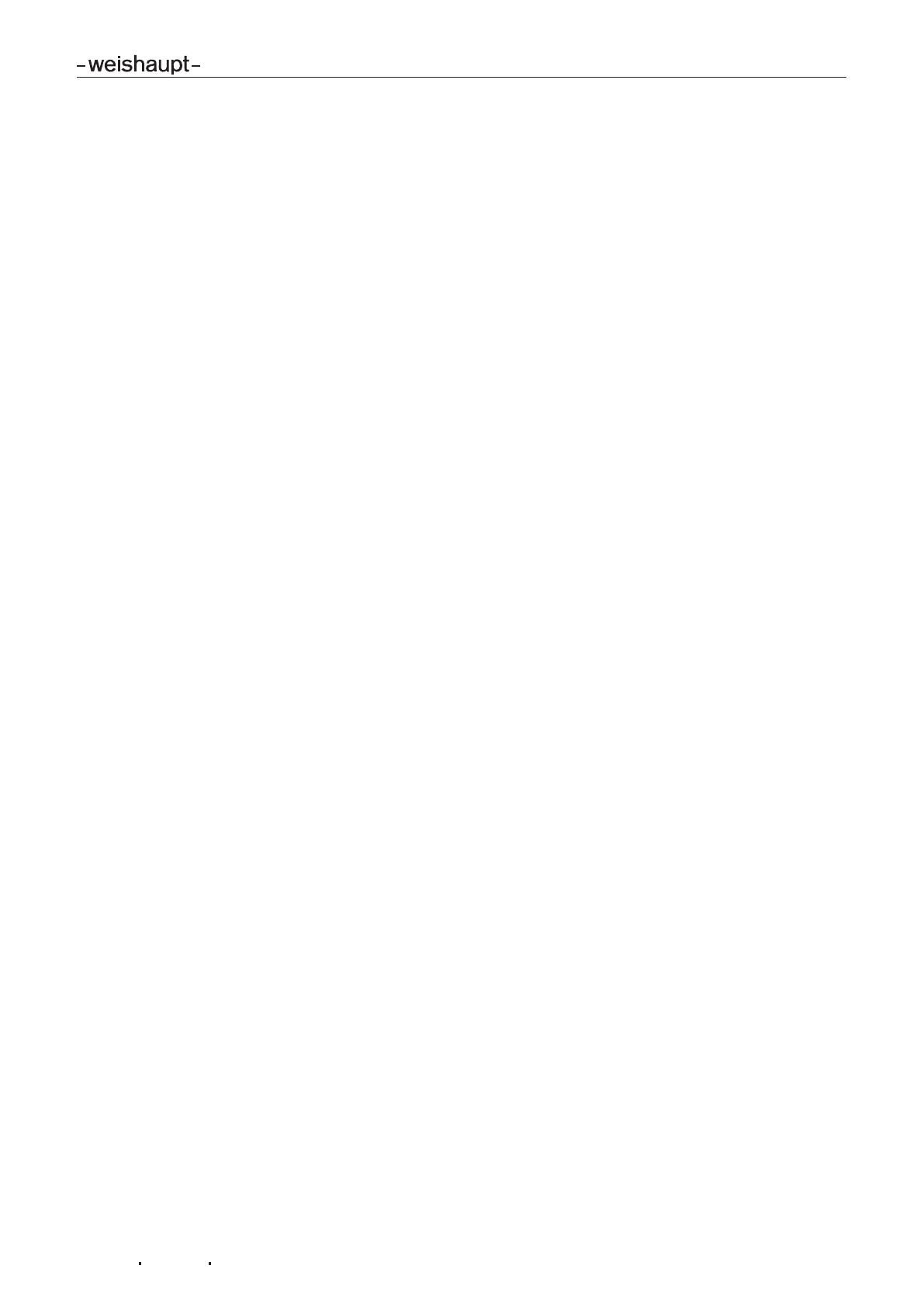
Installation and operating instruction
Oil burner WM-L20/2-A R (W-FM100/200)
83252902 1/2019-09 La 2-84
1 User instructions.............................................................................................................. 4
1.1 Target group.................................................................................................................. 4
1.2 Symbols.......................................................................................................................... 4
1.3 Guarantee and Liability............................................................................................... 5
2 Safety ..................................................................................................................................... 6
2.1 Designated application............................................................................................... 6
2.2 Safety measures........................................................................................................... 6
2.2.1 Normal operation...................................................................................................6
2.2.2 Electrical connection............................................................................................6
2.3 Alterations to the construction of the equipment ................................................. 7
2.4 Noise emission ............................................................................................................. 7
2.5 Disposal ......................................................................................................................... 7
3 Product description ........................................................................................................ 8
3.1 Type key ......................................................................................................................... 8
3.2 Serial number................................................................................................................ 8
3.3 Function.......................................................................................................................... 9
3.3.1 Air supply ................................................................................................................9
3.3.2 Oil supply............................................................................................................. 10
3.3.3 Electrical components....................................................................................... 12
3.4 Technical data.............................................................................................................13
3.4.1 Approval data...................................................................................................... 13
3.4.2 Electrical data ..................................................................................................... 14
3.4.3 Ambient conditions............................................................................................ 15
3.4.4 Fuels...................................................................................................................... 15
3.4.5 Emissions............................................................................................................. 15
3.4.6 Rating.................................................................................................................... 16
3.4.7 Dimensions.......................................................................................................... 17
3.4.8 Weight.................................................................................................................. 18
4 Installation ........................................................................................................................ 19
4.1 Installation conditions................................................................................................19
4.2 Check rating................................................................................................................20
4.3 Set mixing head..........................................................................................................21
4.3.1 Setting diagram .................................................................................................. 21
4.3.2 Set mixing head without combustion head extension ............................... 22
4.3.3 Set mixing head with combustion head extension ..................................... 24
4.4 Burner installation ......................................................................................................26
5 Installation ........................................................................................................................ 28
5.1 Oil supply.....................................................................................................................28
5.2 Electrical connection.................................................................................................30
6 Operation .......................................................................................................................... 32