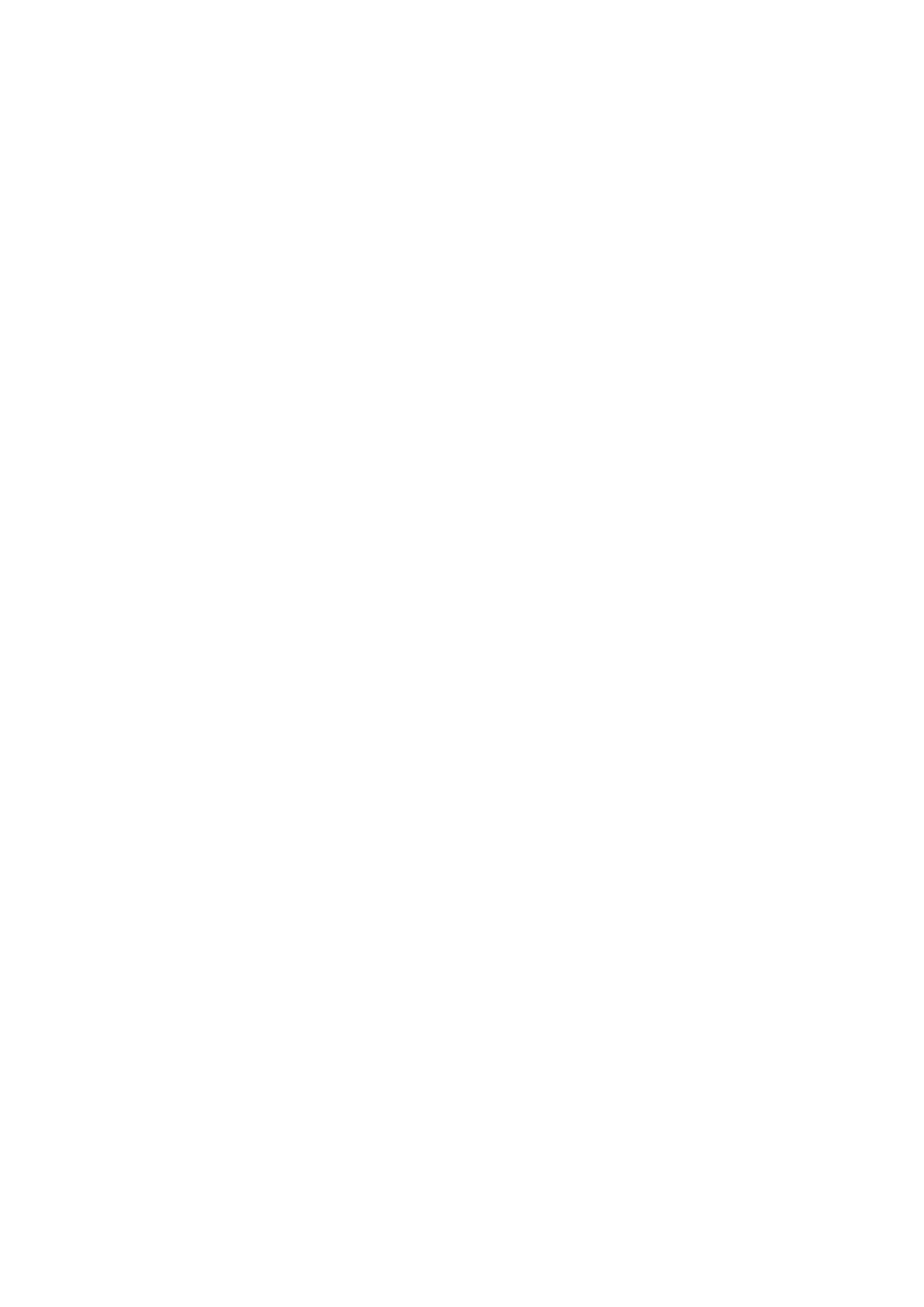
MCC - Intervention IGEE – Année 2006
2- Qui est en charge de travailler sur le règlement du problème dans l’entreprise ?
Il est nécessaire de bien connaître le fonctionnement de l’entreprise :
- dans laquelle on travaille
- pour laquelle on travaille
Que veut l’entreprise, quel est l’enjeu, quels sont les moyens dont elle dispose
pour investir ?
Dans l’entreprise :
- Chargé d’environnement
- Responsable des achats
- Responsable des travaux neufs
- Directeur
- Directeur technique
En dehors de l’entreprise :
- Agent d’une administration (DRIRE) ou d’un Ets public (Agence de l’Eau)
- Intervenant mandaté par l’entreprise (Norisko, Apave, Véritas ect…ou conseil
indépendant). Dans ce cas, un partenariat doit s’établir avec l’interlocuteur de
l’entreprise qui attend du conseil, du professionnalisme ? CE DERNIER PEUT
AUSSI ATTENDRE DU SOUTIEN VIS-A-VIS DE SA HIERARCHIE.
3- Qu’entend-t-on par connaissance du fonctionnement de l’entreprise ?
- Connaissance de l’activité de l’entreprise
- Connaissance des différents ateliers de production (micros entreprises dans
l’entreprise, atelier à la disposition d’autres, sources de pollution principales et de
pollutions annexes)
- Identification des personnes qui ont l’ancienneté et la connaissance et qui peuvent
renseigner sur les pratiques quotidiennes
- Connaissance du fonctionnement des achats (produits chimiques, produits de
nettoyage, enlèvement déchet ect…
- Identification des moyens de l’entreprise, son appartenance à un groupe ou non,
son devenir, sa situation, quels sont ses actionnaires ?
4- En découlera la connaissance de la volonté de l’entreprise :
- L’entreprise feint l’ignorance sur ce qui se passe, elle « joue la montre », jusqu’au
jour ou elle reçoit une mise en demeure de l’administration ! sa situation devient
délicate, elle va devoir agir sous la pression et dans la précipitation !
- De repousser ainsi peut conduire à des remises en cause très lourdes au plan
économique et conduire à la fermeture de l’entreprise. Cette situation n’est pas