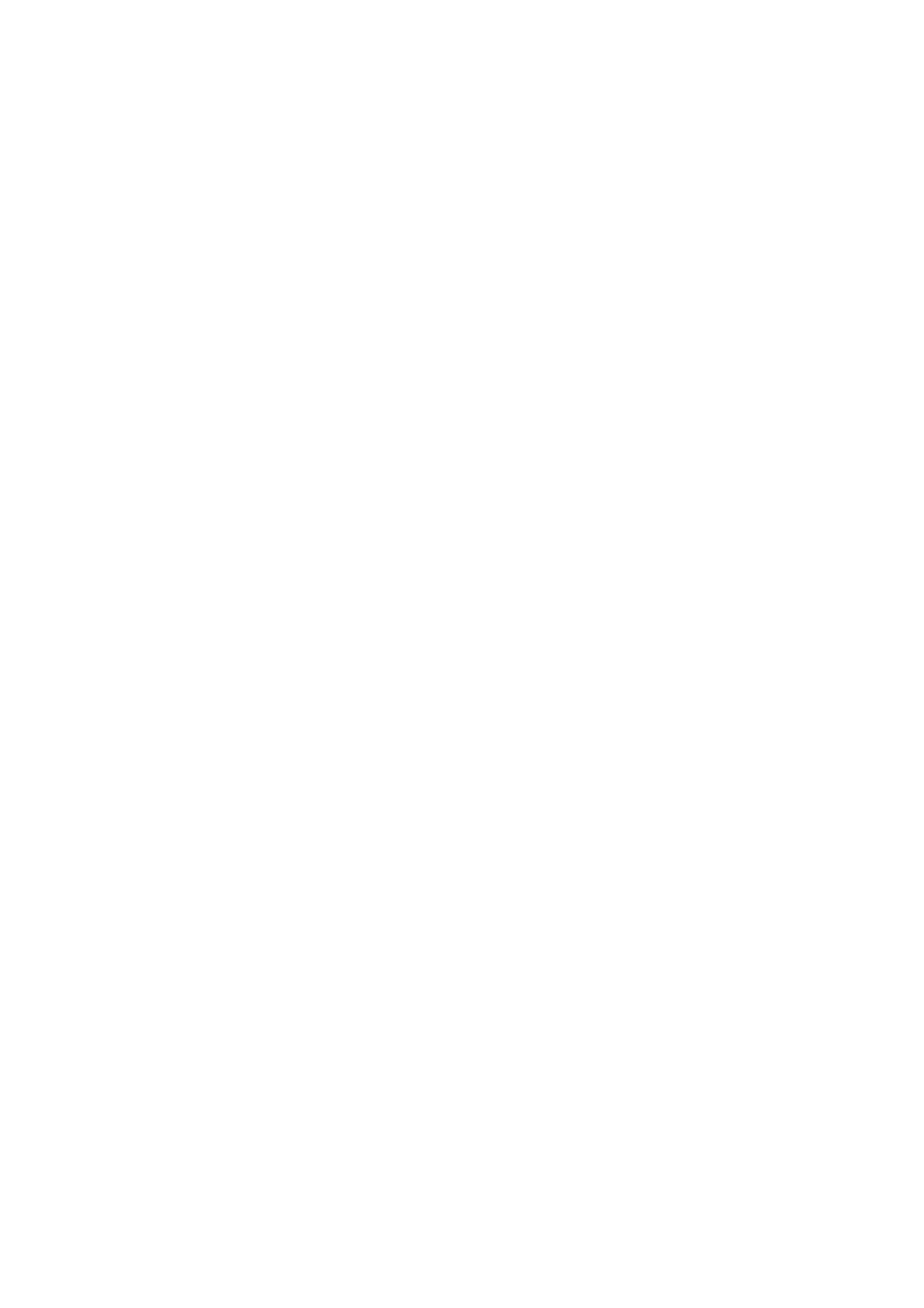
4
Résumé
Ce mémoire présente une étude sur la mise en forme spatiale d’un faisceau laser de forte
puissance dans le proche infrarouge par un élément optique diffractif. Une application en
marquage laser de codes d’identification bidimensionnels est proposée dans le cadre de cette
problématique. La faisabilité d’une telle application est examinée sous différents angles.
D’une part les sources laser à fibre peuvent actuellement proposer des faisceaux dont la
qualité à forte puissance est compatible avec l’utilisation d’un élément optique diffractif
(facteur M² proche de l’unité dans le proche infrarouge). L’étude des conditions de marquage
laser d’un matériau a conduit à la définition des paramètres du faisceau incident (puissance,
durée d’exposition) requis pour l’application proposée. D’autre part, le comportement
thermomécanique de l’élément optique diffractif exposé à de fortes puissances a été examiné.
Les déformations par expansion thermique ont été estimées et comparées aux tolérances de
fabrication du composant. Dans le cas de l’application visée, ces déformations s’avèrent
négligeables. Enfin, une méthode originale de micro-usinage laser dans l’ultraviolet d’un
matériau hybride organique-inorganique obtenu par procédé sol-gel est proposée et étudiée
pour la fabrication de l’élément optique diffractif à relief de surface. La méthode se révèle
particulièrement adaptée à la structuration de ce substrat. La fabrication d’un relief multi-
niveau a été démontrée. Le bilan de l’étude aboutit à des conclusions positives quant à la
faisabilité de l’application, notamment à l’utilisation sans détérioration d’un composant
diffractif soumis à de fortes puissances laser.
Titre en anglais
High power near infrared laser beam shaping with diffractive optics
Abstract
This doctoral thesis presents a study on the spatial beam shaping of a high power near infrared
laser by means of a diffractive optical element. An application in laser marking of two-
dimensional identification codes is proposed within the frame of this subject. The feasibility
of such an application is examined under various angles. On the one hand, fibre laser sources
can at present propose laser beams with quality at high power compatible with the use of a
diffractive optical element (M² factor close to unity in the near infrared). The study of the
laser marking conditions of a material has led to the definition of the incident beam
parameters (power, duration of exposure) required for the proposed application. On the other
hand, the thermo-mechanical behaviour of the diffractive optical element exposed to high
powers has been examined. The deformations due to thermal expansion have been estimated
and compared with the manufacturing tolerances of the component. In the case of the
proposed application, it turns out that these deformations remain negligible. Finally, an
original manufacturing method by UV laser micro-machining of an organic-inorganic hybrid
material obtained by sol-gel process is proposed and studied for the fabrication of the surface
relief diffractive optical element. The method seems particularly adapted to the structuring of
this substrate. The manufacturing of a multi-level surface relief has been demonstrated. The
study ends in positive conclusions concerning the feasibility of the application, notably for the
use without deterioration of a diffractive optical component subjected to high laser powers.