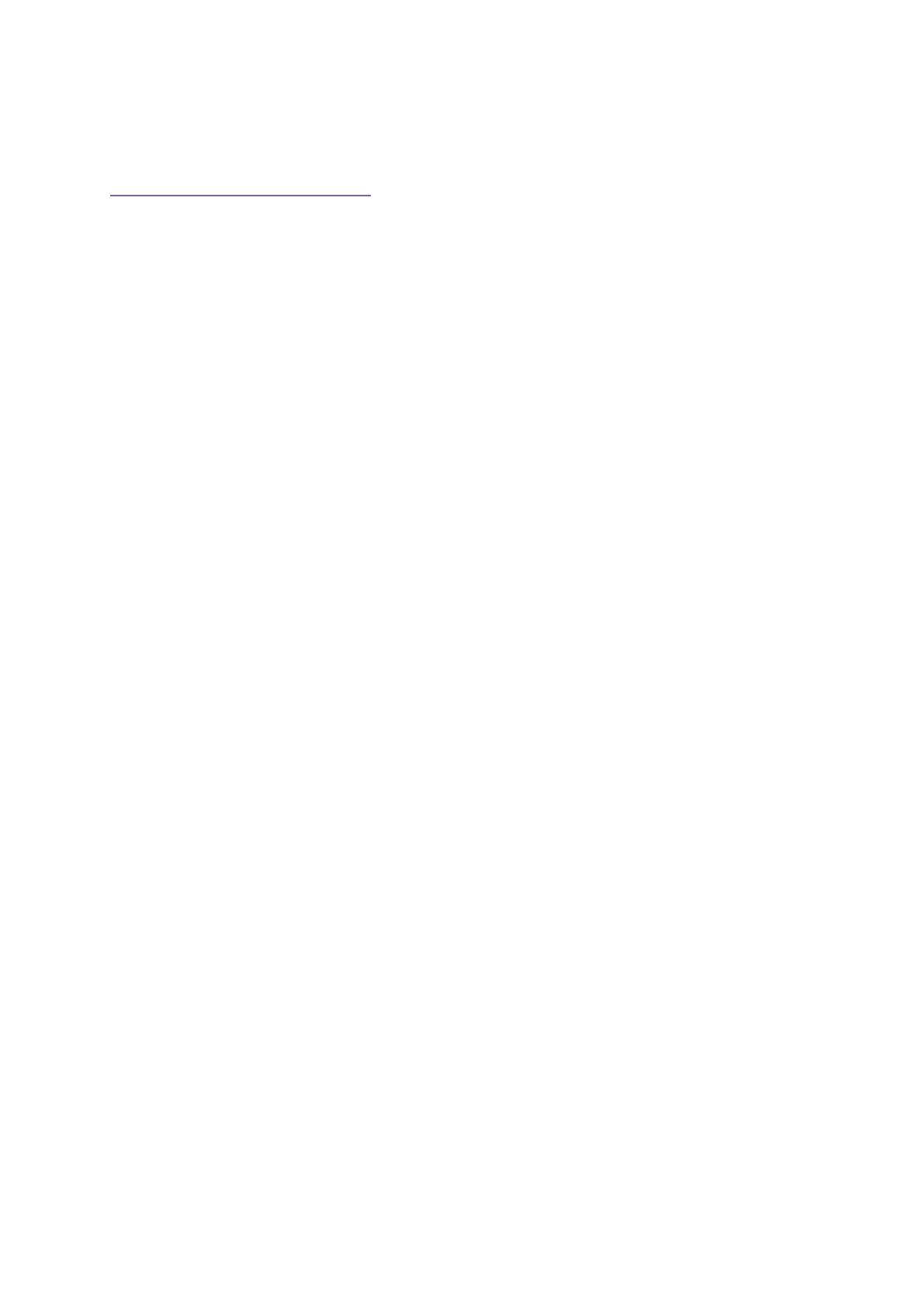
-Introduction générale
L'acide sulfurique (H2SO4) est un produit industriel de
première importance, qui trouve de très nombreuses
applications, notamment dans les batteries au plomb pour les
voitures et autre véhicules, le traitement des minerais, la
fabrication des engrais, le raffinage du pétrole, le traitement
des eaux usées et les synthèses chimiques. Au sein du
complexe Maroc Phosphore Jorf Lasfar, l’unité de production
de l’acide sulfurique joue un rôle important, tout en assurant
la totalité du besoin en acide sulfurique pour la production de
l’acide phosphorique et des engrais, ainsi qu’en vapeur pour
la production de l’énergie électrique nécessaire. Un échange
eau alimentaire-vapeur doit être assuré en continu entre
l’atelier sulfurique et la centrale, ce dit échange est
caractérisé par un problème d’écart exagéré entre les débits
déclarés par la centrale et ceux déclarés par l’atelier
sulfurique. Mon sujet consiste à étudier cet écart et ce par :
• Vérification des débits déclarés
• Lister les causes de cet écart
• Faire des actions afin de remédier à cette situation