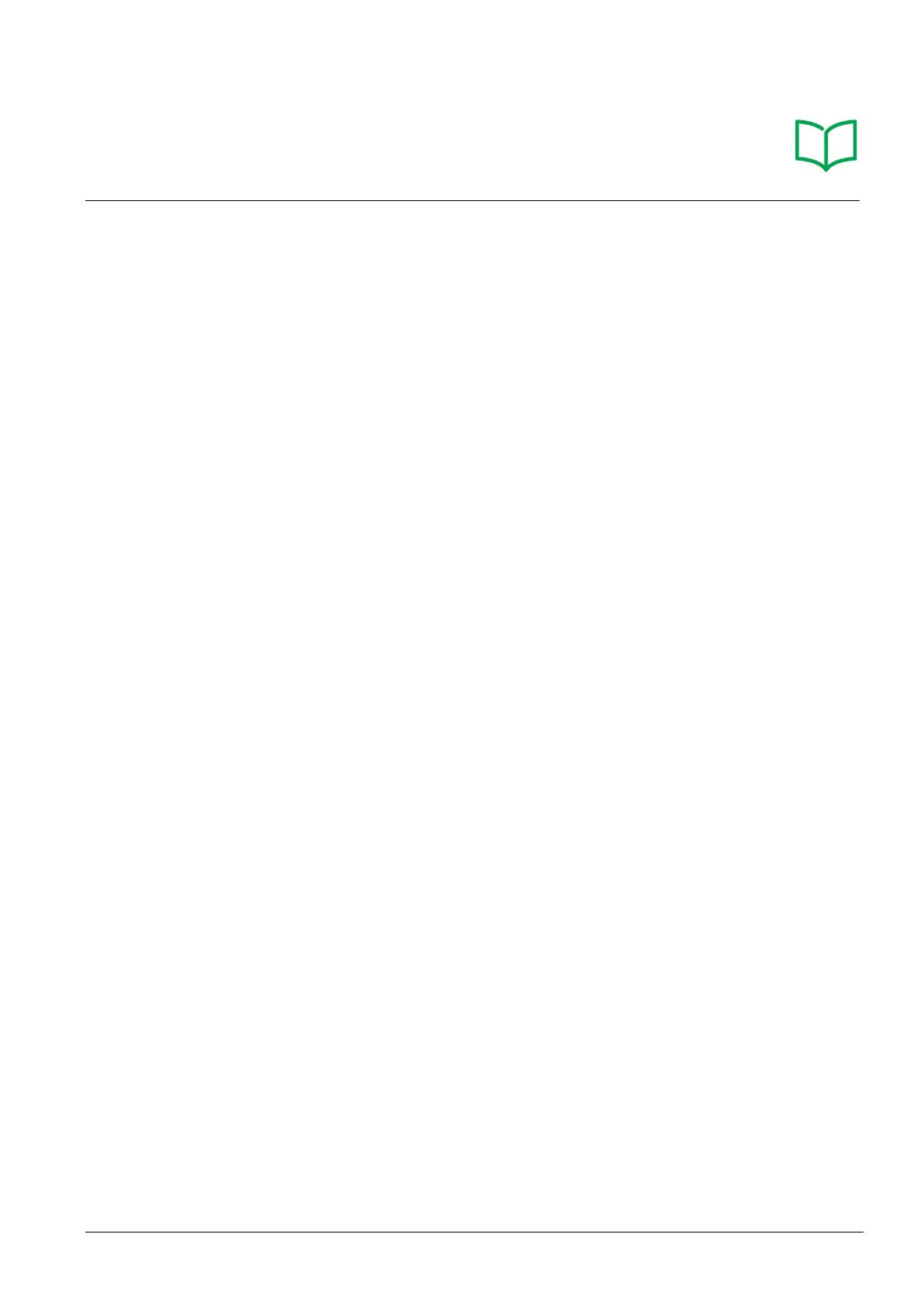
NHA80973 05/2019 3
Table of Contents
Safety Information ................................................................................................ 5
About the Book ..................................................................................................... 9
Part I Introduction ............................................................................................... 12
Scope and Purpose of Application Note .............................................................................................. 13
General Overview of Hoisting .............................................................................................................. 15
Classification of Cranes....................................................................................................................... 19
Part II Requirements, rating and sizings............................................................ 21
Prerequisites for Sizing ....................................................................................................................... 22
General Information of the Sizing of Altivar Drives .............................................................................. 23
General Information on the Sizing of Braking Resistor ........................................................................ 26
General Information on the Sizing of Cable Length ............................................................................. 28
General Information on the Sizing of Associated Components ........................................................... 31
Part III Wiring Diagrams ....................................................................................... 33
Introduction ......................................................................................................................................... 34
Wiring Diagrams .................................................................................................................................. 35
Part IV Configuration of the Drive ........................................................................ 38
Configuration overview ........................................................................................................... 39
Prerequisites for the Configuration ........................................................................................ 40
Factory Settings .................................................................................................................................. 41
Expert Level Access ............................................................................................................................ 42
System Units Customization ............................................................................................................... 43
Application Selection ........................................................................................................................... 44
Basic Configuration ................................................................................................................. 45
Motor Configuration ............................................................................................................................. 46
Motors in parallel Configuration ........................................................................................................... 48
Configuration of the Motor Thermal Monitoring ................................................................................... 51
Configuration of the Encoder ............................................................................................................... 53
Configuration of the Reference Speed and the Preset Speed............................................................. 54
Configuration of the Direction for the Vertical Movement .................................................................... 55
Configuration of the Direction for the Horizontal Movement ................................................................ 57
Optimization of the Configuration .......................................................................................... 60
After the First Movement ..................................................................................................................... 61
Optimization of the Brake Logic Control .............................................................................................. 62
Acceleration and Deceleration ............................................................................................................ 68