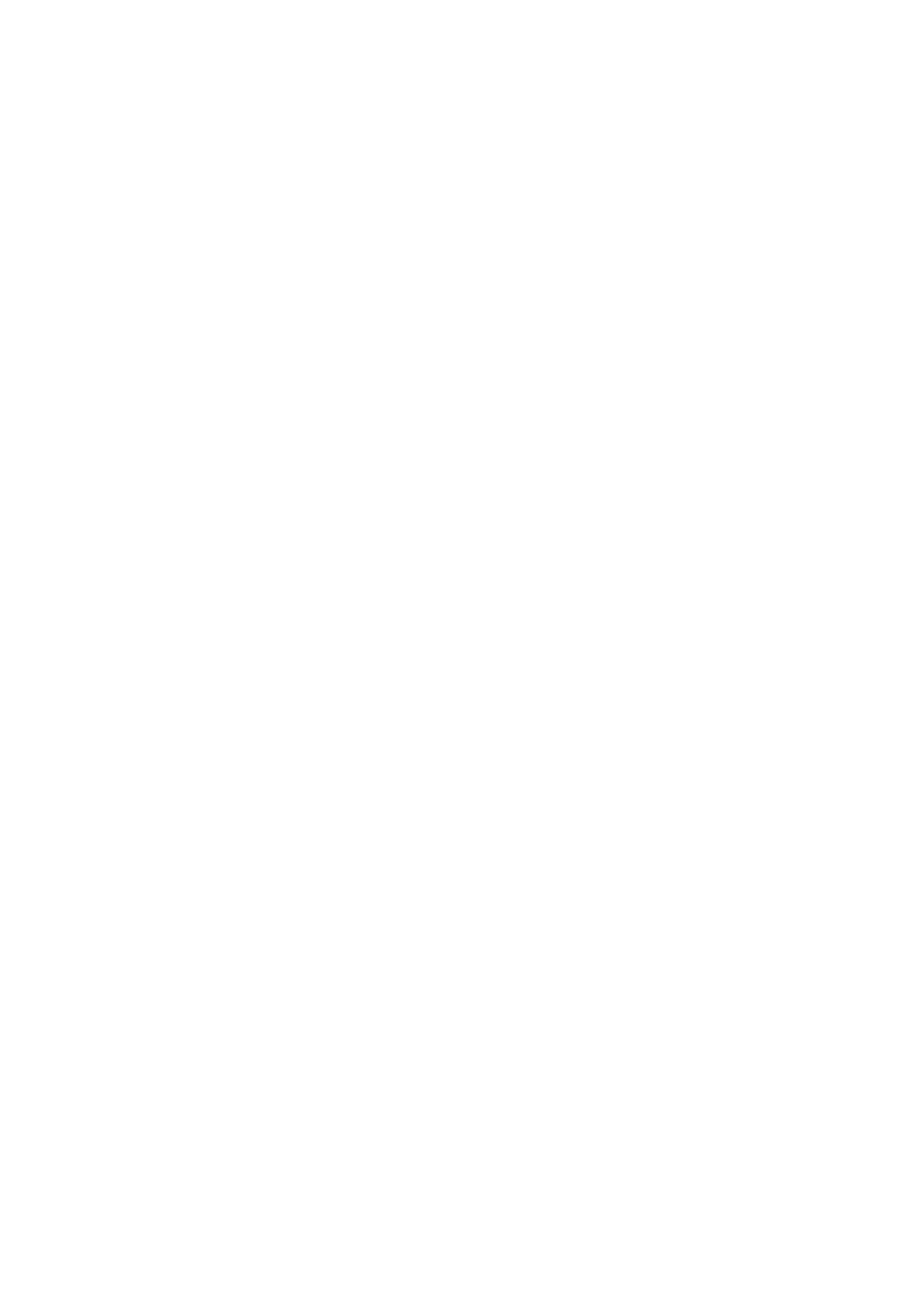
CONTENTS
INTRODUCTION............................................................................................................................................... 1
LAYOUT OF THIS REPORT................................................................................................................................... 1
BASIC FACTS: PARTICIPATING UNIVERSITY DIVISIONS AND INDUSTRY PARTNERS, STAFF, AND ECONOMIC
ACCOUNTING..................................................................................................................................................... 1
BUDGET ............................................................................................................................................................ 5
CENTRE MANAGEMENT ..................................................................................................................................... 6
HCCI ENGINE RESEARCH (ATAC ENGINE)............................................................................................. 7
SUMMARY ......................................................................................................................................................... 7
BASIC ENGINE STUDIES ..................................................................................................................................... 8
Personnel..................................................................................................................................................... 8
Multipoint Ion Current Measurements........................................................................................................ 8
LASER DIAGNOSTICS ....................................................................................................................................... 12
Personnel................................................................................................................................................... 12
Background................................................................................................................................................ 12
High speed formaldehyde visualization..................................................................................................... 14
Optical Diagnostics of Laser-Induced and Spark Plug-Assisted HCCI Combustion ................................ 19
References.................................................................................................................................................. 31
Papers published....................................................................................................................................... 31
COMBUSTION CONTROL .................................................................................................................................. 32
Persons involved........................................................................................................................................ 32
Experimental setup.................................................................................................................................... 32
Studies performed during the year............................................................................................................. 33
Future work............................................................................................................................................... 35
CHEMICAL KINETICS MODELING ACTIVITIES ................................................................................................... 36
Personnel................................................................................................................................................... 36
Full cycle simulations with coupled kinetics ............................................................................................. 36
Modeling and investigation of exothermic centers in HCCI combustion .................................................. 36
Calculations of hydroxyl radicals and formaldehyde and comparisons to LIF-measurements................. 37
NO, NO2 and N2O in HCCI combustion................................................................................................... 37
UNORTHODOX OTTOENGINE ................................................................................................................... 42
PERSONNEL ..................................................................................................................................................... 42
BACKGROUND................................................................................................................................................. 42
EXPERIMENTAL SETUP .................................................................................................................................... 42
LOAD REGIME ................................................................................................................................................. 43
INFLUENCE OF INTAKE TEMPERATURE............................................................................................................. 45
3000rpm..................................................................................................................................................... 45
4000rpm..................................................................................................................................................... 46
CYLINDER TO CYLINDER VARIATIONS AND CYCLIC INFLUENCES ................................................................... 47
SPARK ASSISTANCE ......................................................................................................................................... 49
PAPERS............................................................................................................................................................ 51
LASER DIAGNOSTICS IN CAR ENGINE................................................................................................... 52
PISTON TEMPERATURE MEASUREMENT BY USE OF THERMOGRAPHIC PHOSPHORS ........................................... 52
Introduction............................................................................................................................................... 52
Experimental.............................................................................................................................................. 52
Results........................................................................................................................................................ 54
Conclusion................................................................................................................................................. 57
REFERENCES ................................................................................................................................................... 57
TWO DIMENSIONAL EQUIVALENCE RATIO IMAGING IN FLAMES ....................................................................... 58
Calibration measurements......................................................................................................................... 58
Two dimensional imaging – Dual burner.................................................................................................. 59
Two dimensional imaging – Single burner................................................................................................ 60