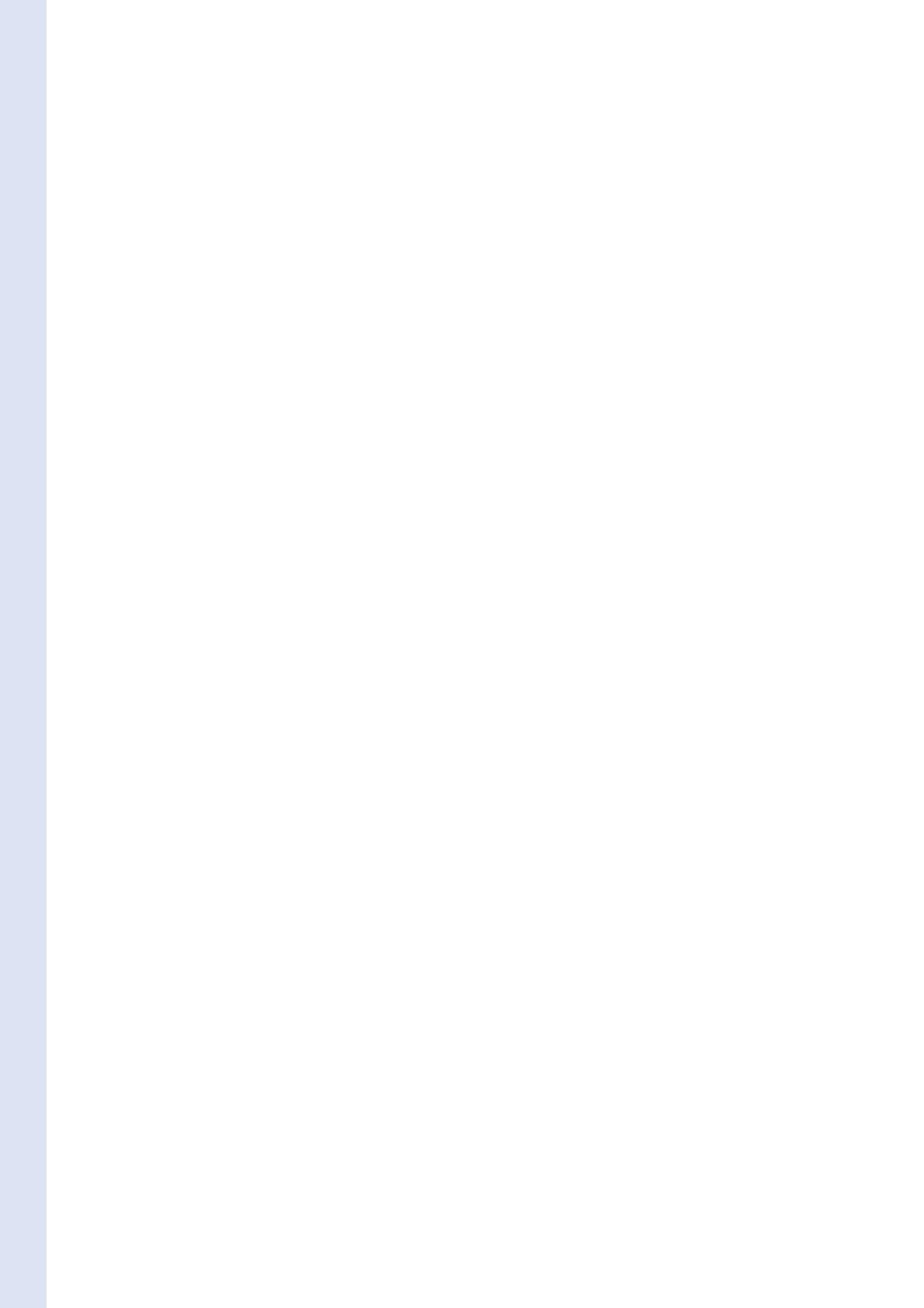
RESUME
Le présent travail de thèse s’inscrit dans le cadre d’un projet industriel proposé par une
entreprise luxembourgeoise et en collaboration avec le Centre de Recherche Public Henry
Tudor du Luxembourg (Laboratoire des Technologies Industriels (LTI)). L’objectif consiste à
mettre au point une méthode numérique de détermination de la forme des outils
d’emboutissage et du flan de pièces de précision en tôlerie fine pour que ce dernier, une fois
déformé en une ou plusieurs opérations, correspond à la définition tridimensionnelle du
cahier des charges. La méthode a pour objectif de remplacer une démarche expérimentale
coûteuse par essais–erreur.
Deux démarches numériques sont proposées, la première est relative à la détermination
de la forme du flan. Elle consiste à estimer la forme du flan par Approche Inverse en partant
de la forme 3D demandée. Puis, un logiciel de simulation incrémental par éléments finis en
3D est utilisé dans une procédure d’optimisation heuristique pour déterminer la forme du
flan. Dans la deuxième démarche, il s’agit de déterminer la forme des outils d’emboutissage
en utilisant le logiciel de simulation incrémental couplé avec une méthode de compensation
du retour élastique en 2D. La démarche numérique est validée expérimentalement dans le
cas d’un emboutissage réalisé en une ou plusieurs passes, à l’aide d’une presse manuelle,
sans serre flan et avec des outils de forme très complexe.
MOTS-CLÉS : Emboutissage, tôles minces, modélisation par éléments finis, approche inverse,
grandes déformations, comportement élasto-plastique, code incrémental, optimisation.
ABSTRACT
The present study deals with an industrial project proposed by a luxembourgian
enterprise and in collaboration with the luxembourgian research centre Henry Tudor
(Laboratory of Industrial Technologies (LTI)). The main objective is to build a numerical
approaches for the determination of the initial blank shape contour and tools shape for 3D
thin metallic precision parts obtained by stamping, knowing the 3D CAD geometry of the final
part. The purpose of the present procedure is to replace the expensive and time consuming
experimental trial and error optimization method.
Two numerical approaches have been proposed, the first is regarding the determination of
the blank shape. An estimation of the blank shape can be given using the Inverse Approach.
Update of the blank shape will then be continued by iterations combining heuristic
optimization algorithms and incremental stamping codes. The second approach is based on
precise finite element models and on spring-back compensation algorithm. The numerical
approaches are tested in the case of a special stamping process where the parts are
pressed in one or more steps using a manual press, without blank holder and by the mean of
complex shape tools.
KEYWORDS: Stamping, thin sheet, finite element modelling, inverse approach, large strains,
elasto-plastic behaviour, incremental code, optimization.
tel-00345712, version 1 - 9 Dec 2008