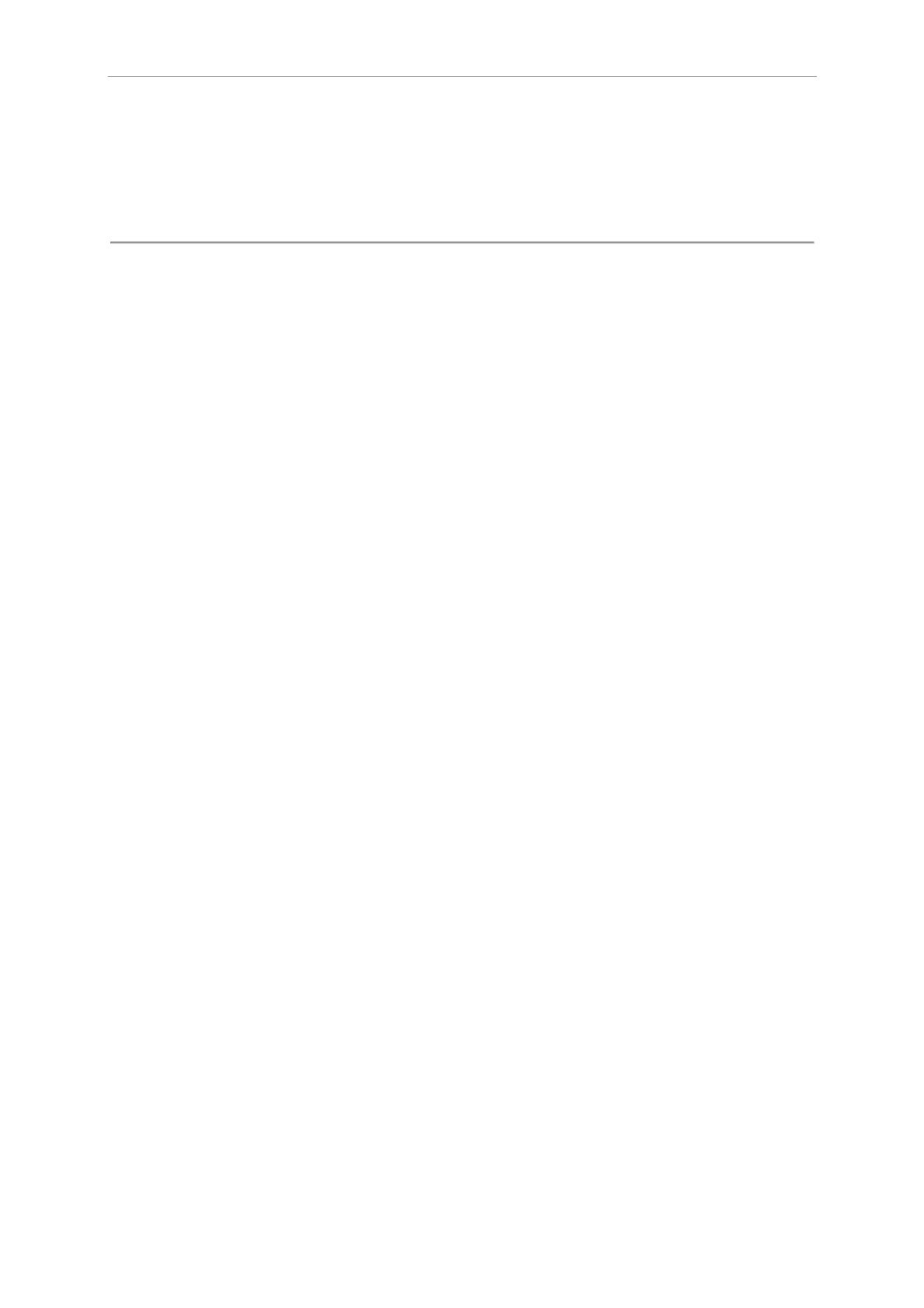
Remerciements
REMERCIEMENTS
Ce travail de thèse a été réalisé au sein de l’équipe Mécanique – Microstructure –
Oxydation du Centre Inter-Universitaire de Recherche et d’Ingénierie des Matériaux de Toulouse
(CIRIMAT – UMR 5085, CNRS/UPS/INPT) ainsi qu’au Centre Technique d’AREVA NP au
Creusot.
Je tiens à exprimer ma profonde reconnaissance à Monsieur André Pineau, Professeur à l’Ecole
Nationale Supérieure des Mines de Paris, pour l’intérêt qu’il a bien voulu porté à ces travaux et
pour avoir assuré la présidence du jury de cette thèse.
Mes plus sincères remerciements vont également à Messieurs Xavier Feaugas, Professeur à
l’Université de La Rochelle, et Peter Scott, International Expert AREVA NP, qui ont mobilisé
leur temps et leurs compétences pour examiner et juger ce travail en qualité de rapporteurs.
Je remercie également Messieurs David Delafosse, Professeur à l’Ecole Nationale Supérieure des
Mines de Saint-Etienne et Jean-Jérôme Vermoyal, expert AREVA NP, pour avoir accepté de
faire partie de ce jury.
La partie expérimentale de ce travail doit beaucoup aux compétences techniques de nombreuses
personnes à Toulouse et au Creusot. Je tiens ainsi à témoigner toute ma gratitude à Jean-Pierre
Lecomte, Hubert Pagès, Jean-Claude Salabura et Jean-Baptiste Deschamps pour leur ingéniosité
et leur disponibilité. Que soient également remerciés Bénédicte Brugier (MEB), Marie-Christine
Lafont (MET) et Claude Armand (SIMS) pour leur sympathie et leurs compétences en matière de
caractérisation des matériaux.
Au-delà du défi scientifique, la thèse est avant tout une aventure humaine… Je remercie donc très
sincèrement l’ensemble des membres des deux laboratoires (permanents, doctorants, stagiaires)
pour la qualité et la variété des échanges que j’ai pu avoir avec eux au cours de ces années et pour
l’ambiance chaleureuse qu’ils ont su entretenir. Un grand merci à l’ensemble des stagiaires qui ont
eu à me « supporter » au cours de ces trois ans, même par delà les océans : Aitziber, Benoît,
Bertrand, Catherine, Raluca, Raphaëlle, Sandrine et Sébastien. Une mention spéciale également
pour Bernard Viguier, maître ès dislocation et amateur de l’ovalie s’il en est, ainsi que pour Julitte
Huez, colocataire du premier étage et reine des fourneaux ! Merci également à Daniel Monceau et
à Claude Mijoule pour les échanges enrichissants que nous avons eus autour de la « lacune ».
Au moment de coucher sur le papier ces quelques phrases, je ne peux manquer de rendre
hommage aux trois personnes qui m’ont encadré lors de ces trois dernières années et à qui je dois
beaucoup en matière de science des matériaux. Merci donc à Dominique Poquillon pour son
enthousiasme, sa disponibilité et sa maîtrise de l’outil numérique qui ont permis d’éveiller le
mécanicien qui sommeillait en moi. Merci également à Jean-Marc Cloué, « l’industriel » de la
bande, pour m’avoir transmis une part de son savoir en matière de métallurgie des superalliages et
surtout pour m’avoir permis d’explorer aussi largement les différentes facettes du sujet qu’il
m’avait confié. Merci enfin à Eric Andrieu qui, depuis mon choix de préférer les matériaux à la
chimie organique (nul n’est parfait !), m’a accompagné et a toujours su alimenter tant ma curiosité