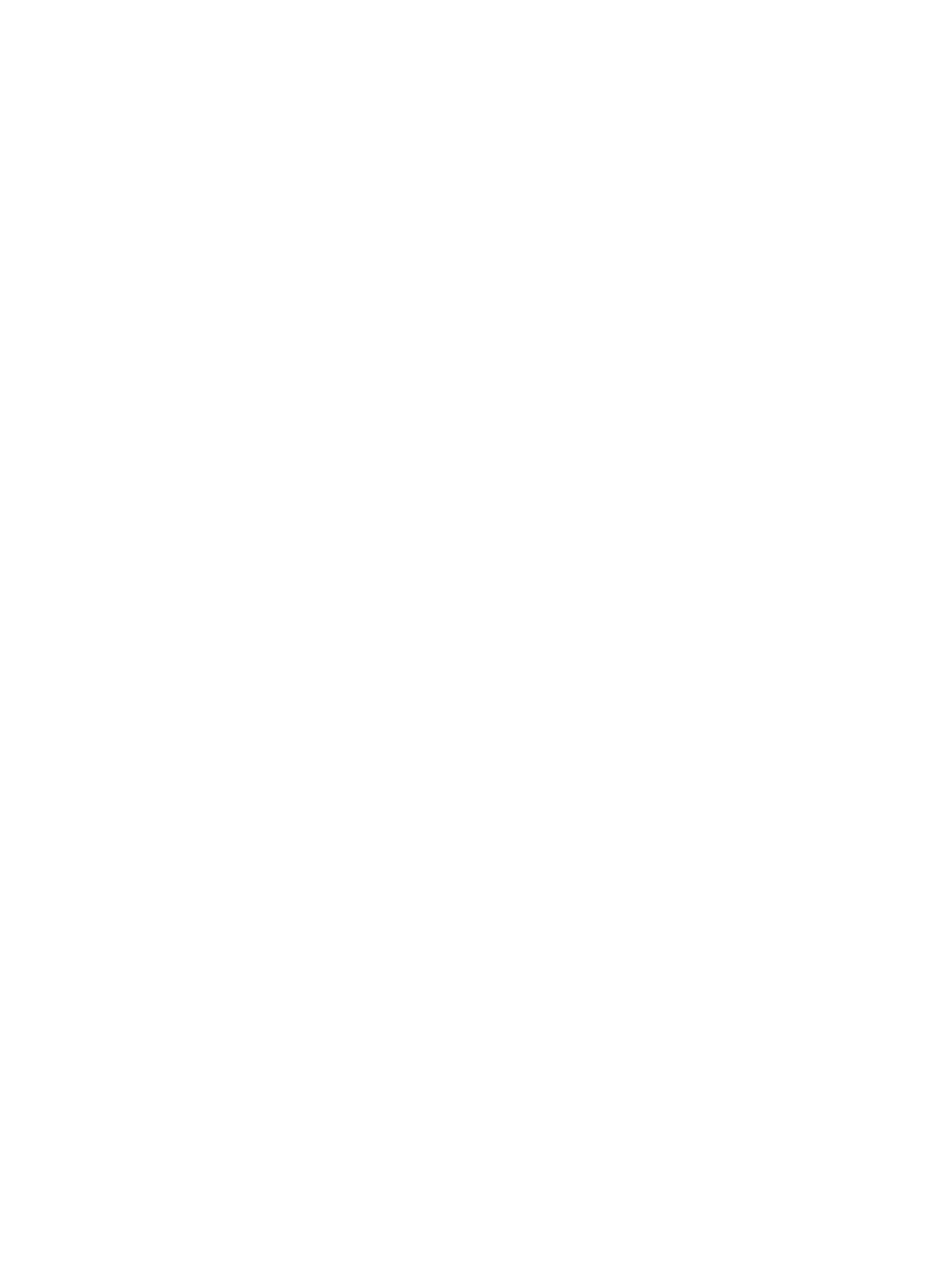
in turns. Then, they were immersed in the sol for about 1 min
and pulled up vertically at a speed of 1 mm/s. After the samples
were dried at room temperature for 24 h, they were subsequently
heated at 100 °C for 1 h. The crystallization of the films occurred
by heat treatment at 450 °C for 60 min. Elsewhere, we showed
that this procedure is suitable for production of anatase TiO2
thin films.54 The thickness of the films was measured at about
200 nm by a profilometer.
Preparation of Graphene Oxide Nanosheets. The modified
Hummers method29,55 was utilized to oxidize natural graphite
powders (45 µm, Sigma-Aldrich) for the synthesis of graphite
oxide. In a typical procedure, 50 mL of H2SO4was added to a
500 mL flask containing2gofgraphite at room temperature.
The flask was cooled to 0 °C in an ice bath. Then6gof
potassium permanganate (KMnO4) was added slowly to the
above mixture, which was allowed to warm to room tempera-
ture. The suspension was stirred continuously for2hat35°C.
After that, it was cooled in an ice bath and subsequently diluted
by 350 mL of DI water. Then H2O2(30%) was added in order
to reduce residual permanganate to soluble manganese ions, i.e.,
until the gas evolution ceased. Finally, the resulting suspension
was filtered, washed with water, and dried at 60 °C for 24 h to
obtain graphite oxide.
By rapidly heating the as-prepared graphite oxide in a tube
furnace, it was thermally exfoliated. After the tube furnace was
heated to 1050 °C, an alumina boat loaded with the graphite
oxide was quickly moved into the heating zone of the furnace,
kept there for 30 s, then rapidly removed.
Deposition of Graphene Oxide on TiO2.Thin films contain-
ing graphene oxide platelets were prepared by spreading an
aqueous suspension of the prepared graphene oxide nanosheets
onto the TiO2thin film. Then the deposited samples were dried
at 60 °C in air for 24 h (as-deposited graphene oxide/TiO2thin
films). For better adhesion of the graphene oxide platelets to
the TiO2layer, the dried thin films were postannealed at
400 °C in air for 30 min (annealed graphene oxide/TiO2thin
films). Before the graphene oxide deposition, the TiO2thin films
were carefully cleaned by DI water and methanol and2hof
UV-visible irradiation of a mercury lamp.
Photocatalytic Reduction of Graphene Oxide on TiO2.For
the photocatalytic reduction of the graphene oxide nanosheets
deposited on the TiO2, at first, the thin films were immersed in
ethanol solution. Then they were irradiated by a 110 mW/cm2
mercury lamp (peak wavelengths at 275, 350, and 660 nm) for
different periods of time at room temperature.
Material Characterization. Surface topography of the thin
films was studied by atomic force microscopy (AFM) obtained
by using a Park Scientific model CP-Research (VEECO) with
a contact force setting of 1 nN. XPS was employed to study
the chemical states of the prepared samples. The data were
obtained by using a hemispherical analyzer with an Al KRX-ray
source (hν)1486.6 eV) operating at a vacuum better than 10-7
Pa. SDP Ver. 4.0 software was utilized to analyze and
deconvolute the XPS peaks. Peak deconvolutions were per-
formed with Gaussian components after a Shirley background
subtraction.
Antibacterial Test. The antibacterial activity of the TiO2and
the graphene (oxide)/TiO2thin films against the Escherichia
coli (E. coli, ATCC 25922) bacteria was studied with use of
the so-called antibacterial drop-test. Before the microbiological
experiment, all glass ware and samples were sterilized by
autoclaving at 120 °C for 15 min. The microorganisms were
cultured on a nutrient agar plate at 37 °C for 24 h. The cultured
bacteria were added in 10 mL of saline solution to reach the
concentration of bacteria of ∼108colony forming units per
milliliter (CFU/mL) corresponding to the MacFarland scale. A
portion of the saline solution containing the bacteria was diluted
to ∼106CFU/mL by DI water. For the antibacterial drop-test,
each thin film was placed into a sterilized Petri dish. Then 100
µL of the diluted saline solution containing E. coli was spread
on the surface of the thin film. After exposing the thin films to
solar light irradiation (during the months of May-September
in Tehran (IRAN) at around noon), the bacteria were washed
from the surface of the thin film with 5 mL of phosphate buffer
solution in the sterilized Petri dish. Then 10 µL of each bacteria
suspension was spread on a nutrient agar plate and incubated
at 37 °C for 24 h before counting the surviving bacterial
colonies.
3. Results and Discussion
To observe and characterize the graphene (oxide) nanosheets
deposited on the TiO2thin film, AFM was utilized as an
effective technique. The AFM images of the graphene (oxide)/
TiO2thin films have been shown in Figure 1. It is seen that the
films consist of overlapping platelets. The graphene (oxide)
platelets deposited on the surface showed a relatively smooth
planar structure. The surface of the annealed TiO2thin film was
also smooth so that its root-mean-square surface roughness was
measured at 0.54 nm. The as-deposited graphene oxide thin film
exhibited in Figure 1a shows two overlapped graphene oxide
platelets and a number of particle-like features on the film
surface. These surface features can be attributed to the residual
carbon or solvent attached to defect sites of the platelets and/or
the film surface, as also observed by others (see for example
ref 56). In fact, we also observed that these particle-like features
could be removed from the surface by heat treatment of the
graphene oxide thin films at temperatures higher than 500 °C,
which can be assigned to combustion of the particles to carbon
dioxide, as similarly reported by Wang et al.57 The height profile
diagram of the AFM image showed that the height of the
graphene oxide layer was about 1.7 nm, which is larger than
∼0.8 nm as the typical thickness of the observed single-layer
graphene oxides.31 It is known that the typical thickness of
graphene oxide shows a ∼0.44 nm increase in graphene
thickness (∼0.36 nm) due to the presence of epoxy and hydroxyl
groups on both sides of the oxide surface.31,32 The larger
thickness observed in this work (∼1.6 nm) may be due to the
presence of the particle-like features between the platelets56 in
addition to the presence of the functional groups adsorbed on
both sides of a single-layer graphene oxide sheet.34 By annealing
the as-deposited graphene oxide/TiO2thin film at
400 °C, the surface concentration of the particle-like features
on the surface decreased, as can be seen in Figure 1b. Moreover,
the height profile measurement showed that the thickness of
the graphene oxide layers decreased to about 1.1 nm. This
indicated that the residual materials initiated evaporation not
only from the surfaces, but also from the space between the
platelets. After exposing the graphene oxide/TiO2thin films to
UV irradiation for 4 h (Figure 1c), the spacing between the
platelets was measured in the range of about 0.75-0.80 nm, as
shown in the height profile diagram of Figure 1c. The decrease
of the thickness of the platelets down to values smaller than
the theoretical value for the thickness of graphene oxide
nanosheets may refer to reduction (but, likely not a complete
reduction) of the graphene oxide platelets to graphene ones. This
matter will be discussed in more details by using XPS analysis.
To study the chemical state variations of the graphene (oxide)/
TiO2thin films, XPS analysis was utilized. Figure 2 shows XPS
J. Phys. Chem. C, Vol. 113, No. 47, 2009 20215