with common rail direct fuel injection.
The vehicle model was constructed using the VEHLIB library,
which was previously developed at IFSTTAR [11].
In this inverse modeling approach the losses and operations
of each component is calculated in the direction opposite to
the power flow. In general the vehicle is propelled by the
engine, the power source is therefore the internal combustion
engine. Given the output of the engine the acceleration of
978-1-61284-247-9/11/$26.00 ©2011 IEEE