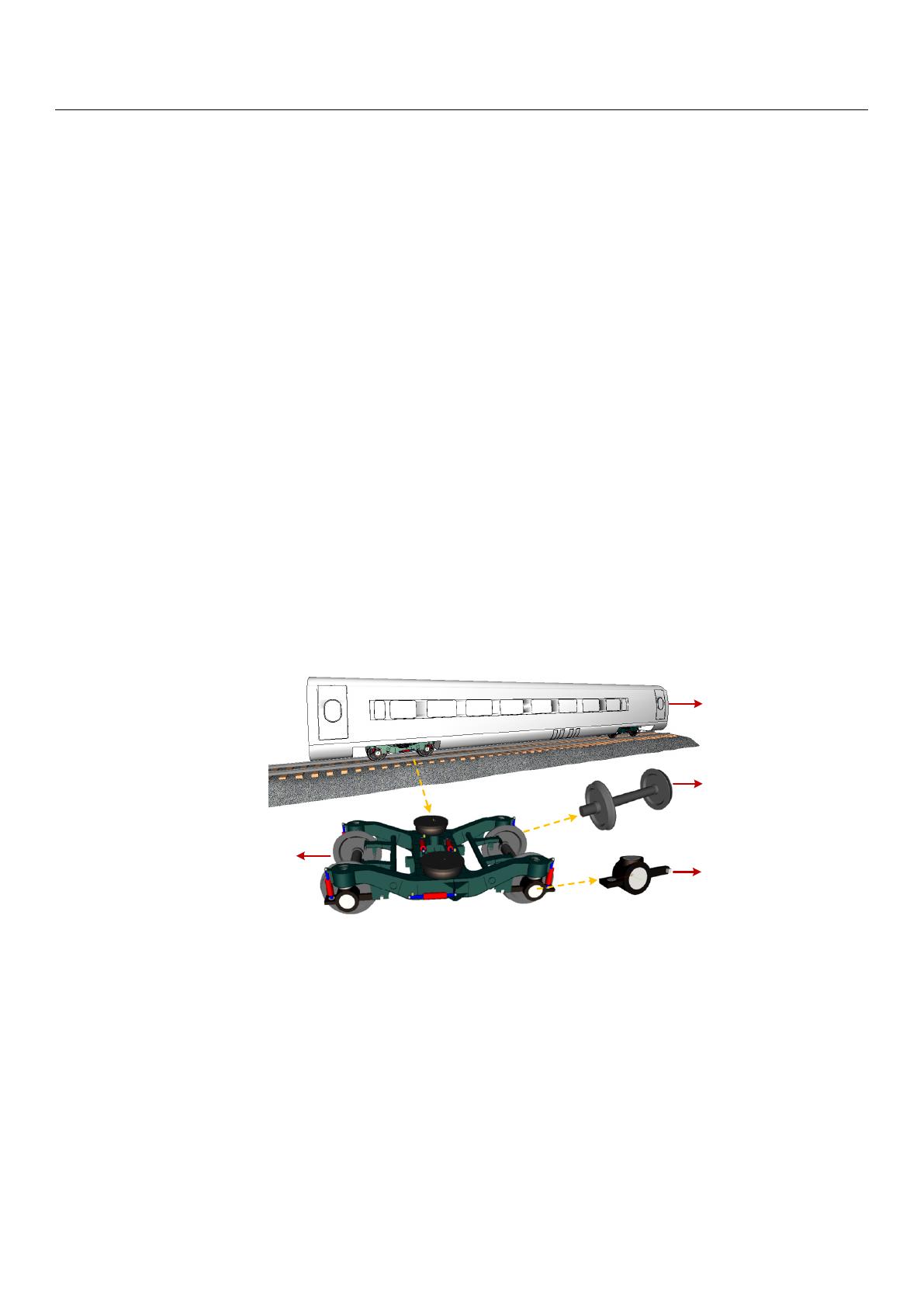
Machines 2022,10, 1024 5 of 34
the research on the influence of external excitation factors on axle box bearing is very
limited, especially in the analysis of vibration characteristics when the bearing with defects.
To address these problems, an improved vehicle-bearing coupling modeling method is
proposed in this paper. By combining Universal Mechanism (UM) with MATLAB/Simulink,
the coupling between the vehicle and the bearing is realized, and the internal forces of the
vehicle and wheel rail contact are fully considered. This model can realize fast calculation
and conveniently apply external excitation. In addition, the bearing outer ring fault, inner
ring fault and roller fault are added to the coupling model, respectively. The model is
simulated and analyzed under the actual running conditions, and verified by the rolling
and vibrating test rig of single wheelset. Since the vibration of the axle box bearing is
closely related to the movement of the vehicle and the rail, makes use of the advantage of
the coupling model, the paper studies the dynamic responses of the axle box bearing under
the impact of track irregularity and wheel flat scar, analyzes the dynamic performance
of the bearing with defects and summarizes some bearing vibration laws. The vibration
mechanism of axle box bearing under external excitation is revealed in time and frequency
domain so as to provide some reference for the research of fault diagnosis of axle box
bearing under real vehicle running environment.
2. Establishment of Vehicle-Bearing Coupling Model
2.1. High-Speed EMU Model
In the paper a vehicle model of a high-speed EMU is established through the multi-
body dynamics simulation software, Universal Mechanism (UM), as shown in Figure 1.
The model includes 1 carbody, 2 bogies, 4 wheelsets and 8 axle boxes. The carbody, bogie
and wheelset have 6 degrees of freedom, respectively, and the axle box has 3 degrees of
freedom (translation in X,Yand Zdirections). In the process of modeling, all structural
components are regarded as rigid bodies without considering their elastic deformation.
Machines 2022, 10, x FOR PEER REVIEW 5 of 35
was larger than that in the unloaded zone, which was distributed symmetrically. The
closer to the symmetry axis, the greater the impact load on the raceway.
However, in the above study, the coupling relationship between vehicle and axle box
bearing does not consider the spatial transmission characteristics of force, the model is
mostly solved by a lot of differential equation, which simplifies the internal force of the
vehicle and has low calculation efficiency. At the same time, most of the coupling models
focus on the vehicle, and there is less research on the axle box bearing itself. Furthermore,
the research on the influence of external excitation factors on axle box bearing is very lim-
ited, especially in the analysis of vibration characteristics when the bearing with defects.
To address these problems, an improved vehicle-bearing coupling modeling method is
proposed in this paper. By combining Universal Mechanism (UM) with MATLAB/Sim-
ulink, the coupling between the vehicle and the bearing is realized, and the internal forces
of the vehicle and wheel rail contact are fully considered. This model can realize fast cal-
culation and conveniently apply external excitation. In addition, the bearing outer ring
fault, inner ring fault and roller fault are added to the coupling model, respectively. The
model is simulated and analyzed under the actual running conditions, and verified by the
rolling and vibrating test rig of single wheelset. Since the vibration of the axle box bearing
is closely related to the movement of the vehicle and the rail, makes use of the advantage
of the coupling model, the paper studies the dynamic responses of the axle box bearing
under the impact of track irregularity and wheel flat scar, analyzes the dynamic perfor-
mance of the bearing with defects and summarizes some bearing vibration laws. The vi-
bration mechanism of axle box bearing under external excitation is revealed in time and
frequency domain so as to provide some reference for the research of fault diagnosis of
axle box bearing under real vehicle running environment.
2. Establishment of Vehicle-Bearing Coupling Model
2.1. High-Speed EMU Model
In the paper a vehicle model of a high-speed EMU is established through the multi-
body dynamics simulation software, Universal Mechanism (UM), as shown in Figure 1.
The model includes 1 carbody, 2 bogies, 4 wheelsets and 8 axle boxes. The carbody, bogie
and wheelset have 6 degrees of freedom, respectively, and the axle box has 3 degrees of
freedom (translation in X, Y and Z directions). In the process of modeling, all structural
components are regarded as rigid bodies without considering their elastic deformation.
Carbody
Bogie
Axle box
Wheelset
Figure 1. Dynamic model of the high-speed train.
In the vehicle model, the primary suspension includes 4 axle box positioning devices,
4 coil springs and 4 vertical dampers etc. The secondary suspension includes 2 air springs,
4 yaw dampers, lateral stops, traction rods, and anti-rolling torsion bars, etc.
Figure 1. Dynamic model of the high-speed train.
In the vehicle model, the primary suspension includes 4 axle box positioning devices,
4 coil springs and 4 vertical dampers etc. The secondary suspension includes 2 air springs,
4 yaw dampers, lateral stops, traction rods, and anti-rolling torsion bars, etc.
2.2. Axle Box Bearing Model
In this paper, the dynamic model of double row tapered roller bearing is established
through MATLAB/Simulink in which the displacement of inner ring, outer ring and rollers
in X,Yand Zdirections are considered. For the convenience of research, the modeling
process simplifies the whole bearing motion system as follows:
(1)
Regardless of the stiffness and damping of elastohydrodynamic lubrication, the
nonlinear factors in the system include the nonlinear contact force between the roller
and the outer raceway, the roller and the inner raceway, the roller and inner ring
flange, and the radial clearance between rollers and the raceways;