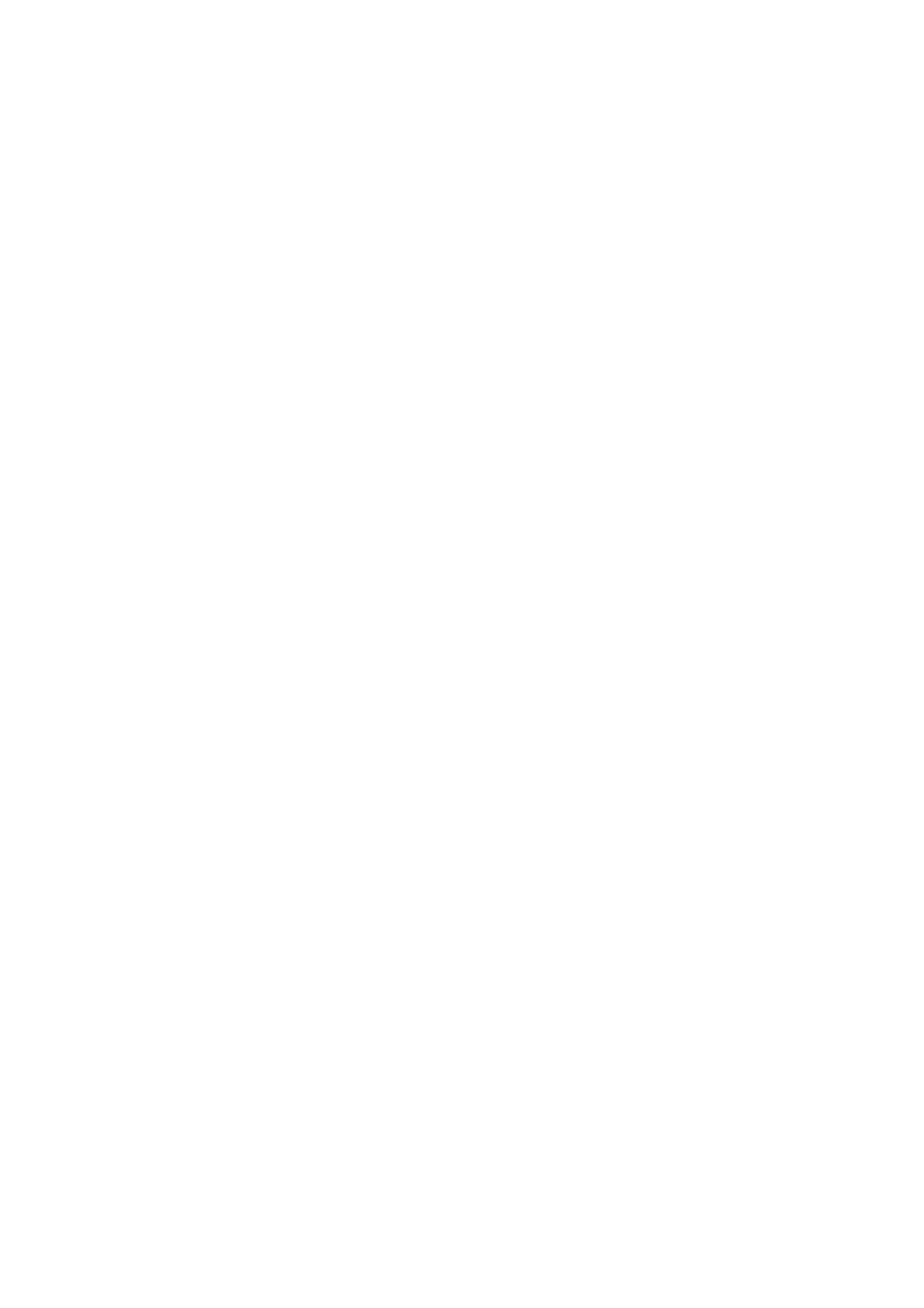
3
Remerciements
Les travaux présentés dans ce mémoire ont été réalisés au sein du groupe Intégration
de Système de Gestion de l’Energie (ISGE) du Laboratoire d’Analyse et d’Architecture des
Systèmes (LAAS) du CNRS de Toulouse et financés par le projet ANR « Superswitch ». Je
remercie Messieurs Jean Arlat et Liviu Nicu, directeurs successifs du LAAS, pour m’avoir
accueilli au sein de ce laboratoire et accordé leur confiance.
Je souhaite également remercier mes directeurs de thèse Josiane Tasselli, chargée de
recherche au LAAS-CNRS et Frédéric Morancho, professeur à l’Université Paul Sabatier
pour avoir encadré ces travaux avec beaucoup de rigueur et de gentillesse. Merci pour votre
disponibilité malgré vos emplois du temps chargés, votre soutien et votre patience.
Je tiens également à remercier Messieurs Dominique Planson, Professeur de l’INSA
de Lyon et Gaël Gautier, Professeur de l’INSA CVL, qui ont accepté la tâche d’être
rapporteur de mes travaux de thèse. Je remercie également les membres du jury, Messieurs
Théolier, Spiegel, Austin pour ce débat intéressant et constructif.
Je souhaite également remercier toutes les personnes qui ont travaillé de près ou de
loin sur ce projet, notamment les laboratoires et entreprises partenaires IMS, GREMAN et
IBS, qui ont permis, grâce à cette collaboration, l’avancement de ce projet. Je souhaite aussi
remercier le personnel TEAM de la salle blanche du LAAS, pour m’avoir formé, conseillé et
aiguillé tout au long de ces travaux dans la bonne humeur. Je remercie tout autant les
membres de l’équipe ISGE pour ces discutions scientifiques très instructives.
Je souhaite exprimer ma gratitude à mes collègues du bureau G13, et ils sont
nombreux !! :
Gaetan Touloun, l’expert Sentaurus ; Emmanuel Marcault, le juste ; Ty Mai Dinh, la
souriante ; Anaïs Ferris, la voyageuse ; Majo, la stagiaire dynamique ; Lya, la geekette et
Asma, la petite dernière. Merci à vous pour ces moments partagés dans le bureau, qui, malgré
les moments de pression et de doutes, resteront gravés comme de chouettes souvenirs.