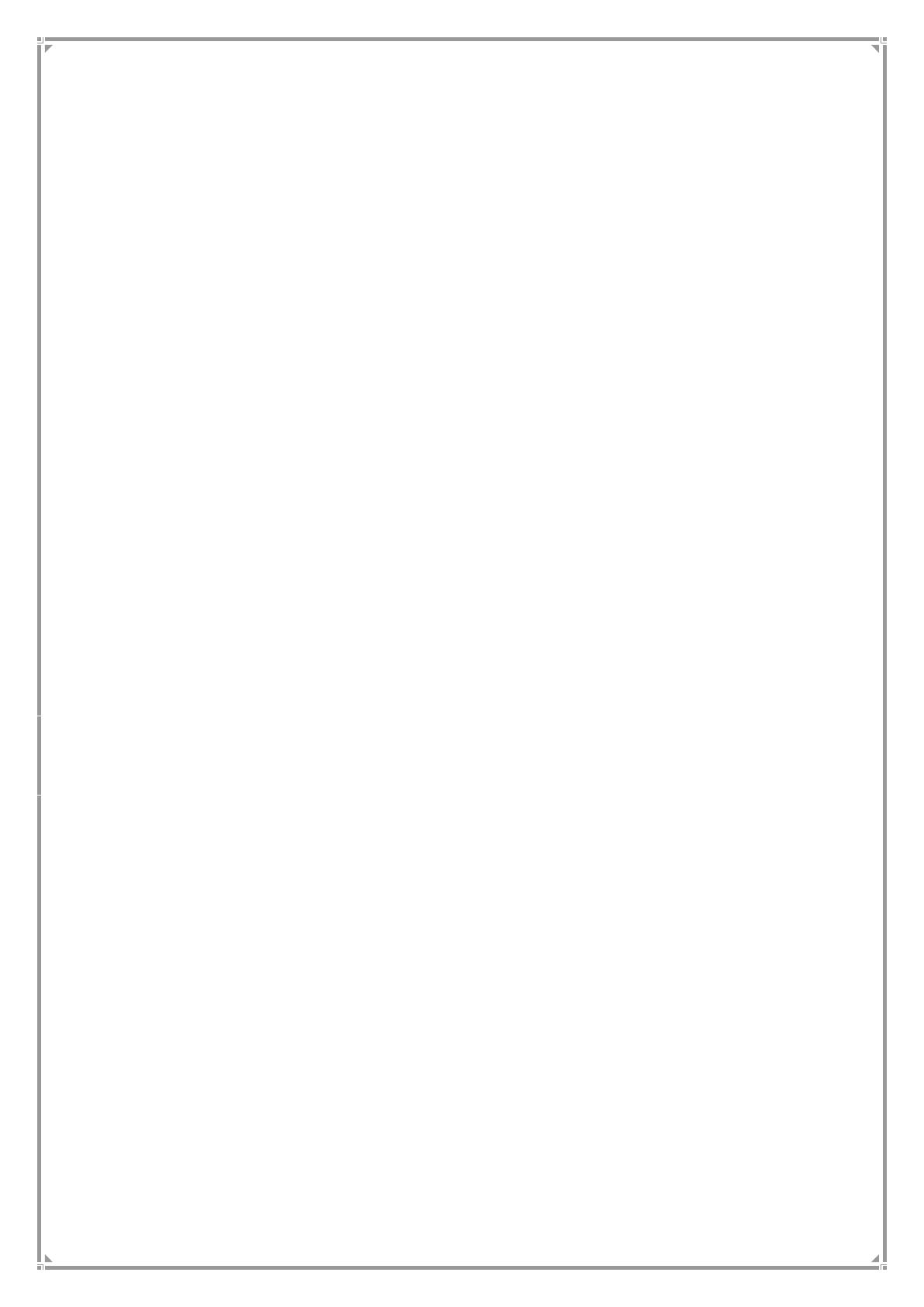
Table des matières
Chapitre 1 : Cadre du projet
1.1.Introduction générale ................................................................................................................ 1
1.2.Présentation de l’organisme d’accueil ....................................................................................... 1
1.3.Analyse Stratégique ................................................................................................................... 2
Chapitre 2 : Présentations des outils du Lean Manufacturing
2.1 .Présentation du Lean ............................................................................................................. 5
2.2 .Le Lean Manufacturing ......................................................................................................... 5
2.3. Présentation de la VMS ........................................................................................................ 6
2.3.1. Définition : ........................................................................................................................... 6
2.3.2. La production à Valeur Ajoutée : ...................................................................................... 7
2.4 .Réalisation VMS : ................................................................................................................... 7
2.4.1. Démarche à suivre ............................................................................................................... 7
2.4.1.1. Qui doit-il le réaliser? ...................................................................................................... 7
2.4.1.2. Comment doit-il le réaliser? ........................................................................................... 7
2.4.1.3. Comment recueillir de l’information? ............................................................................ 8
2.5 .Étapes de réalisation d’une VMS .......................................................................................... 8
2.5.1. Famille de produits .............................................................................................................. 9
2.5.2 .Méthode de KUZIACK ....................................................................................................... 9
2.5.3. Méthode de KING ............................................................................................................. 12
2.5.4 .Cartographie de l’état actuel et futur : ........................................................................... 15
2.5.5 .Création de la Cartographie de l’Etat existant : ............................................................ 16
2.5.5.1 .Création de la Cartographie du Futur : ....................................................................... 16
2.5.5.2 .Migration de l’existant vers la cible .............................................................................. 16
2.5.5.3 .Temps nécessaire pour réaliser une cartographie ....................................................... 16
2.6. Analyse du VMS : ................................................................................................................. 17
2.6.1 .Techniques d’amélioration continue : ............................................................................. 17
2.6.1.1 .Kaizen .............................................................................................................................. 17
2.6.1.2 .Les 5S .............................................................................................................................. 19
2.6.1.3 .Elimination des gaspillages ............................................................................................ 20
2.6.1.4 .SMED .............................................................................................................................. 22
2.7.Outils d’application de Kaizen : .......................................................................................... 25
2.7.1. Diagramme d'Ishikawa .................................................................................................... 25