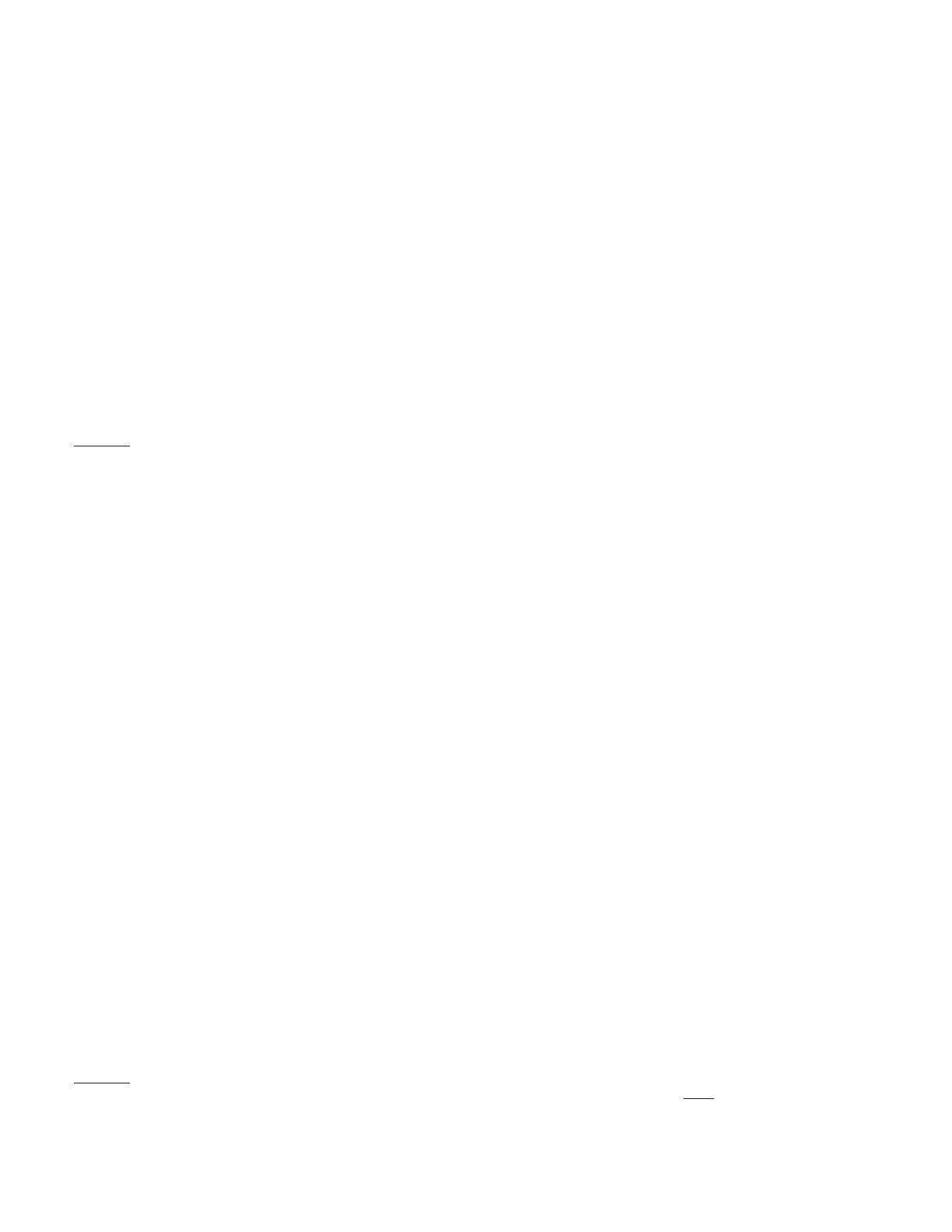
2810 DISSOLVED GAS SUPERSATURATION*
2810 A. Introduction
Water can become supersaturated with atmospheric gases by
various means, heating and air entrainment in spilled or pumped
water being the most common. The primary sign of gas super-
saturation is the formation of bubbles on submerged surfaces or
within the vascular systems and tissues of aquatic organisms.
Gas supersaturation can limit aquatic life and interfere with
water treatment processes. Levels of supersaturation lethal to
aquatic organisms have been found in springs, rivers, wells,
lakes, estuaries, and seawater. Gas supersaturation can be pro-
duced in pumped or processed water intended for drinking, fish
hatchery supply, and laboratory bioassays. Seasonal and other
temporal variations in supersaturation may occur in surface
waters as a result of solar heating and photosynthesis. Because
the rate of equilibration may be slow, supersaturation may persist
in flowing water for days and excessive dissolved gas levels thus
may persist far from the source of supersaturation.
Gas bubbles form only when the total dissolved gas pressure
is greater than the sum of compensating pressures. Compensat-
ing pressures include water, barometric and, for organisms,
tissue or blood pressure. The total dissolved gas pressure is equal
to the sum of the partial pressures of all the dissolved gases,
including water vapor. Typically, only nitrogen, oxygen, argon,
carbon dioxide, and water vapor pressures need to be considered
in most natural waters. Gas bubble disease, of fish or other
aquatic organisms, is a result of excessive uncompensated gas
pressure. A single supersaturated gas such as oxygen or nitrogen
may not necessarily result in gas bubble disease because bubble
formation depends largely on total dissolved gas pressure. The
degree of gas saturation should be described in terms of pres-
sures rather than concentration or volume units.
2810 B. Direct-Sensing Membrane-Diffusion Method
1.
General Discussion
a. Principle: This method requires an instrument with a variable
length of “gas permeable” tubing, connected to a pressure-measur-
ing device. Dimethyl silicone rubber tubing often is used because it
is highly permeable to dissolved gases, including water vapor. At
steady state, the gauge pressure inside the tubing is equal to the
difference in gas pressure (⌬P) between the total dissolved gas
pressure and the ambient barometric pressure. When the water is in
equilibrium with the atmosphere, ⌬Pequals zero. If ⌬Pis greater
than zero, the water is supersaturated. Conversely, if ⌬Pis negative
the water is undersaturated.
b. Working range: The working range of this method depends
on the pressure-sensing device used, but typically will range
from ⫺150 to ⫹600 mm Hg. Dissolved solids in wastewater will
not interfere with this method. The practical depth range for
these instruments is 1 to 10 m.
2.
Apparatus
Several types of membrane-diffusion instruments are available
commercially.* Alternatively, construct a unit from commer-
cially available parts. Several units have been described, includ-
ing a direct-reading instrument using pressure transducers and a
digital readout,
1
an on-line unit that can activate an alarm sys-
tem,
2
and an early model of the Weiss saturometer.
3
Each of
these units has specific advantages and limitations; the instru-
ment of choice will depend on the specific application. All these
instruments are portable so that data collection is completed in
the field.
Test the instrument for leaks according to the manufacturer’s
recommendation. Even a very small leak, difficult to detect and
locate, will result in useless data. Calibrate the pressure-measuring
device with a mercury manometer or certified pressure gauge. If a
manometer is used, include fresh mercury that flows freely in the
tubing. An alternative method for directly testing membrane-diffu-
sion instruments in a small, closed chamber where induced ⌬P
levels can be compared against observed ⌬Plevels is available.
2
Van Slyke-Neill
4
or gas chromatography methods
1
are inap-
propriate for calibration but they may be used to verify results.
These methods measure individual gas concentrations and re-
quire further conversion to ⌬Por partial pressure and suffer from
sampling and sample handling problems.
5–7
3.
Procedure
At the start of each day, test the instrument for leaks and recali-
brate. At a monitoring site, completely submerge the sensing ele-
ment in the water, preferably below the hydrostatic compensation
depth. This is the depth where the hydrostatic and total gas pressures
are equal and as a result, bubbles will not form on the tubing.
Bubble formation on the silicone rubber tubing seriously reduces
accuracy. Compute hydrostatic compensation depth
5
as follows:
Z⫽⌬P
73.42
* Approved by Standard Methods Committee, 2010. Editorial revisions, 2011.
Joint Task Group: 20th Edition—John E. Colt (chair), Larry E. Fidler, John O.
Jensen, John W. Sweeney, Barnaby J. Watten.
* Common Sensing, Clark Fork, ID; Eco Enterprises, Seattle, WA; Novatech,
Vancouver, BC, Canada; and Sweeney Aquametrics, Stony Creek, CT.
1