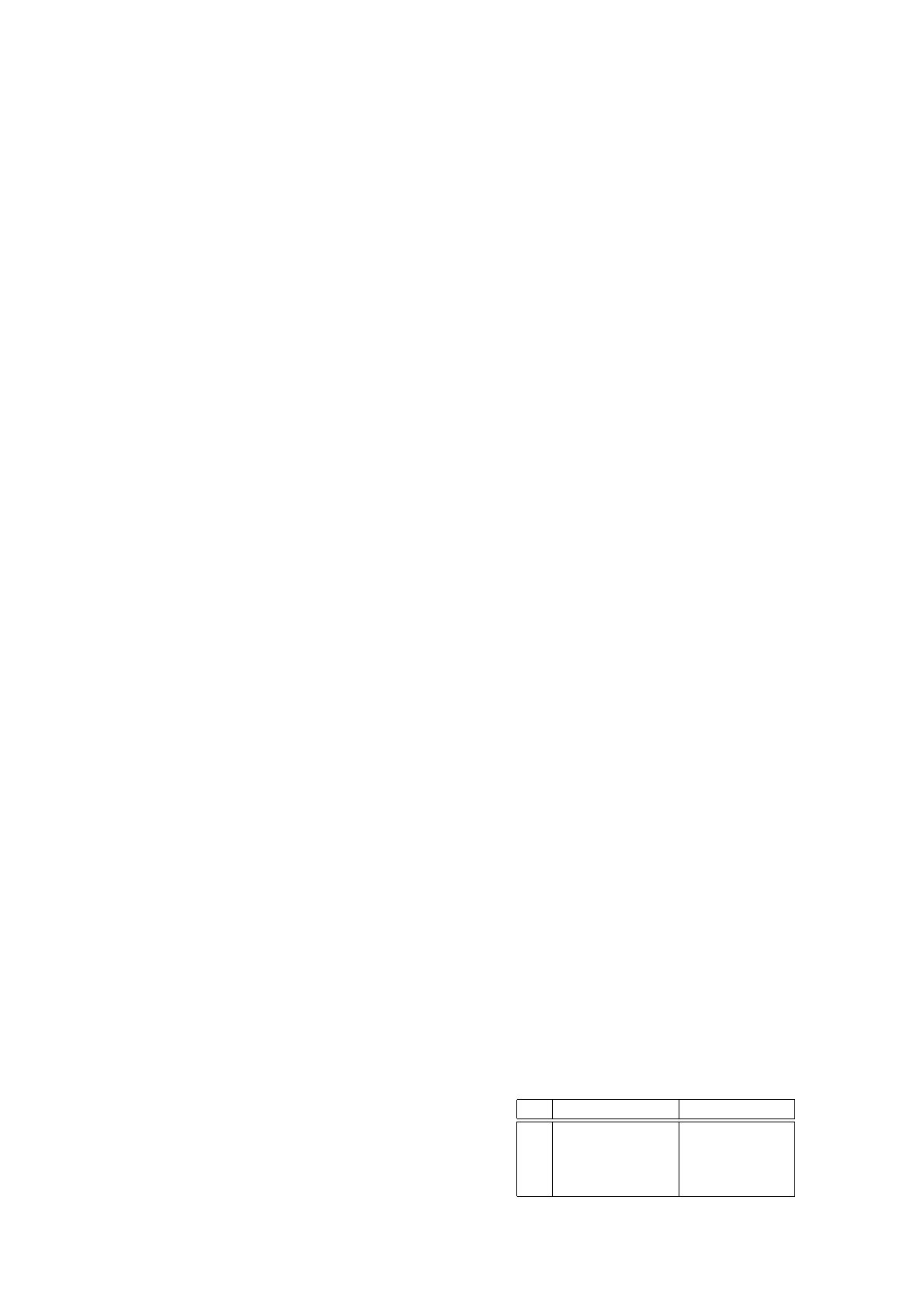
2203
Finite-States Model Predictive Control of a
Four-Level Diode-Clamped Inverter
P. Cortes(1), J. Rodriguez(1),S.Alepuz
(2), S. Busquets-Monge(2), J. Bordonau(2)
(1)Depto. Electronica. Universidad Tecnica Federico Santa Maria.
Av. Espa˜
na, 1680, Valparaiso, Chile.
(2)Dept. Electronic Engineering. Technical University of Catalonia.
Av. Diagonal 647, 08028 Barcelona, Spain.
Abstract— This paper presents a new and simple finite-
states model predictive control strategy for a four-level three-
phase diode-clamped inverter. This strategy allows for fast
load current control while keeping the balance of the dc-
link capacitor voltages. A discrete-time model of the load
and of the dc-link capacitors is used to predict the behavior
of the load current and the capacitor voltages for each
possible switching state. A cost function that considers the
load current error and the capacitor voltages error is used to
evaluate each prediction. The switching state that minimizes
the cost function is selected and applied during a whole
sampling period.
Simulation results are shown verifying the good perfor-
mance of the proposed predictive controller.
I. INTRODUCTION
Multi-level converters are considered for medium volt-
age and high power applications, and also for other appli-
cations where high quality voltages and currents are re-
quired [1], [2]. These converters have several advantages
over the traditional converters: operation with voltages
over the switching devices rating, reduced common mode
voltages and smaller voltage changes (dv/dt). Increasing
attention on these kind of converters is reflected in a large
number of publications in the last years [3], [4].
One of the most popular multi-level topology is the
diode-clamped converter, specially the three-phase three-
level neutral point clamped converter. For the control
of these converters several modulation techniques have
been proposed. Most of this techniques are based on
Pulse Width Modulation (PWM) [5], [6] and Space Vector
Modulation [7]. Modifications of the PWM strategy has
been proposed in order to guarantee dc-link capacitor
voltage balance in a four-level diode clamped converter
under any operating condition [8].
Predictive control is a very wide class of controllers that
have found rather recent application in power converters,
a classification of them is proposed in [9]. A well known
type of predictive controller is the deadbeat controller,
which has been applied for current control in three-
phase inverters [10], [11], [12], rectifiers [13], [14], active
filters[15], [16], and uninterruptible power supplies (UPS)
[17].
Model Predictive Control (MPC) is a different approach
that considers a model of the system in order to predict
the future behavior of the system over a horizon in time.
A cost function represents the desired behavior of the
system. Finite-States MPC is a simple way to use MPC
for the control of power converters taking advantage of the
discrete nature of the power converters. These are systems
with a finite number of states given by the possible combi-
nations of the state of the switching devices. By this way,
the behavior of the system is predicted for each possible
state. Then, each prediction is evaluated using the cost
function and the state that minimizes it is selected. This
approach has been successfully applied for the current
control in a three-phase inverter [18], a three-level neutral
point clamped inverter [19] and a matrix converter [20],
power control in an active front end rectifier [21], [22],
and torque and flux control of an induction machine [23].
This strategy has been also applied for current control in
a four-level three-phase diode-clamped inverter [24], but
without considering balance of the dc-link voltages.
This work proposes the use of Finite-States MPC for a
four-level three-phase diode-clamped inverter considering
current control and balancing of the dc-link capacitor
voltages.
II. CONVERTER MODEL
A diagram of the four-level three-phase diode clamped
inverter considered in this work is shown in Fig. 1. Each
output phase of the inverter can be connected to the points
0, 1, 2 or 3. The switching state of each leg of the inverter
will be represented by variables Sa,Sband Sc, where
Sx∈{0,1,2,3}, with x∈{a, b, c}.
The relationship between the switching state of one leg
Sa, the switching state of each switch of this leg, and the
output voltage in one phase is shown in the following
table:
SxSx1Sx2Sx3vx0
0000 0
1001 vc1
2011 vc1+vc2
3111vc1+vc2+vc3
978-1-4244-1668-4/08/$25.00 ©2008 IEEE