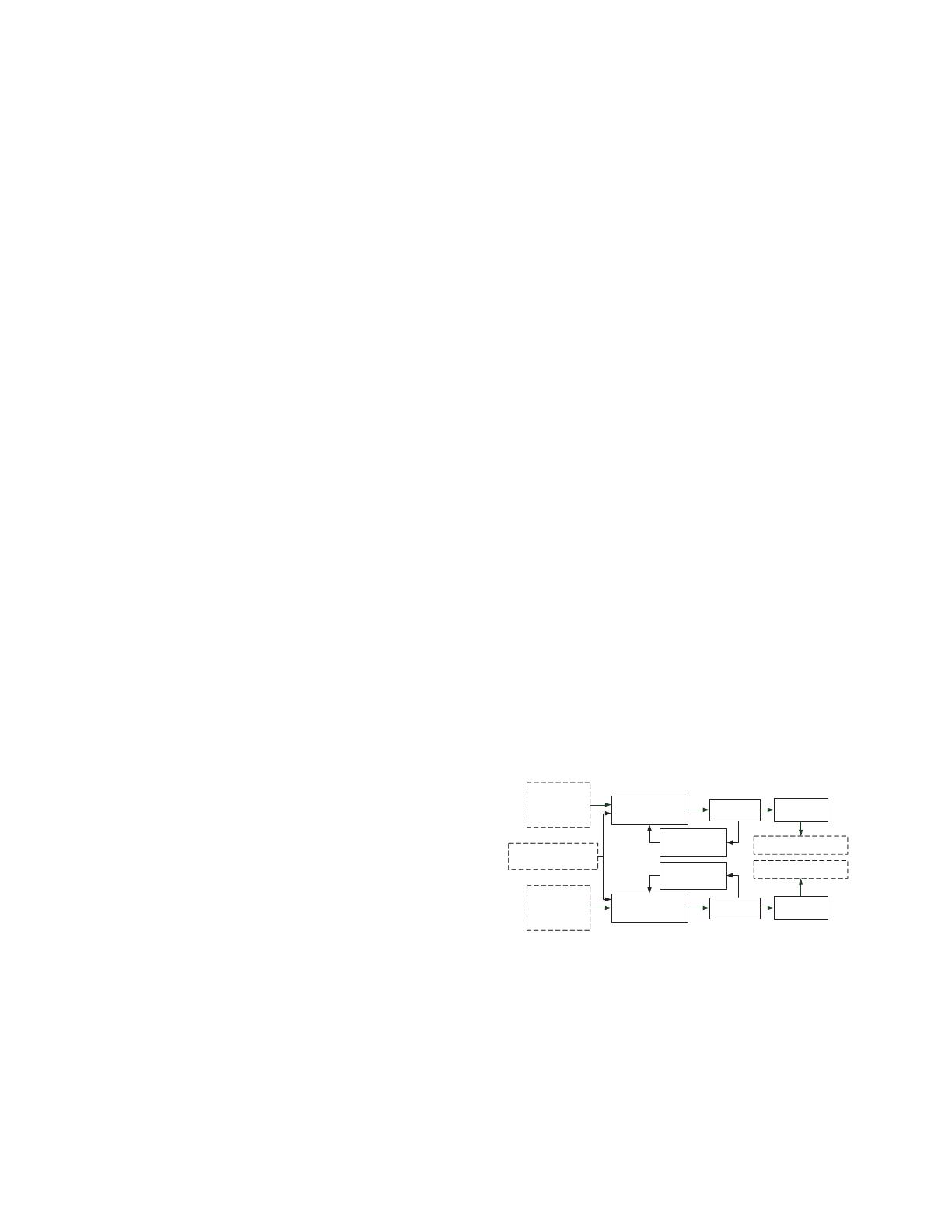
Research on SVM-Based Direct Torque Control for PMSM of Artillery Speed
Servo System
CHEN Teng-fei, HAN Chong-wei, XIE Yi-na,ZHAO Yu-he
Northwest Institute of Mechanical and Electrical Engineering
Abstract: The performance of direct torque control (DTC) based on space vector modulation (SVM) for permanent
magnet synchronous motor (PMSM) of artillery speed servo system is researched in this paper. The PMSM of artillery
speed servo system has small stator inductance and permanent magnet flux linkage, so high sampling interval is needed
to reduce torque ripples when using classical DTC scheme. A SVM-based DTC scheme is applied in artillery speed servo
system and the simulation is done. The simulation results indicate that the speed response of SVM-based DTC
(SVMDTC) is as fast as classical DTC and the motor’s torque ripples are small. By using the SVM-based DTC scheme a
better performance at low speed and a wider speed range is achieved.
Key Words: SVM-based DTC, PMSM, Artillery speed servo system
1 Introduction
Permanent magnet synchronous motors are widely applied
in modern artillery speed servo system due to their
advantages of small size, high power density and
maintenance-free. As calculations are executed in
stationary frame, DTC for PMSM uses no current
controller and only depends on stator resistance parameter,
which yields a faster torque response and less parameter
dependence than the vector control. With the features of
fast dynamic response and robustness, the DTC-based
PMSM servo system becomes a popular issue of high
performance AC motor servo system. [1][2]
The classical DTC (CDTC) scheme for PMSM proposed in
[3] uses two hysteresis comparators for stator flux linkage
and electromagnet torque respectively. The instantaneous
error values of stator flux linkage and electromagnet torque
combined with the section number containing the stator
flux vector are inputted into a switching table to choose a
proper voltage vector to control the motor. So low
sampling frequency often leads to large torque ripples. It is
the main drawback of the classical DTC scheme. [4] The
sampling frequency is limited by some physical factors
such as the microprocessor computing capability and the
efficiency of power devices in practical application. The
cost effectiveness is low when only the sampling
frequency of control system is increased. Predictive
control methods are used in [5] [6] to reduce the torque
ripples but the predictive control algorithm is complicate
and the effect at high speed is not obvious. The SVMDTC
schemes for interior and surface mounted PMSM are
proposed in [7] [8] .The torque ripples are tremendously
reduced and the system sampling frequency is not very
high. Both of the PMSM used in [7] [8] meet the
requirements described in [3] but their speed is not very
high. The DC bus voltage of the PMSM used in artillery
speed servo system is low and the motor’s stator
inductance is very small, which is different from the
PMSM in [7] [8].It is worth investigating the performance
of SVMDTC for this kind of PMSM.
In this paper, the structure and features of the artillery
speed servo system are introduced firstly. Then the model
of the SVMDTC for PMSM of artillery servo system is
built and analyzed. Finally, the simulation of the
SVMDTC for PMSM and comparative analysis with
CDTC is done.
2 Structure and Features of the Artillery Speed
Servo System
The structure of the artillery speed servo system is
illustrated in Fig.1 constituting of azimuth speed servo
system and elevation speed servo system, and its main
parts include such as AC drive box, PMSM and gearbox.
Artillery speed servo system receives speed commends
given by semi-automatic console or position controller,
completes azimuth or pitching adjustment. And there is a
rotary transformer installed on the motor shaft to provide
the mechanical angle information of the rotor.
Azimuth AC
Drive Box PMSM
Azimuth
Position
Controller
Azimuth Turret
Semi-automatic
Console
Rotary
Transformer
Gear Box
Elevation
AC Drive Box PMSM
Elevation
Position
Controller
Elevation Turret
Rotary
Transformer
Gear Box
Fig. 1: Structure of the Artillery Speed Servo System
Due to the limitations of vehicle’s power supply and the
gearbox’s transmission ratio, the low DC-bus voltage and
high-speed PMSM is used. The permanent magnet flux
linkage and stator inductance of the PMSM are very small,
while amplitude of phase current is very large. When using
the CDTC scheme, a very high sampling frequency should
be applied to achieve low torque ripples and stabilized low
speed performance. But high sampling frequency will lead
to low efficiency of power device and of which the
3727
978-1-4673-5534-6/13/$31.00 c
2013 IEEE
Authorized licensed use limited to: Anelis Plus consortium. Downloaded on October 09,2022 at 15:40:29 UTC from IEEE Xplore. Restrictions apply.