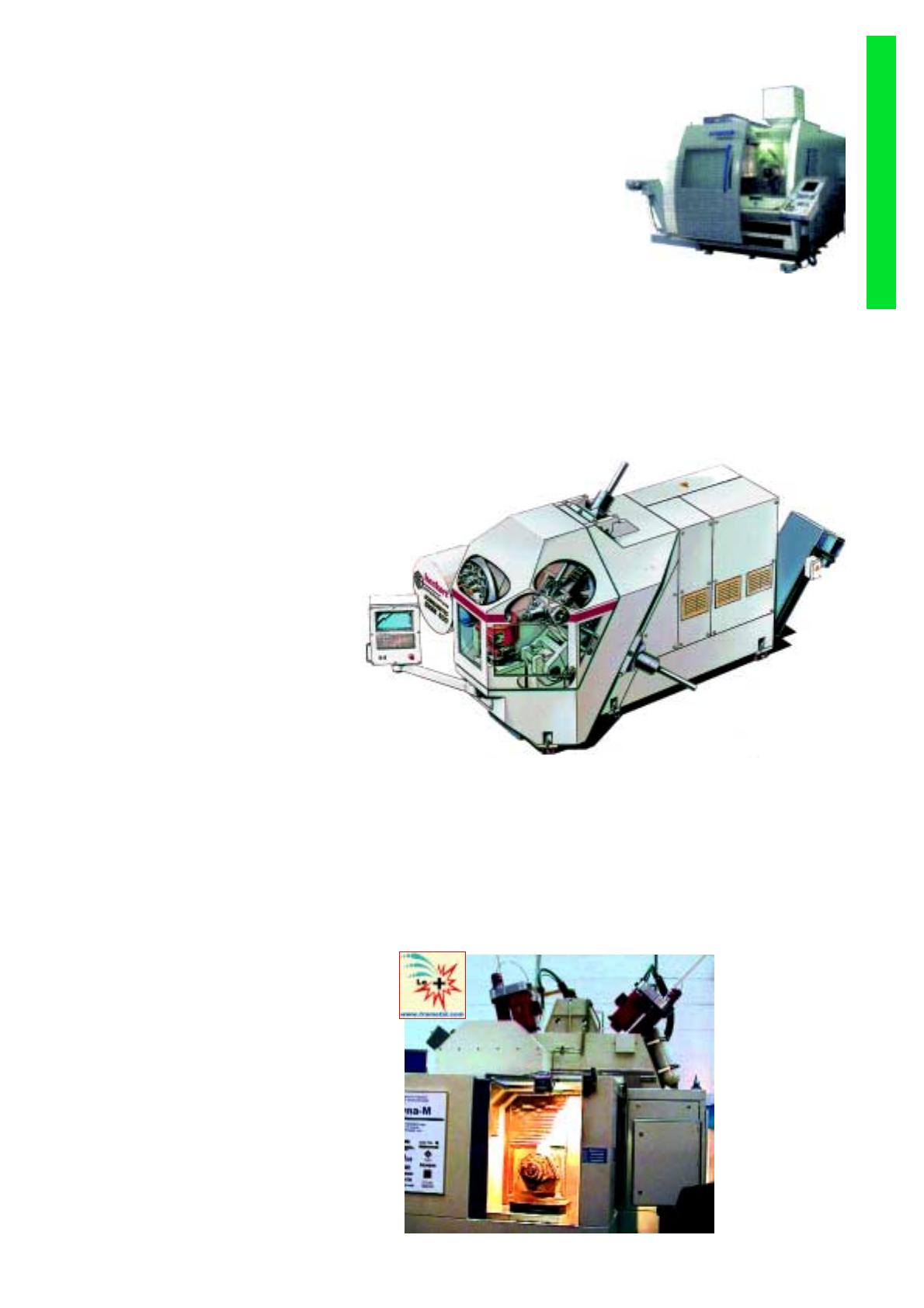
RAMETAL - Novembre 2000 - 45
MACHINES-OUTILS
sommairement (discrétion oblige) le Dr. Tho-
mas Treib, responsable technique chez Mi-
kron Machining Technology, “l’exigence d’u-
ne modularité à 3+1+1 axes est, ainsi, remplie
selon une technique appelée HPM pour High
Performance Machining (usinage à haute per-
formance). Les avantages par rapport aux
machines traditionnelles équipées d’une co-
lonne (bâti mobile, à banc ou en croix) sont
évidents: centre de gravité moins élevé, mas-
se en mouvement plus faible, deux axes d’en-
traînement en plan et donc faciles à fabriquer.
La solution, tout comme l’application chez
DaimlerChrysler, sont convaincantes: la ma-
chine est encore plus précise que les centres
d’usinage classiques, la cadence/les temps
principaux des processus définis sont infé-
rieurs de quelque 30 pour cent, les objectifs
des coûts de fabrication sont deux fois moins
élevés que les coûts générés par les centres
d’usinage traditionnels, une accélération sur
tous les axes de 2g, des avances normales/
avances rapides de 80/100 m/mn et des mas-
ses en mouvement (y compris broches) de <
1000 kg.” Aucune autre précision n’a pu être
obtenue pour le moment, hormis le fait que
l’existence en fabrication d’un tel centre
d’usinage sera transposée rapidement
dans la future génération de centres d’usi-
nage que le constructeur compte lancer
très prochainement.
Centre d’usinage à module tripode
supportant et guidant la broche
Une conception nouvelle de centre d’usi-
nage à broche horizontale est apparue avec le
modèle
SX-051
développé par H
ECKERT
(fig. 6).
Il s’est agi, en exploitant une cinématique pa-
rallèle pour l’unité porte broche, de lui confé-
rer, sous la forme d’un module autonome
SKM 400, l’ensemble des déplacements cor-
respondant aux cinq axes classiques des
centres d’usinage traditionnels afin d’obtenir
une stabilité supérieure et les performances
dynamiques à attendre de la réduction du
nombre d’éléments et d’assemblages qui
aboutit à une masse moindre et à des coûts
de construction réduits. On fera remarquer
que cette machine est l’aboutissement d’un
projet “Dynamill” de coopération auquel plus
de vingt partenaires, entreprises très connues
et universités ou Instituts ont participé dont
Alfing, Baumüller, Beckhoff, Deckel Maho,
Fraunhofer Institut, Heckert, Heidenhain, Hel-
ler, Honsberg Lamb, Ex-Cell-O, ISG, Trumpf,
Thyssen Hüller Hille, Deutsche Star, INA,
Wälzlager Schaeffler, Siemens, WZL RWTH
d’Aix-la-Chapelle, et l’Université ISW de Stut-
tgart. Le module porte-broche a été dévelop-
pé dans le but de parvenir à usiner plus
efficacement et plus économiquement toutes
pièces prismatiques de configuration “boîte”,
aussi bien en aluminium qu’en acier avec
des courses atteignant 650 mm. L’un
des avantages est la suppression ra-
dicale de tout guidage linéaire et l’une
des originalités repose dans
l’accouplement cinématique pour
guider horizontalement la broche
selon des courses correspondant
aux axes X, Y et Z. Trois modules d’axes de
longueur variable constitués d’une servocom-
mande, d’une vis à billes et d’un joint tournant
universel servent à positionner la broche. Cet-
te cinématique offre de nombreux avantages
parmi lesquels on retiendra: 1) une perfor-
mance dynamique accrue en ce qui concerne
les courses sur tous les axes avec une vitesse
montant à 100 m/mn pour une accélération à
1g permis par l’allègement des masses en
mouvement, 2) des coûts réduits dûs à la
disparition des
assemblages
comme les co
-
lonne, base, cou
-
l
lisseau, sup-
port et cou-
vre glissiè-
res, ainsi qu’à
la réduction des temps d’as-
semblage, 3) Diminution globale des temps
d’usinage grâce à l’accroissement de perfor-
mance et à une broche à haute dynamique
(31 kW et 15000 t/mn), 4) adaptabilité aisée
aux types de production envisagés avec l’uti-
lisation, soit d’une table rotative, soit d’une
table rotative pivotante pour du cinq axes, par
exemple pour l’usinage d’aubes d’une lon-
gueur jusqu’à 405 mm.
Fig. 5 - Cette
illustration de
mauvaise qualité
est la seule qu’il
a été possible de
“récupérer” du
bulletin Today de
Mikron sorti au
salon METAV.
Fig. 6 - Concept
de construction
du centre
d’usinage
Heckert à
cinématique
parallèle tripode.
Fig. 7 - Sous le
nom de Dyna M,
A. Mannesman
propose un
centre
d’usinage
à broche
horizontale
de hautes
performances
dont le module
portant et
guidant
la broche
est une unité
à cinématique
parallèle
bipode.