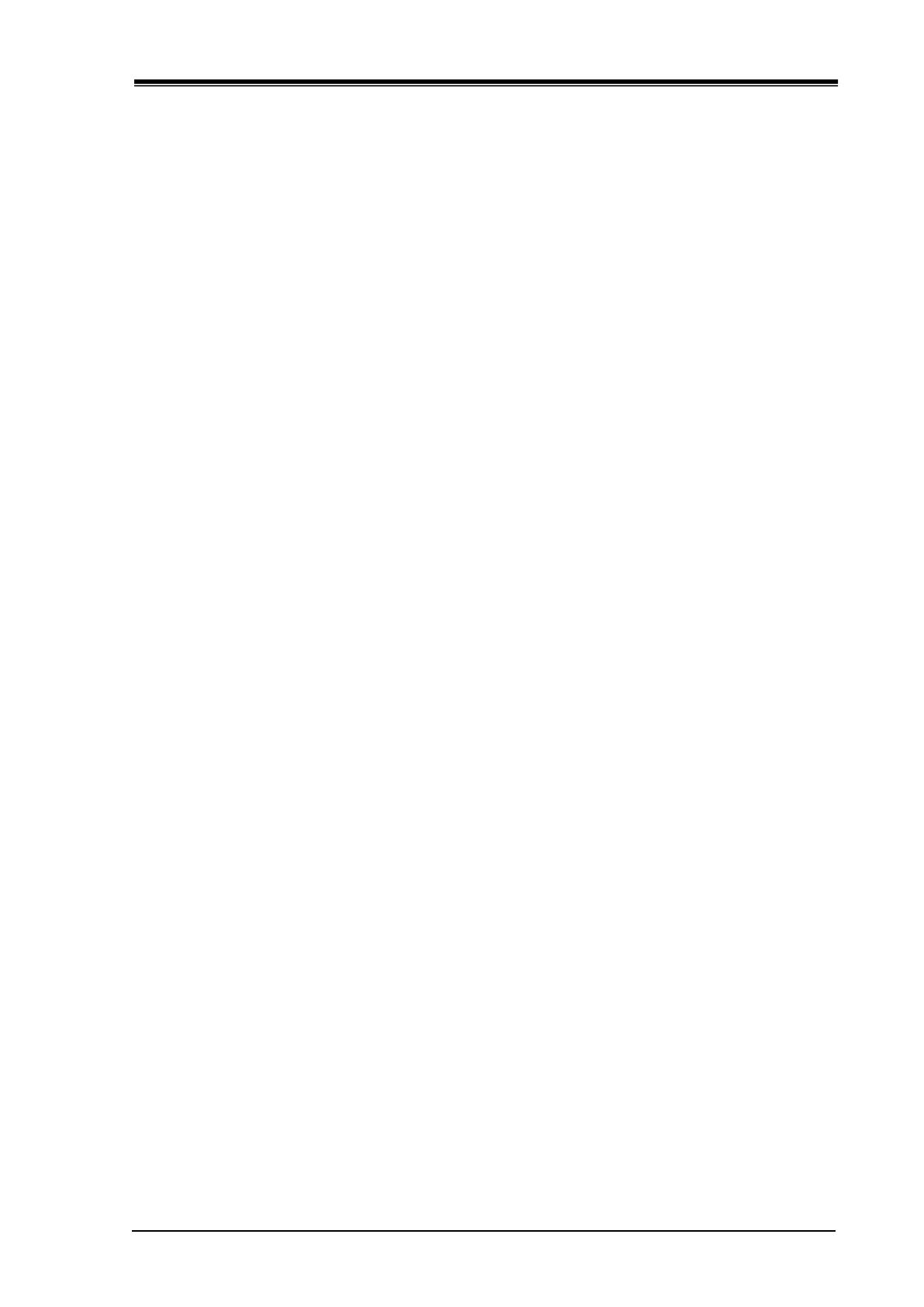
Résumé
Résumé: le travail réalisé dans cette thèse concerne l'analyse et l'étude des
possibilités d'amélioration de la fiabilité des machines électriques. Dans la première
partie, un état de l'art sur les enroulements des machines électriques suivi d'une
étude des causes et de détection des défauts apparaissant lors de leur
fonctionnement sont présentés. Suite à cela, et après avoir situé la fiabilité dans le
concept global de la sûreté de fonctionnement, un aperçu sur les conditions
d'exploitation et de fonctionnement est donné. Dans le but de pouvoir apporter des
améliorations de la fiabilité des machines électriques, des propositions basées sur
les technologies des processus de fabrication des enroulements statoriques ont été
soulignées. Aussi, des méthodes de traitement statistique portant sur la fiabilité des
machines électriques sont introduites. La seconde partie concerne , d'une part,
l'étude de l'influence des processus technologique de mise en encoches des
enroulements à deux couches sur la durée de vie de ces machines; d'autre part , et
partant du fait que les enroulements mixtes à une-deux couches sont l'une des
solutions au problème de mise en encoches automatiques des enroulements
précités, une étude approfondie de leur durée de vie est mise en évidence à travers
les résultats obtenus.
Mots clés: machine électrique, enroulement statorique, isolation, fiabilité,
tension de claquage, défaillance, durée de vie.
Abstract: the work carried out in this thesis concerns the analysis and study
of the possibilities of improving the reliability of electrical machines. In the first part, a
state of the art was presented on the windings of electrical machines followed by a
study of the causes and detection of defects appearing during their operation.
Following this, and after having located the reliability in the overall concept of
dependability, an overview of operating conditions is given. In order to be able to
make improvements in the reliability of the electrical machines, proposals based on
the technologies of the manufacturing processes of stator windings were highlighted.
Also, statistical processing methods relating to the reliability of electrical machines
are introduced. The second part concerns, on the one hand, the study of the
influence of the placement technological process of the two-layer windings on the
lifespan of these machines; On the other hand, knowing that the hybrid one-two-layer
windings are one of the solutions to the problem of automatic placement of the
aforementioned windings, a study of their lifespan is demonstrated through the
obtained results.
Key words: Electric machine, stator winding, insulation, reliability, breakdown
voltage, failure, lifespan.