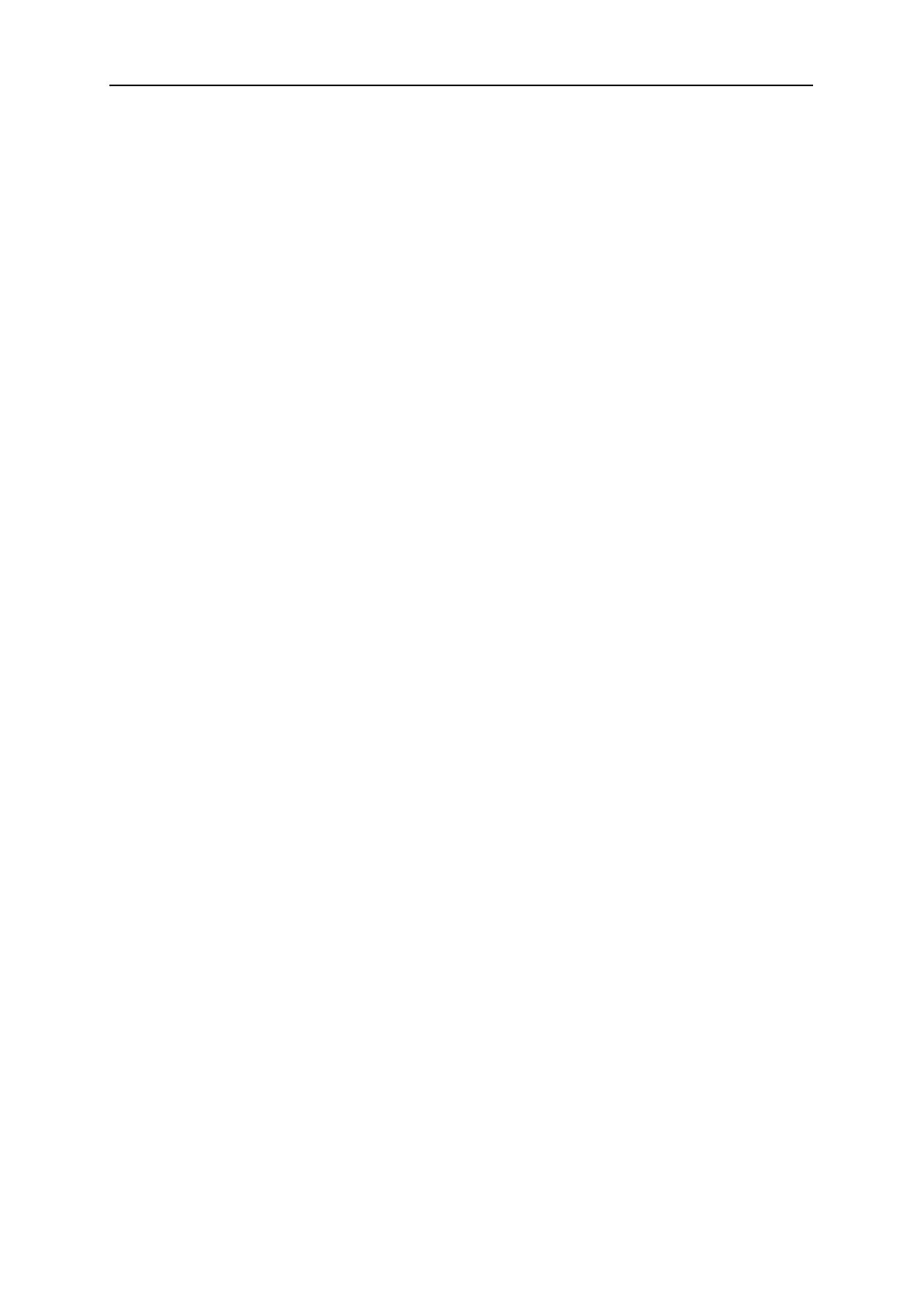
Remerciements
Je remercie Monsieur Christian LAURENT, directeur du LAPLACE, de m’avoir accueilli
dans son laboratoire.
J’adresse ma profonde reconnaissance à tout le personnel du LAPLACE de manière
générale pour la formidable ambiance de travail dont j’ai pu profiter. Je tiens à mentionner le
plaisir que j’ai eu à travailler au sein du groupe « Matériaux Diélectriques dans la conversion de
l’Energie » (MDCE) et à remercier tous les membres permanents du groupe (Jean-Pascal
CAMBRONNE, Thierry LEBEY, Zarel VALDEZ NAVA, Sombel DIAHAM, Lionel LAUDEBAT,
Marie-Laure LOCATELLI, Philippe CASTELAN, Nadine LAHOUD, Céline COMBETTES, Sorin
DINCULESCU) pour le temps qu’ils m’ont consacré au cours de ces années ainsi que leurs
conseils qui ont contribué à l’aboutissement de cette thèse.
Je tiens également à remercier à nouveau Monsieur Jean-Pascal CAMBRONNE,
responsable du groupe MDCE, mais également responsable de la formation de Master 2 recherche,
pour m’avoir donné la chance d’effectuer un Master 2 recherche dont l’orientation « matériaux
pour l’électrotechnique » a été plus qu’enrichissante.
Je remercie bien évidement tous mes collègues de bureau, passés et présents, qui ont
contribué à créer une ambiance de travail chaleureuse (pour ne faire qu’une liste des présents,
François le Patron, Trung alias Pierre, Simon le Plombier, que les anciens me pardonnent). Ces
remerciements sont également destinés à tous les collègues Doctorants et Post-Doctorants avec qui
j’ai partagé des moments dans et hors laboratoire très agréables. Une mention spéciale pour les
« MDCE » Guillaume, Laurent, Thibaut, Bang, Lumei (à votre tour), Chafé (ce qui se passe à
Cancùn reste à Cancùn), Elyse, Zenjebil, Cédric, Cyril, Louis, Enrico… mais également pour
Abder, Abdé, Lucie, Chérif, Mustapha, et les sacrés footeux Quyen et Xuan.
Pour le soutien que vous m’avez apporté tout au long de ma thèse, je vous exprime toute
mon amitié. Que les absents m’excusent, faire une liste exhaustive des personnes rencontrées est
hasardeux, mais à coup sûr j’ai pensé à vous à un moment…
Qu’il me soit permis ici de remercier l’ensemble des amis pour le soutien et les encouragements
qu’ils m’ont transmis tout au long de ces années.
Sur un plan plus personnel, je voudrais remercier l’ensemble de ma famille de m’avoir
constamment encouragé et aidé à franchir les obstacles surtout pendant les moments de doute. Que
mes parents, qui seront les seuls désignés par pudeur, y trouvent une pensée pleine d’affection. Les
mots sont insuffisants pour exprimer combien je leur suis reconnaissant… Merci est bien trop faible
pour témoigner votre impact sur l’aboutissement de cette thèse…
Que tous mes proches (qui ne seront encore là non plus pas désignés, mais ils/elles se
reconnaitront j’en suis sûr), reçoivent toute mon affection pour être restés toujours présents
pendant cette période de vie en ermite.