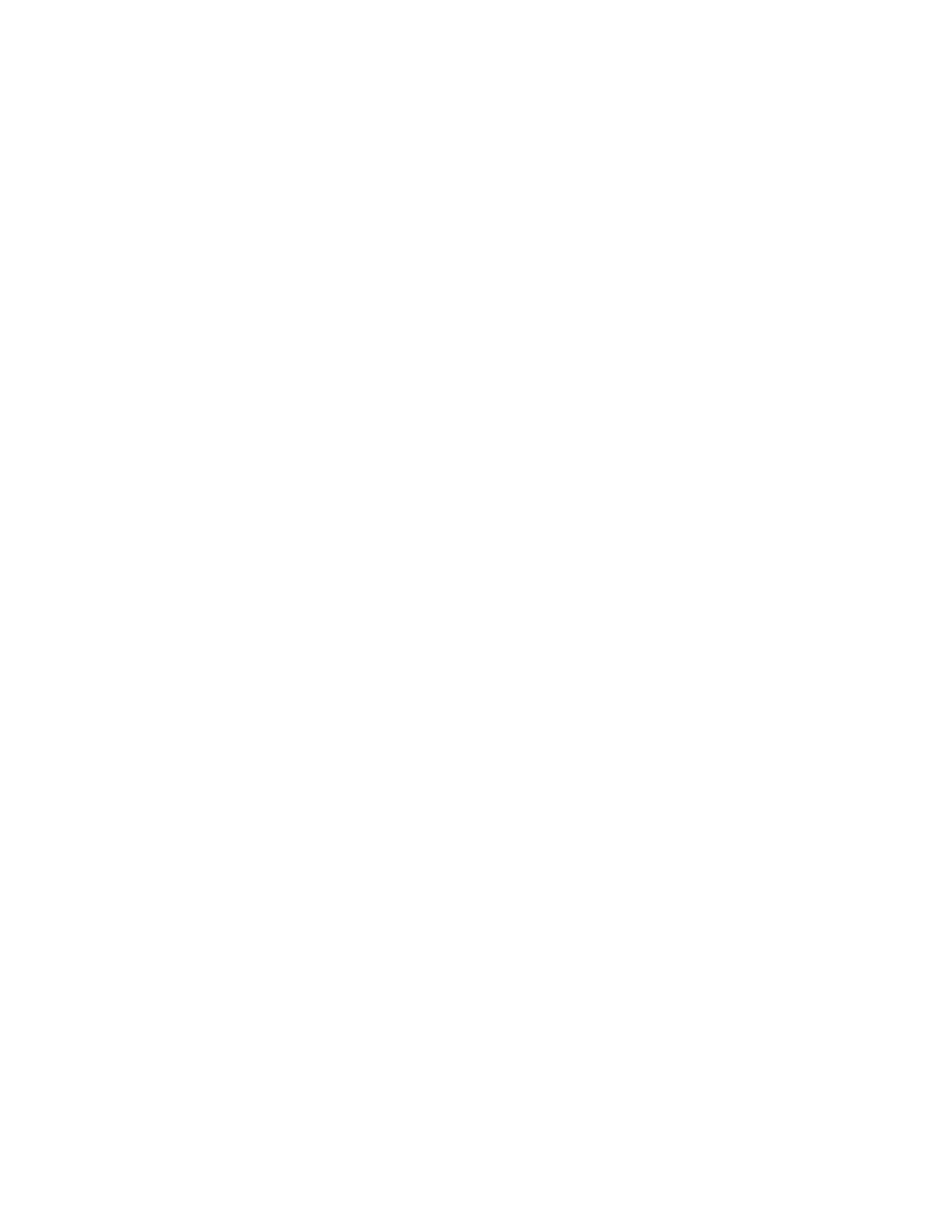
are flowing through the system. Because gas bubbles are compress-
ible, highly reflective, and electrically nonconductive, they severely
distort the signal in the detector; therefore, many systems remove
the bubbles before the optical light path. However, if the system
removes the bubbles at any point within the system, the segregated
liquids will be able to interact and pool. This interaction can cause
cross-contamination or loss of wash, and decreases the rate at which
samples can be processed. Real-time analog or digital data recon-
struction techniques known as curve regeneration can remove the
effect of pooling at the flow-cell debubbler and/or any other unseg-
mented zones of the system. “Bubble-gating” is a technique that
does not remove the bubbles, but instead uses analog or digital
processing to remove the distortion caused by the bubbles. Bubble-
gating requires a sufficiently fast detector response time and re-
quires that the volume of the measurement cell be smaller than the
volume of the individual liquid segment.
b. Sample dispersion and interferences: Theoretically, the output
of the detector is square-wave. Several carryover processes can
deform the output exponentially. The first process, longitudinal
dispersion, occurs as a result of laminar flow. Segmentation of the
flow with air bubbles minimizes the dispersion and mixing between
segments. The second process is axial or lag-phase dispersion. It
arises from stagnant liquid film that wets the inner surfaces of the
transmission tubing. Segmented streams depend on wet surfaces for
hydraulic stability. The back-pressure within non-wet tubing in-
creases in direct proportion to the number of bubbles it contains and
causes surging and bubble breakup. Corrective measures include
adding specific wetting agents (surfactants) to reagents and mini-
mizing the length of transmission tubing.
Loose or leaking connections are another cause of carryover and
can cause poor reproducibility. Wrap TFE tape around leaking
screw fittings. When necessary, slightly flange the ends of types of
tubing that require it for a tight connection. For other connections,
sleeve one size of tubing over another size. Use a noninterfering
lubricant for other tubing connections. Blockages in the tubing can
cause back-pressure and leaks. Clean out or replace any blocked
tubing or connection. A good indicator for problems is the bubble
pattern; visually inspect the system for any abnormal bubble pattern
that may indicate problems with flow.
For each analysis, check individual method for compounds
that can interfere with color development and/or color reading.
Other possible interferences include turbidity, color, and salinity.
Turbid and/or colored samples may require filtration. In another
interference-elimination technique, known as matrix correction,
the solution is measured at two separate wavelengths, and the
result at the interference wavelength is subtracted from that at
the analytical wavelength.
2.
Apparatus
a. Tubing and connections: Use mini- or micro-bore tubing
on analytical cartridges. Replace flexible tubing that becomes
discolored, develops a “sticky” texture, or loses ability to spring
back into shape immediately after compression. Also see man-
ufacturer’s manual and specific methods.
b. Electrical equipment and connections: Make electrical
connections with screw terminals or plug-and-socket connec-
tions. Use shielded electrical cables. Use conditioned power or a
universal power supply if electrical current is subject to fluctu-
ations. See manufacturer’s manual for additional information.
c. Automated analytical equipment: Dedicate a chemistry
manifold and tubing to each specific chemistry. See specific
methods and manufacturer’s manual for additional information.
d. Water baths: When necessary, use a thermostatically con-
trolled heating/cooling bath to decrease analysis time and/or
improve sensitivity. Several types of baths are available; the
most common are coils heated or cooled by water or oil. Tem-
perature-controlled laboratories reduce drift in temperature-
sensitive chemistries if water baths are not used.
3.
Reagents
Prepare reagents according to specific methods and manufactur-
er’s instructions. If required, filter or degas a reagent. Use reagent
water (see Section 1080) if available; if not, use a grade of water that
is free of the analyte and interfering substances. Run blanks to
demonstrate purity of the water used to prepare reagents and wash
SFA system. Minimize exposure of reagents to air, and refrigerate
if necessary. If reagents are made in large quantities, preferably
decant a volume sufficient for one analytical run into a smaller
container. If using a wetting agent, add it to the reagent just before
the start of the run. Reagents and wetting agents have a limited
shelf-life. Old reagents or wetting agents can produce poor repro-
ducibility and distorted peaks. Do not change reagent solutions or
add reagent to any reagent reservoirs during analysis. Always start
with a sufficient quantity to last through the analytical run.
4.
Procedure
For specific operating instructions, consult manufacturer’s direc-
tions and methods for analytes of interest. At startup of a system,
pump reagents and wash water through system until system has
reached equilibrium (bubble pattern smooth and consistent) and
base line is stable. Meanwhile, load samples and standards into
sample cups or tubes and type corresponding tags into computer
table. When ready, command computer to begin run. Most systems
will run the highest standard to trigger the beginning of the run,
followed by a blank to check return to base line, and then a set of
standards covering the analytical range (sampling from lowest to
highest concentration). Construct a curve plotting concentration
against absorbance or detector reading and extrapolate results
(many systems will do this automatically). Run a new curve daily
immediately before use. Calculation and interpretation of results
depend on individual chemistry and are analogous to the manual
method. Insert blanks and standards periodically to check and
correct for any drift of base line and/or sensitivity. Some systems
will run a specific standard periodically as a “drift,” and automati-
cally will adjust sample results. At end of a run, let system flush
according to manufacturer’s recommendations.
5.
Quality Control
The QC practices considered to be an integral part of each
method are summarized in Table 4020:I. Also see individual
methods for quality control methods and precision and bias data.
SEGMENTED CONTINUOUS FLOW ANALYSIS (4120)/Segmented Flow Analysis Method
2
SEGMENTED CONTINUOUS FLOW ANALYSIS (4120)/Segmented Flow Analysis Method