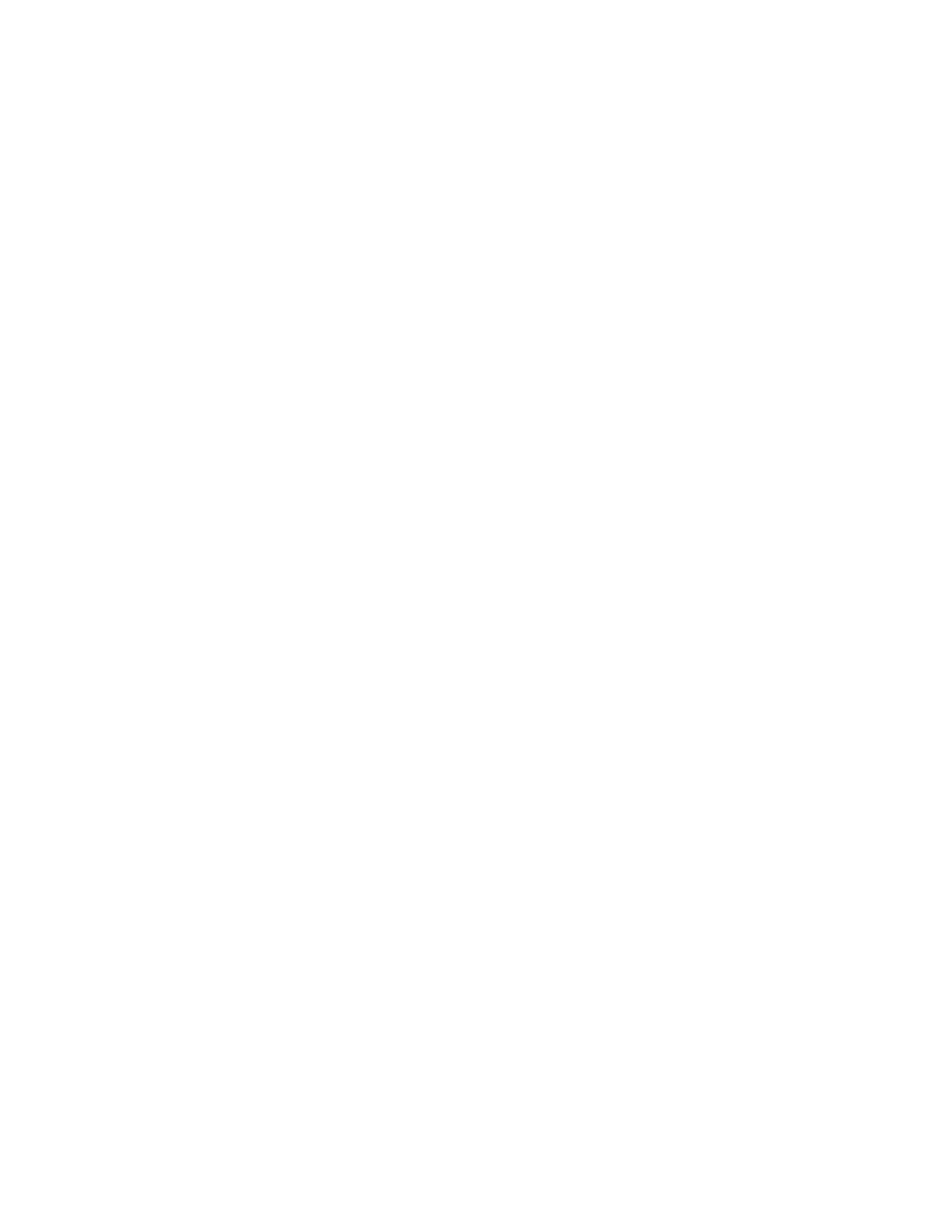
cases, makes flocculation less likely. Make dilutions only imme-
diately before measurement.
Samples measured at different temperature or pressure than when
collected and those with biological activity may develop entrained
air bubbles that interfere with measurement accuracy. If any gas
bubbles are visible, let sample stand for a short time to degas
naturally or use a mild vacuum to speed degassing. Use ultrasound
to aid degassing, but only if floc breakup is not a problem.
Minimize time between sampling and analysis; if at all pos-
sible, make measurements immediately after sampling. If storage
is unavoidable, refrigerate at 4°C but restore samples to room
temperature, preferably in water bath, before measurement.
b. Continuous-flow: Using a particle counter as a continuous-
flow monitor may be desirable. Many more samples can be
processed by automated particle counting than by batch sample
analysis. All the instruments mentioned in 2560B–D can be used
in this mode, although instruments and samples not requiring
dilution are easier to set up. For some instruments, this type of
operation requires custom hardware; for others, there is com-
mercially available hardware.
Batch sample problems are equally relevant to continuous
analysis. Other critical considerations include selection of sam-
pling point, velocity at entrance and throughout sample line,
maintenance of stable sample flow rate, position of instrument’s
sensor in the sample line, and absence of flow-modifying devices
upstream of sensor.
Choose a sampling point that is representative and away from
wall surfaces. Place entrance to sample line facing the flow, with the
velocity at the opening nearly the same as the surrounding flow.
Sample preservation within the instrument is difficult because
both deposition (or temporary holdup) of particles and floc breakup
must be avoided. Deposition occurs by gravity settling of particles
onto horizontal surfaces. Floc breakup occurs because of excessive
shear forces. Minimize length of transmission lines, especially in
horizontal components, and preferably have no horizontal lines.
Avoid drastic changes in flow direction or velocity. Do not use
flow-modifying devices (pumps, fittings with irregular surfaces,
sharp angle changes, flow controllers, etc.) between the sampling
point and the sensor. Locate pumps after the sensor. Preferably,
provide curved sample lines (e.g., flexible tubing or bent glass
tubing) rather than right-angle fittings.
For most instruments, flow rate is specified. Because calibration
(see 2560A.5) can change with flow rate within the range, flow
control within very narrow limits is essential. Calibrate and use the
sensor at the same flow rate. For continuous particle size distribu-
tion measurements, flow control (not simply flow monitoring) is
necessary. Do not make measurements at a flow rate different from
that used for calibration. Provide a flow control system downstream
of the sensor, maintain a constant rate, and do not introduce turbu-
lence or pulsations before or through the sensor.
4.
Dilution Water
Particle-free water is virtually impossible to obtain, but it is
possible to produce water containing very few particles within
the size range to be measured. Produce “particle-free” or “clean”
water from distilled, deionized water or water taken from the
same source as the samples. If all samples are from the same
source or have similar chemical characteristics, preferably filter
sample water to produce “particle-free” water with no change in
chemical environment. Distilled, deionized water produced by
ion exchange and cartridge filtration may produce acceptable
“particle free” dilution water, but preferably use continuous
closed-loop membrane filtration.
Dilution water preparation systems are available from particle-
counter manufacturers. Alternatively, assemble a system similar
to that shown in Figure 2560:1 (or any system that produces a
water of sufficient quality). In the system shown, a pump draws
the water from a bottle and puts it through the in-line filter. Use
membrane filters with nominal pore sizes no more than 10% of
the smallest particle size expected; alternatively use cartridge
filters. Pass water through the filter several times. The system
lets water be passed directly from the product-water bottle to the
source-water bottle by opening the clamps and three-way stop-
cock. Use glass tubing in the bottles, but use flexible tubing to
allow product-water bottle to drain into source-water bottle.
Attach a glass wool or membrane filter to air inlets. Dilute
samples by drawing water directly from the three-way stopcock
into the bottle to be used in sample analysis.
A simpler system with one-pass filtration directly into the
sample bottle may be adequate for many samples, depending on
the particle size range to be measured. Such a system would omit
the product-water bottle, the connections between the two bottles
and associated stopcock and clamps of Figure 2560:1. Dilution
water is produced on demand and the effluent is put directly,
without additional handling, into the sample container.
Guard against biological growth within filtration systems by
frequent disassembly and adequate washing or replacement of
components. For many samples, do not use chemical disinfec-
tants because they might change the particle count and size
distribution by their oxidizing potential.
5.
Calibration
When an instrument’s sensing zone detects a particle; an
electrical response is generated and sorted into a channel of the
instrument based on its magnitude.
Calibrate by determining the channel number into which the
instrument sorts particles of known size. Use spherical particles
manufactured for this purpose. Calibration particles are available
in suspension or as dry particles. Over time, suspensions are
likely to undergo some aggregation; use ultrasound to break up
flocs before calibration. Calibration particles are nearly mono-
disperse but do exhibit a small inherent (true) variance.
The instrument’s precision (Section 1030A.1) and resolution
influence its ability to sort particles into different channels.
Resolution is a measure of an instrument’s ability to distinguish
between particles of similar but different sizes. An instrument
with high precision and good resolution will measure monodis-
perse particles in a very narrow size range; some instruments
have sufficient precision and resolution so calibration particles
with extremely narrow size distributions (very small variance)
are sorted into a few adjacent channels. In such cases, the true
variance of the particle size and the measured variance will be
nearly equal. An instrument with low precision but high resolu-
tion will yield a wide distribution on the same particles (i.e.,
measured variance ⬎true variance). An instrument with high
precision but low resolution (e.g., few channels) may yield a
narrow measured distribution (e.g., all the particles in the same
PARTICLE COUNTING & SIZE DISTRIBUTION (2560)/Introduction
2
PARTICLE COUNTING & SIZE DISTRIBUTION (2560)/Introduction