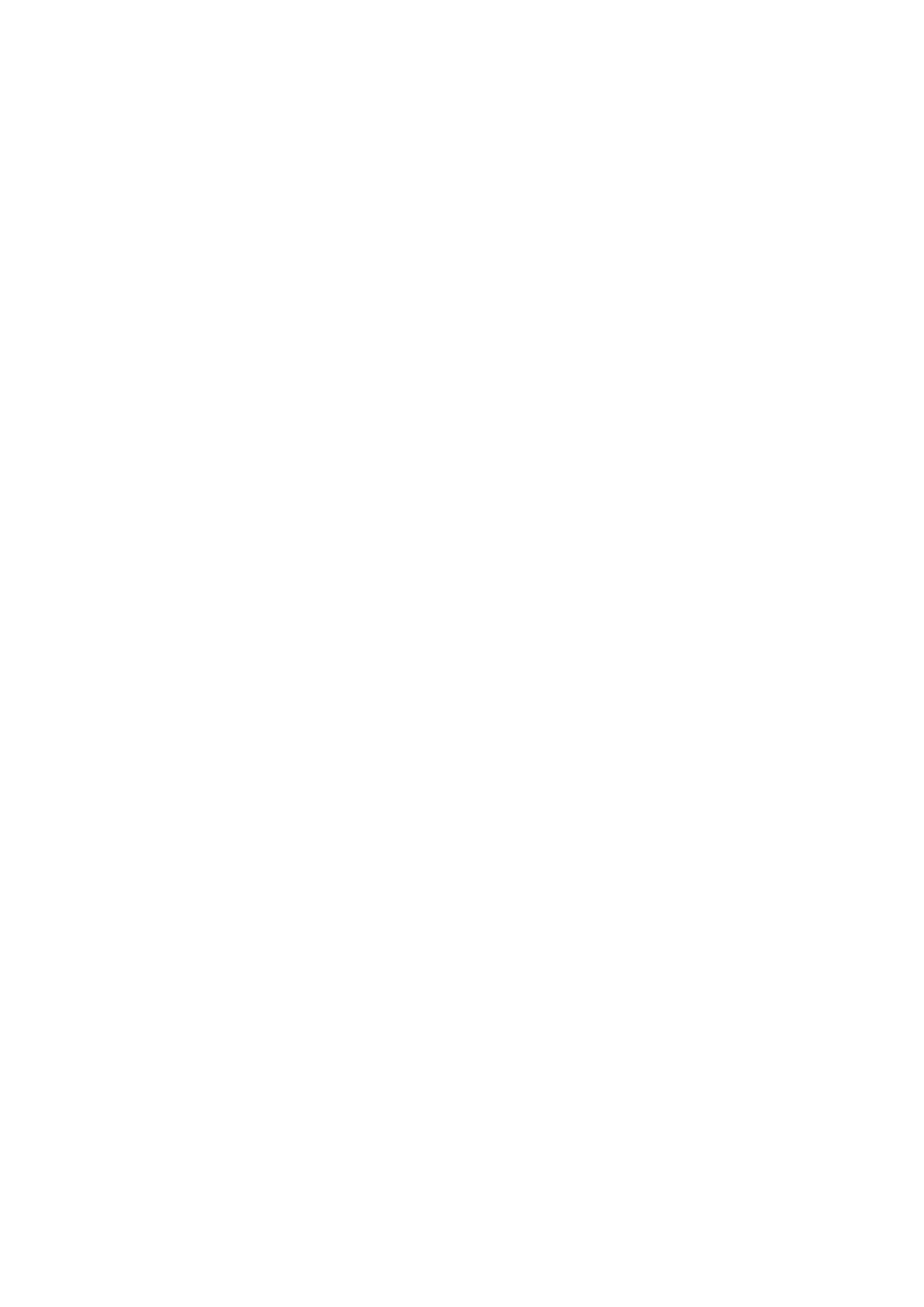
IV.4.3
IV.4.4
IV.5
IV.5.1
IV.5.2
IV.5.3
IV.5.4
IV.5.5
IV.5.6
IV.6
IV.6.1
IV.6.2
IV.6.3
IV.6.4
IV.6.5
IV.6.6
Conditions de coupe…………………………………………………………………...
Foret hélicoïdal……………………………………………………………………….
..
Détermination du temps de coupe
……………………………………………………..
Brochage………………………………………………………………………………
.
………………………………………………………………………………
……………………………………………………………………..
…………………………………………………………………...
Types de machines à brocher
…………………………………………………………..
…………………………………………………………………………...
………………………………………………………………………………
……………………………………………………………………………
Définition……………………………………………………………………………...
Structure de la rectifieuse
……………………………………………………………..
…………………………………………………………………….
Rectification de surfaces cylindriques
………………………………………………..
…………………………………………………………………..
de meules……………………………………………………………
Avantages de la rectification………………………………………………………….
34
35
36
36
36
38
38
38
39
39
39
39
39
40
42
42
V Usinage à grande vitesse
V. 2
V.2.1
V.2.2
V.2.3
V.3
V.4
V.4.1
V.4.2
V.4.3
V.4.4
Adaptation de l’usinage à grande vitesse…………………………………………….
Avantages de l’UGV
…………………………………………………………………
Haute performance
…………………………………………………………………...
Simplicité du processus
Précision et qualité
…………………………………………………………………...
Processus d’usinage CNC
Machines a commande numériques…………………………………………………
Sélection d'une machine-outil……………………………………………………….
Différents axes d’une MOCN
Transmission de mouvement………………………………………………………..
Matériaux des outils………………………………………………………………….
Conditions de coupe……………………………………………………………........
43
43
43
43
44
45
47
47
49
49
VI Usinage par Electroérosion
VI.2
VI.3
VI.4
VI.5
VI.6
VI.7
VI.8
VI. 9
VI.10
VI.10.1
VI.10.2
VI. 10.3
VI. 11
Principe physique de l’usinage par électroérosion…………………………………...
Usinage par étincelage
……………………………………………………………….
Vitesse d’usinage et état de surface
Caractéristiques électriques des étincelles…………………………………………...
Opération d’électroérosion…………………………………………………………..
Caractéristiques de l’électroérosion
Conditions d’usinage
…………………………………………………………………
Electrodes outils
……………………………………………………………………...
Diélectriques…………………………………………………………………………
Machines EDM fil et EDM enfonçage………………………………………………
Caractéristiques communes aux machines EDM…………………………………….
EDM enfonçage
……………………………………………………………………...
EDM Fil
……………………………………………………………………………...
Avantages de l’usinage EDM vis-à-vis a l’usinage traditionnel…………………….
52
52
52
52
53
53
53
54
54
54
54
55
56
VII Frittage
VII.2
VII.3
Généralités……………………………………………………………………………
Caractérisation des poudres
Procédé de frittage
……………………………………………………………………
Réactions physico-chimiques au sein du matériau…………………………………..
57
57