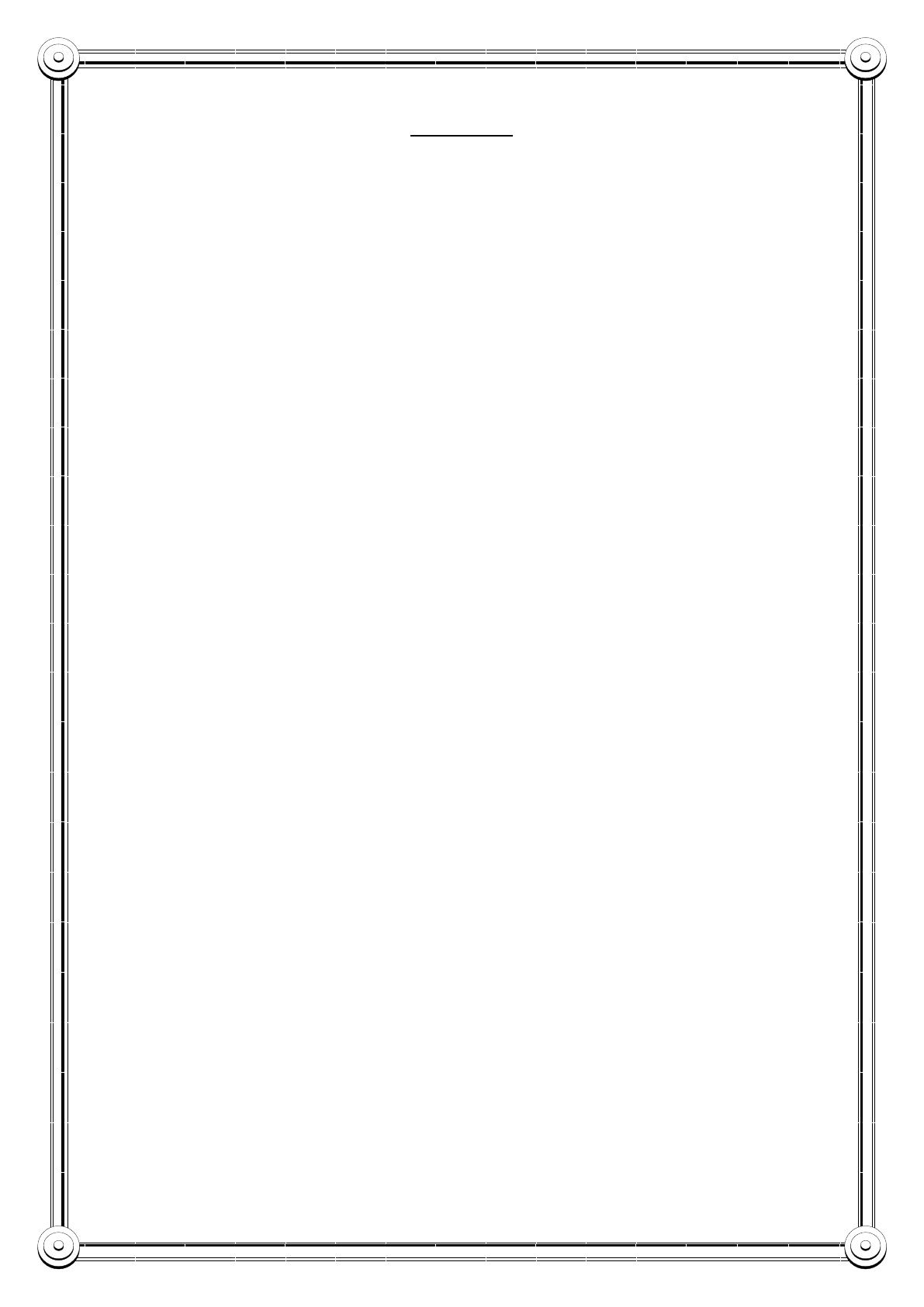
Sommaire
Dédicaces……………………………………………………………………………………………………………………………….……..i
Remerciements……………………………………………………..………………………………………………………………….. ii
Sommaire…………………………………………………………………………………………… …………………………………….iii
Tables Des figures Et tableaux……………………………………………………………………………………………….iiii
Introduction
CHAPITRE I- CONTEXTE GENERAL
I.1. Historique et situation géographique du complexe………………….……....…….…2
I.2 Présentation du SIDER TSS …………………………………...…………..…..….….4
I.2.2 Aperçu sur la TSS………………………………….……………………………4
I.2.2 Productions et utilisations ………………..…………….…….……6
I.3 Description des ateliers de production…..................................………..……………8
I.3.1 Présentation………………………………..……………………....…………..…8
I.3.2 Processus de production…………………………………………………………9
I.4 Présentation du projet…………………………………………………………..…..20
CHAPITRE II- GENERALITES SUR LES PONTS ROULANTS ET PRINCIPE DE CLASSIFICATION DES
MECANISMES DE LEVAGE ET DE DIRECTION
II.1 Différents types de ponts roulants et structures ……………………….…….……23
II.2 Eléments constitutifs du pont roulant …………………………………………….25
II.3 Différents mouvements possibles …………………………………………….……25
II.4 Principaux mécanismes des ponts roulants …………………………………….…26
II.4.1 Mécanisme de levage ………………………………………………..26
II.4.2 Mécanisme de direction ……………………………………………28
II.4.2 Mécanisme de translation ………………………………..…………29
II.5 Classement du pont roulant de l’étude ……………………………………...……30
II.5.1 Charpente……………………………………………..…….…..………31
II.5.2 Mécanismes……………………………………………………..……….32
II.5.3 Facteur de marche (FDM) et classe de démarrage ………..………..33