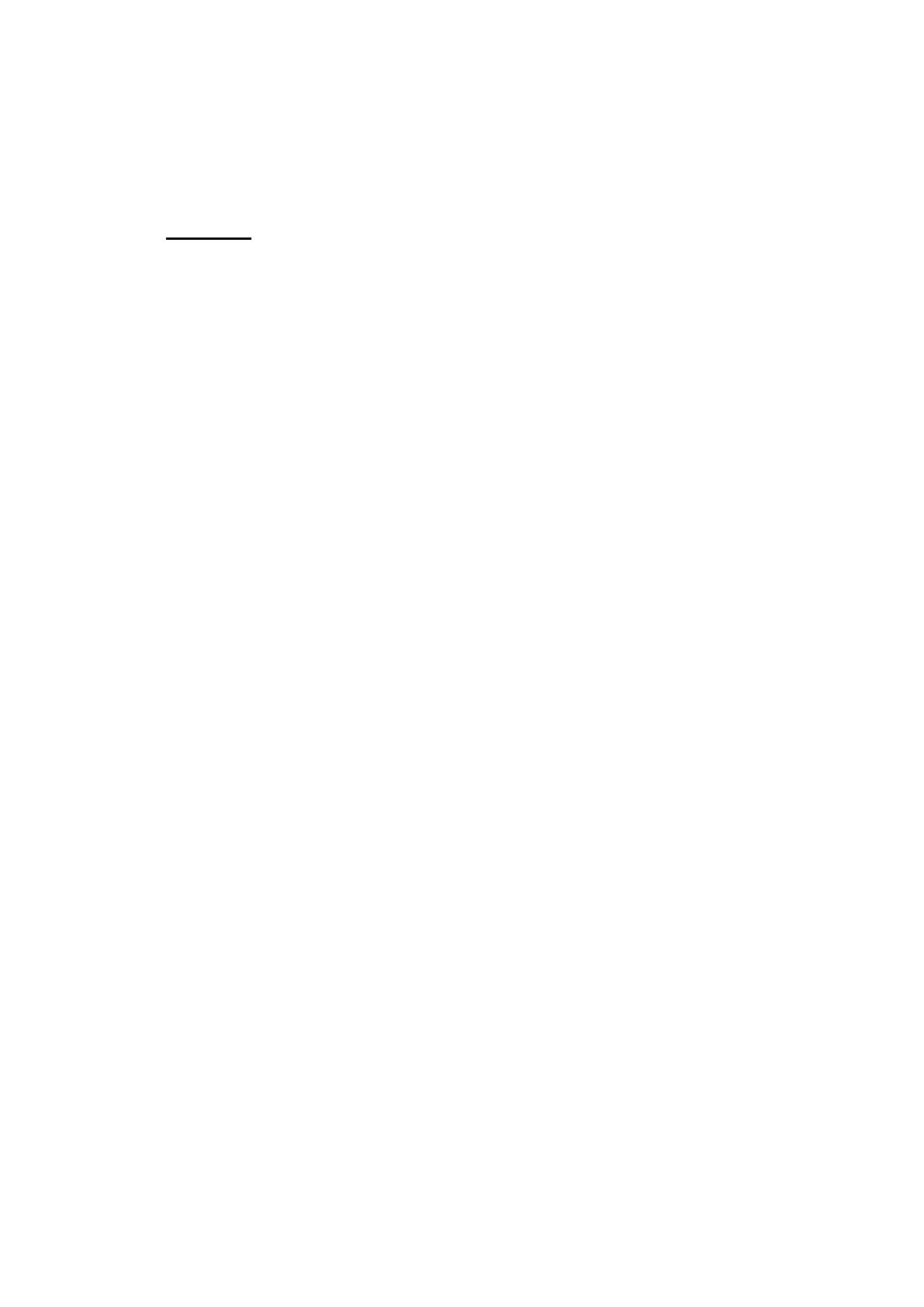
- 3 -
CHAPITRE I : PRESENTATION GENERALE
A. PRESENTATION DE L’ENTREPRISE
1. Le LNE
Fondé en 1901, le Laboratoire National de métrologie et d’Essais (LNE), à l’époque laboratoire
du CNAM (Conservatoire National des Arts et Métiers
)
, avait pour but d’effectuer des essais de
conformité pour divers domaines (thermomètres médicaux , métaux, matériaux de construction…).
En 1978, la loi Scrivener lui donne le statut d’EPIC (Etablissement Public à caractère Industriel et
Commercial).
Aujourd’hui, le LNE fournit des prestations aux entreprises dans bon nombre de domaines tels que
la métrologie, la santé, la construction, l’environnement, l’électrotechnique. Il propose une offre en
matière de conformité technique (étalonnages, essais...) d’études, de formation et de certification.
Le LNE a également des missions de service public précisées dans le cadre d’un contrat
d’objectifs signé tous les quatre ans avec l’Etat.
Elles impliquent l’engagement financier de l’Etat sous forme de subventions annuelles, qui
permettent au laboratoire :
- d’être le laboratoire national de référence, pour l’industrie, en matière de métrologie.
- de poursuivre son développement scientifique et technique pour anticiper les besoins nouveaux
en matière de mesure et d’essais, liés aux évolutions technologiques et aux attentes nouvelles de
la société dans les domaines de la sécurité, de la santé, de la qualité ou encore de la protection
de l’environnement;
- de donner une assistance technique aux pouvoirs publics et aux acteurs économiques pour
l’élaboration de nouvelles réglementations et normes aux niveaux, international, européen et
national, la mise au point de nouvelles méthodes d’essais, et la surveillance du marché.
Mon apprentissage s’est déroulé au sein d’une unité de recherche ayant pour mission d’être le
laboratoire national de référence pour l’industrie en matière de métrologie.