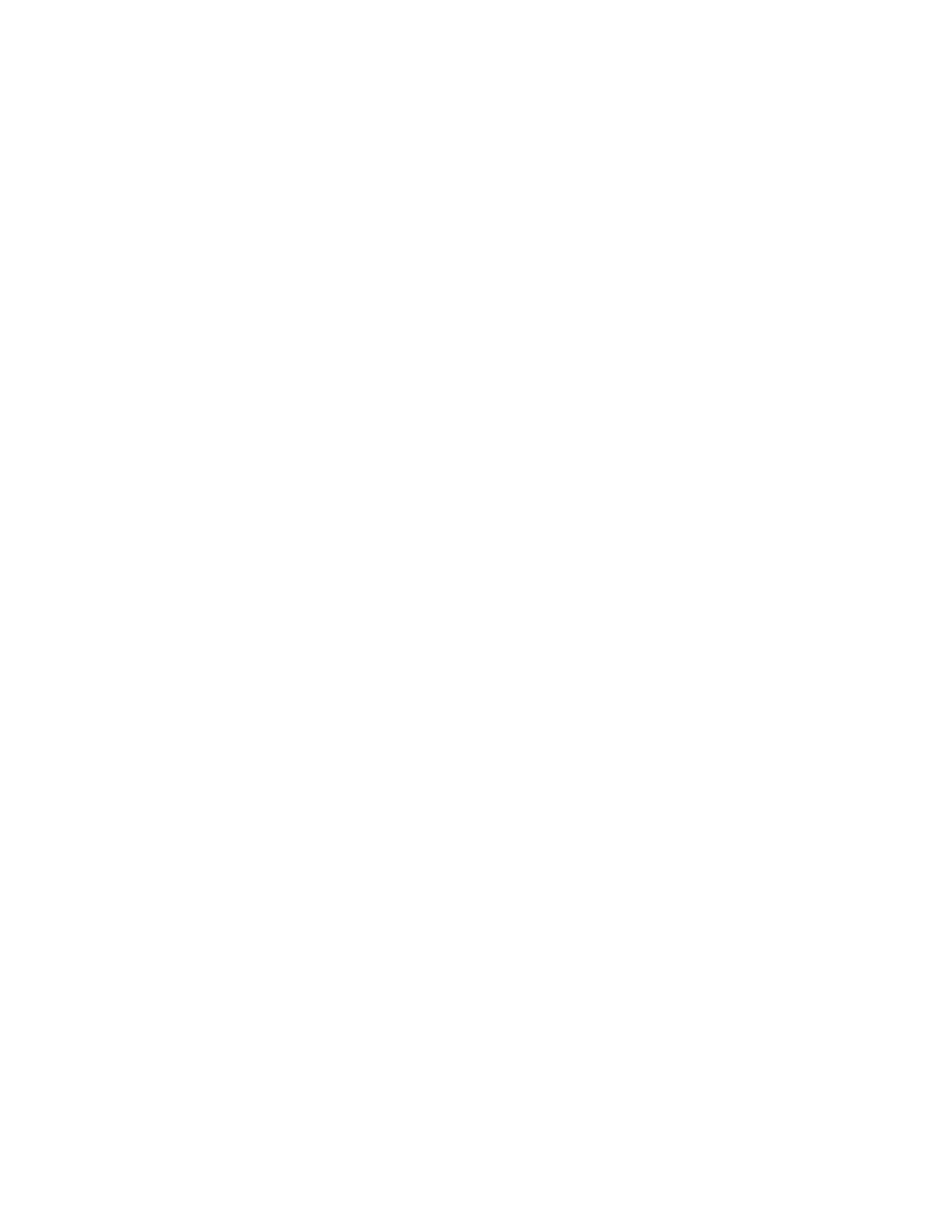
a. Access: Conduct all transfers and work with these sub-
stances in a controlled area, i.e., a restricted-access hood, glove
box, or portion of a laboratory, designated for use of highly toxic
substances, for which all people with access are aware of the
substances being used and necessary precautions.
b. Approvals: Prepare a plan for use and disposal of these
materials and obtain the approval of the laboratory supervisor.
c. Non-contamination/decontamination: Protect vacuum
pumps against contamination by scrubbers or HEPA filters and
vent them into the hood. Decontaminate vacuum pumps or other
contaminated equipment, including glassware, in the hood be-
fore removing them from the controlled area. Decontaminate the
controlled area before routine work is resumed.
d. Exiting: On leaving a controlled area, remove any protec-
tive apparel (place it in an appropriately labeled container), and
thoroughly wash hands, forearms, face, and neck.
e. Housekeeping: Use a wet mop or a vacuum cleaner
equipped with a HEPA filter. Do not dry sweep if the toxic
substance is a dry powder.
f. Medical surveillance: If using toxicologically significant
quantities of such a substance on a regular basis (e.g., three times
per week), consult a qualified physician about desirability of
regular medical surveillance.
g. Records: Keep accurate records of the amounts of these
substances stored and used, the dates of use, and names of users.
h. Signs and labels: Ensure that the controlled area is con-
spicuously marked with warning and restricted access signs and
that all containers of these substances are appropriately labeled
with identity and warning labels.
i. Spills: Ensure that contingency plans, equipment, and ma-
terials to minimize exposures of people and property are avail-
able in case of accident.
j. Storage: Store containers of these chemicals only in a
ventilated, limited-access area.
k. Glove boxes: For a negative-pressure glove box, ensure that
the ventilation rate is at least 2 volume changes/h and the
pressure drop at least 1.3 cm of water. For a positive-pressure
glove box, thoroughly check for leaks before each use. In either
case, trap the exit gases or filter them through a HEPA filter and
then release them into the hood.
l. Waste: Ensure that containers of contaminated waste (in-
cluding washings from contaminated flasks) are transferred from
the controlled area in a secondary container under the supervi-
sion of authorized personnel.
8.
Physical Hazards
a. Electrical: Ensure that electrical wiring, connections, and ap-
paratus conform to the requirement of the latest National Electrical
Code. Fire, explosion, power outages, and electrical shocks are all
serious hazards that may result from incorrect use of electrical
devices. Ground all electrical equipment or use double-insulated
equipment. Use ground fault interrupter circuit breakers to the
maximum extent possible. Do not locate electrical receptacles in-
side fume hoods, and do not use equipment near volatile flammable
solvents. Use approved safety refrigerators. Disconnect electrical
equipment from the power supply before service or repair is at-
tempted and never bypass safety interlocks. Attempting to repair
equipment using employees not thoroughly acquainted with elec-
trical principles may present particularly dangerous situations.
b. Non-ionizing radiation: Non-ionizing radiation, also called
electromagnetic radiation, is generally considered to be the radio
frequency region of the radiation spectrum. For the purposes of
dealing with personal exposures in laboratories, it also includes
the microwave frequency region. Typical laboratory exposures
to non-ionizing radiation usually include ultraviolet, visible,
infrared, and microwave radiation.
For normal environmental conditions and for incident electro-
magnetic energy of frequencies from 10 MHz to 100 GHz, the
radiation protection guide is 10 mW/cm
2
. The radiation protec-
tion applies whether the radiation is continuous or intermittent.
This means a power density of 10 mW/cm
2
for periods of 0.1 h
or more, or an energy density of 1 mW-h/cm
2
during any 0.1-h
period. These recommendations apply to both whole-body irra-
diation and partial body irradiation.
Ultraviolet radiation (UV) and lasers are used frequently. With
properly constructed and operated instruments, it is not a signif-
icant hazard but can be harmful when used for controlling
microorganisms in laboratory rooms or for sterilizing objects.
When using devices that generate or use non-ionizing radia-
tion, observe the following precautions: Wear safety glasses or
goggles with solid side pieces whenever there is a possibility of
exposure to harmful (UV) radiation. Provide proper shielding
(shiny metal surfaces reflect this energy). Shut off all these
devices (UV lamps) when not in use. Post warning signs and
install indicator lights to serve as a constant reminder when these
types of devices are in use (UV lamps).
c. Mechanical: Shield or guard drive belts, pulleys, chain drivers,
rotating shafts, and other types of mechanical power transmission
apparatus. Laboratory equipment requiring this guarding includes
vacuum pumps, mixers, blenders, and grinders.
Shield portable power tools. Guard equipment such as centri-
fuges, which have high-speed revolving parts, against “fly-
aways.” Securely fasten equipment that has a tendency to vibrate
(e.g., centrifuges and air compressors) to prevent the tendency to
“walk” and locate them away from bottles and other items that
may fall from shelves or benches because of the vibration.
d. Compressed gases: Gas cylinders may explode or “rocket” if
improperly handled. Leaking cylinders may present an explosion
hazard if the contents are flammable; they are an obvious health
hazard if the contents are toxic; and they may lead to death by
suffocation if the contents are inert gases. The Compressed Gas
Association has published procedures governing use and storage of
compressed gases. Transfer gas cylinders only with carts, hand
trucks, or dollies. Secure gas cylinders properly during storage,
transport, and use, and leave valve safety covers on cylinders during
storage and transport. Avoid the use of adapters or couplers with
compressed gas. Properly identify cylinder contents.
9.
Chemical Hazards
a. General precautions: Chemical injuries may be external or
internal. External injuries may result from skin exposure to caustic
or corrosive substances such as acids, bases, or reactive salts. Take
care to prevent accidents, such as splashes and container spills.
Internal injuries may result from the toxic or corrosive effects of
substances absorbed by the body. These internal injuries may result
from inhalation, skin contact, or ingestion.
Tables 1090:I, II, and III list PELs, TLVs, and/or short-term
exposure limits and ceilings for some chemical materials specified
LABORATORY OCCUPATIONAL HEALTH AND SAFETY (1090)/Safe Laboratory Practices
4
LABORATORY OCCUPATIONAL HEALTH AND SAFETY (1090)/Safe Laboratory Practices