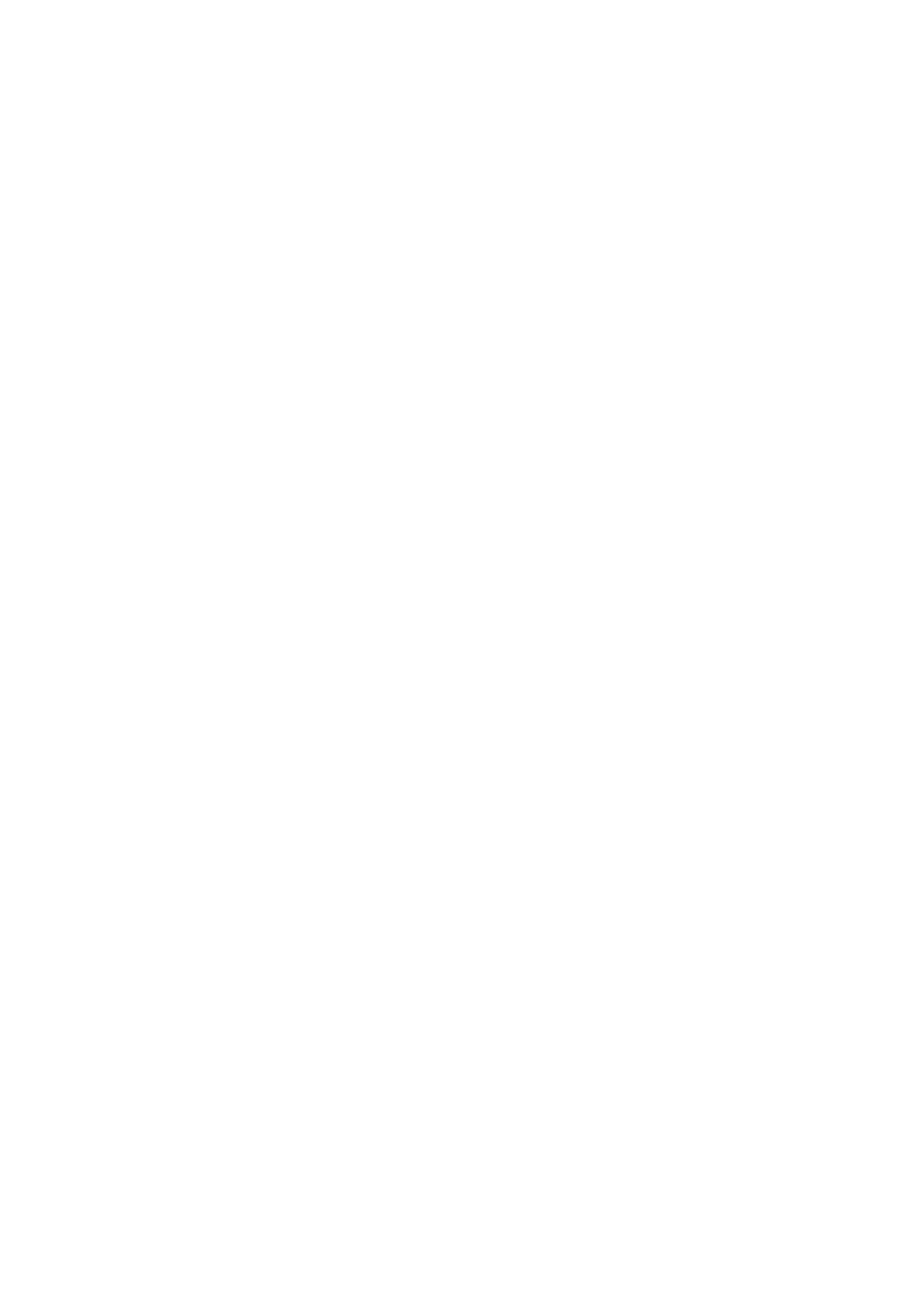
Remerciements
Les travaux décrits dans ce mémoire n’auraient jamais pu être réalisés sans l’aide de nombreuses
personnes. Je souhaite donc, à travers ces quelques lignes, leur faire part de ma sincère
reconnaissance.
Je tiens, en premier lieu, à remercier mon encadrant industriel Franck Julien pour son dynamisme,
son écoute, sa disponibilité, sa bonne humeur, son savoir sur la fabrication des composants et ses
nombreux conseils qui m’ont permis d’avancer et parfois même, de me remettre en question. J’ai
réalisé, tout au long de ces trois années d’étude, la chance d’avoir pu collaborer avec lui.
Je tiens ensuite à remercier mes encadrants académiques Pascal Masson et Jean-Michel Portal pour
leur savoir, leur disponibilité et surtout leur réactivité. Ils ont toujours, dans un temps record,
accepté de m’aider dans la rédaction des différents articles scientifiques et chapitres de ce
manuscrit. Leur soutien, partagé au travers quelques échanges téléphoniques et électroniques a été
capital. Il m’a permis d’avancer plus rapidement et plus sereinement et je ne les remercierai jamais
assez pour ça.
Je remercie vivement Laurent Lopez, grâce à qui j’ai pu être rapidement autonome sur la
caractérisation électrique des structures de test réalisées pendant ma thèse. Je le remercie
également pour sa disponibilité, ses conseils et surtout ses nombreuses discussions qui m’ont permis
de me poser les bonnes questions et de m’orienter plus rapidement vers la solution à mes
problèmes.
J’exprime toute ma gratitude aux professeurs Francis Calmon et Gérard Ghibaudo pour avoir accepté
de rapporter les travaux décrits dans ce manuscrit. Je remercie également Damien Deleruyelle qui a
accepté de présider ma soutenance de thèse.
J’exprime toute ma reconnaissance à tous les membres de l’équipe du process intégration de
Rousset, et plus particulièrement à Stephan Niel et Arnaud Regnier, avec qui j’ai eu la chance de
collaborer et d’enrichir mes connaissances. Je tiens à remercier, spécialement, Delphine Maury et
Jean-Michel Mirabel, sans qui, je n’aurai jamais pu être intégré dans l’équipe aujourd’hui. Je me dois
de remercier Bernadette Gros, qui a pris le temps de m’aider sur la prise en main des logiciels et de
partager une partie de ses connaissances, toujours dans la bonne humeur. Je n’oublie pas toutes les
autres personnes, sur qui j’ai toujours pu compter : Steph B., Julie B., Hélène D.H., Antonio S.,
Béatrice B., Eric B., Anaïs C., Jean-Marc V., Anne-Hélène C., Philippe B., Guillaume G., François P.,
Stéphane D. Enfin, je suis énormément redevable envers Catherine Marteaux, Julia Castellan et
Guilhem Bouton qui m’ont permis de réaliser et de mener à bien les études sur la réduction des
capacités BEOL et des largeurs d’actives.