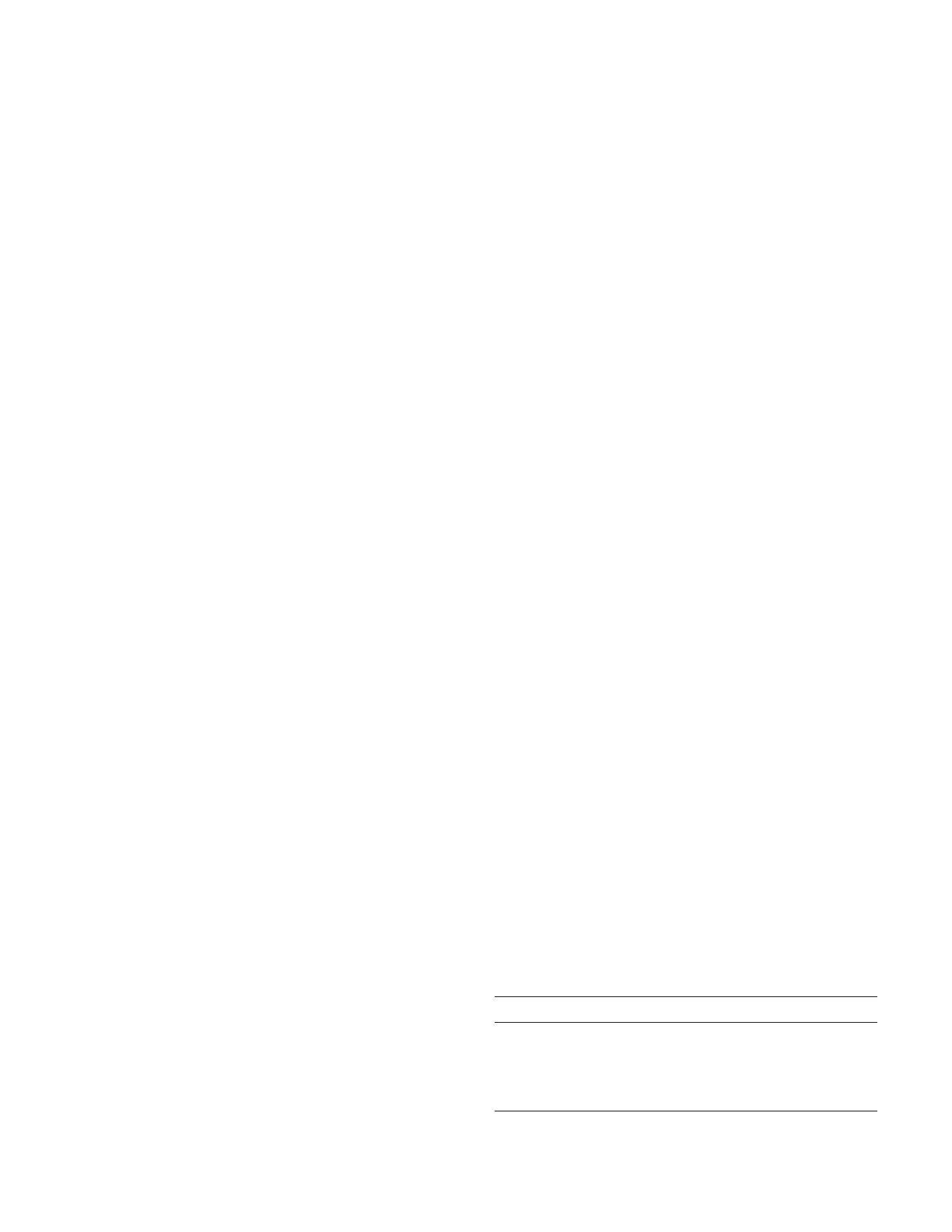
Impurities may be added to the water during boiling if they
leach from the container. Also, freshly replaced filters, car-
tridges, and resins initially can release impurities. Pretreat feed-
water and maintain still periodically to minimize scale forma-
tion. Pretreatment may be required if the feedwater contains
significant concentrations of calcium, magnesium, and bicarbon-
ate ions; it may involve demineralization via reverse osmosis or
ion exchange.
2.
Reverse Osmosis
In reverse osmosis, water is forced under pressure through a
semipermeable membrane, thereby removing some dissolved
constituents and suspended impurities. The reagent water quality
will depend on both feedwater quality and the type and condition
of membranes used.
Reverse osmosis membranes are available in both spiral-
wound and hollow-fiber configurations; the choice depends on
the feedwater’s characteristics and fouling potential. Obtain re-
jection data for feedwater contaminants (levels of salt and im-
purities that will pass through the membranes compared to
feedwater levels) at the operating pressure that will be used to
prepare reagent water. Set the water-production rate to make the
most economical use of feedwater without compromising per-
meate (reagent water) quality.
Pretreatment steps (e.g., filtration) may be needed to minimize
membrane fouling (due to colloids or particulates) and/or deg-
radation (due to chlorine, iron, and other oxidizing compounds).
Also, the membrane modules need to be backwashed periodi-
cally to clean the surface of the membranes. If using a commer-
cially available reverse osmosis system, follow manufacturer’s
instructions for quality control (QC) and maintenance.
3.
Ion Exchange
In an ion exchange process, water passes through a reactor
containing negatively charged (anionic) and/or positively
charged (cationic) resins. Targeted ions in the water are substi-
tuted with specific ions on the resins (ones acceptable in treated
water systems), thereby purifying the water. To prepare deion-
ized water, direct feedwater through a mixed-bed ion exchanger,
which contains both strong anion and strong cation resins. Proper
bed sizing is critical to resin performance. Be sure the bed’s
length-to-diameter ratio is in accordance with the maximum
process flow rate to ensure that optimal face velocities are not
exceeded and that residence time is sufficient.
If the system does not generate reagent water continuously,
recirculate the water through the ion exchanger. If resin regen-
eration is economically attractive, use separate anion and cation
resin beds, and position the anion exchanger downstream of the
cation exchanger to remove leachates from the cation resin. If the
feedwater contains significant quantities of organic matter, re-
move the organics first to minimize the potential for resin foul-
ing. Organics can be removed via prefiltration, distillation, re-
verse osmosis, or adsorption. If using commercially prepared
resin columns, follow supplier’s recommendations for monitor-
ing QC of reagent water from specific equipment.
4.
Adsorption
In adsorption, water is fed into a reactor filled with an
adsorbent material (typically, granular activated carbon, al-
though some resins and other manmade adsorbents are used in
specific applications). Chlorine and other organic impurities
are drawn from the water to the surface of the adsorbent. How
well the process works depends on the organic contaminants
involved, the activated carbon’s physical characteristics, and
the operating conditions. In general, organics-adsorption ef-
ficiency is inversely proportional to the solubility of the
organics in water and the adsorption process may be inade-
quate for removing low-molecular-weight, polar compounds.
Performance differences among activated carbons are attrib-
utable to the raw materials and activation procedures. Even
with an optimal activated carbon, proper performance will not
be attained unless the column is sized to provide required face
velocity and residence time at the maximum process flow rate.
If using commercial sorbent systems, follow supplier’s rec-
ommended flow and QC steps.
Using activated carbon may adversely affect the reagent wa-
ter’s resistivity. This effect may be controlled via reverse osmo-
sis, mixed resins, or special adsorbents. To minimize organic
contamination, use mixtures of polishing resins with special
carbons and additional treatment steps (e.g., reverse osmosis,
natural carbons, ultraviolet oxidation, or ultrafiltration).
1080 C. Reagent Water Quality
1.
Quality Guidelines
Guidelines for reagent water vary with the intended use.
1
Table 1080:II lists some characteristics of various qualities of
reagent water. In general, low-quality reagent water has a min-
imum resistivity of 0.1 megohm-cm at 25°C. It may be used to
wash glassware, rinse glassware (as a preliminary step), and as a
source to produce higher-grade waters.
Medium-quality reagent water typically is produced via distilla-
tion or deionization. Resistivity should be ⬎1 megohm-cm at 25°C.
High-quality reagent water has a minimum resistivity of 10
megohms-cm at 25°C. It typically is prepared via distillation,
deionization, or reverse osmosis of feedwater followed by
mixed-bed deionization and membrane filtration (0.2-
m pore).
TABLE 1080:II. REAGENT WATER SPECIFICATIONS
Quality Parameter High Medium Low
Resistivity, megohm-cm
at 25°C
⬎10 ⬎1⬎0.1
Conductivity,
mho/cm
at 25°C
⬍0.1 ⬍1⬍10
SiO
2
, mg/L ⬍0.05 ⬍0.1 ⬍1
REAGENT WATER (1080)/Reagent Water Quality
2
REAGENT WATER (1080)/Reagent Water Quality