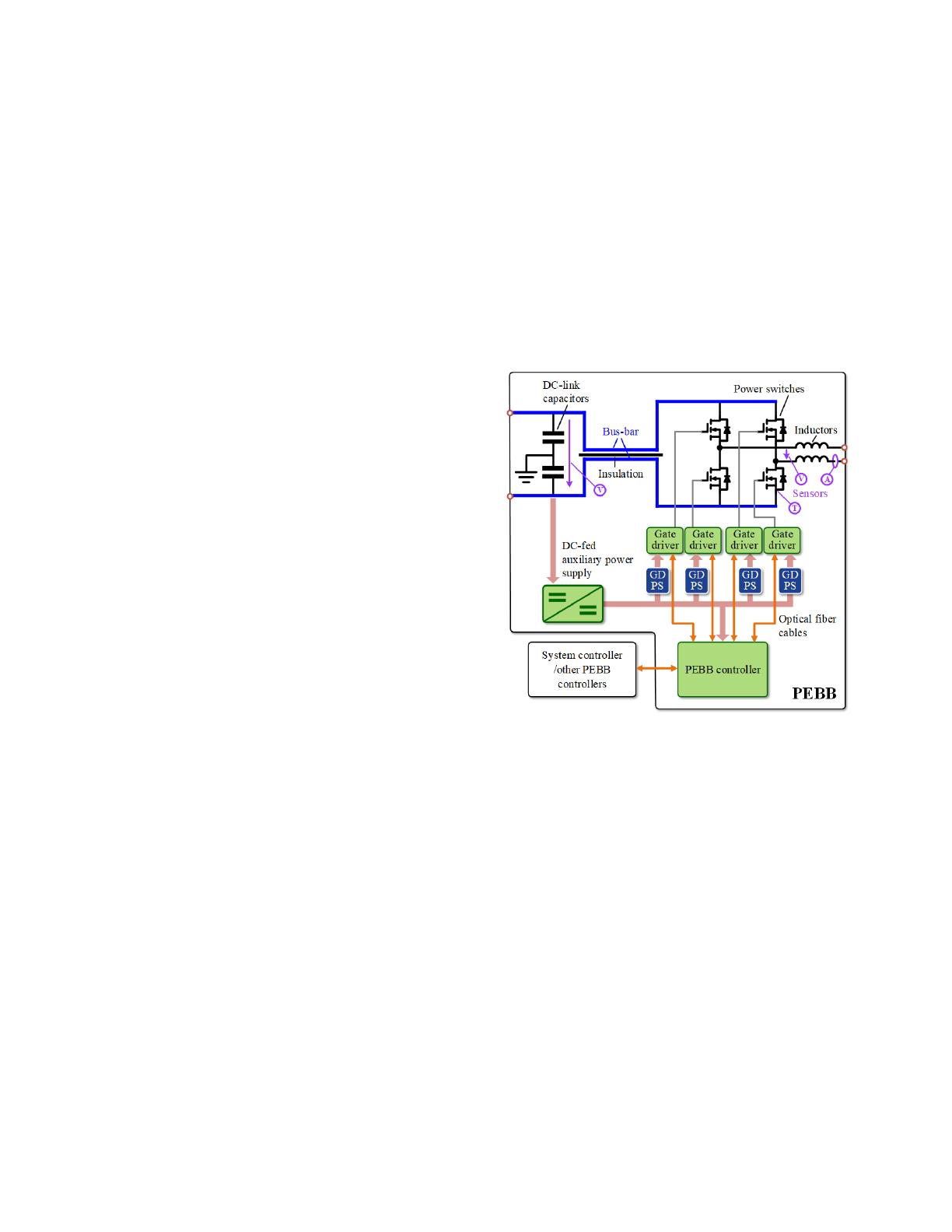
A High-Speed Gate Driver with PCB-Embedded
Rogowski Switch-Current Sensor for a 10 kV, 240
A, SiC MOSFET Module
Jun Wang, Slavko Mocevic, Yue Xu, Christina DiMarino, Rolando Burgos, Dushan Boroyevich
Center for Power Electronics Systems
Virginia Polytechnic Institute and State University
Blacksburg, VA, USA
Abstract—High-voltage SiC MOSFET modules are revolu-
tionizing modern high power electronics owing to their high
blocking voltage, low conduction resistance, and fast switching
frequency. A 10 kV, 240 A SiC MOSFET module has recently
become a candidate to build medium-voltage converters. The
MOSFET module comprises three independent submodules that
can be configured as three phase-legs, or one half-bridge by
paralleling. To maximize its performance, this paper presents
a smart gate driver design for this particular semiconductor
device. The design concentrates on a high-current booster stage
and a high-bandwidth PCB-embedded Rogowski switch-current
sensors for the paralleled submodules. The PCB layout has
satisfied high-voltage clearance and creepage standards. Finally,
the booster current sharing and RSCS performance have been
experimentally validated.
Index Terms—10 kV SiC MOSFET, smart gate driver, paral-
leled current boosters, Rogowski switch-current sensor
I. INTRODUCTION
Owing to the booming technology of wide-bandgap (WBG)
semiconductor devices and packaging, silicon-carbide (SiC)
MOSFETs have demonstrated their superior performance to Si
IGBTs in terms of higher breakdown voltage, faster switching
speed, lower switching loss and higher operating temperature
[1] [2]. The high blocking voltage of SiC MOSFETs simplifies
converter power stage by using uncomplicated topologies,
and meanwhile their high switching frequency preserves the
overall harmonic performance despite of reduced number of
voltage levels. Recently, Wolfspeed has developed a 10 kV,
240 A SiC MOSFET module XHV-6, which uses their 3rd-
generation 10 kV, 350 mΩSiC MOSFETs [1] with an im-
proved package layout [3]. This device is suitable to construct
converters such as a 6∼7 kV dc, 3.3 kV ac motor drive
by using a simple three-phase two-level topology. In this
research work, the device serves as a critical component in a
power electronics building block rated at 6 kV dc bus voltage
(PEBB6000) as shown in Fig. 1 [4]. The power-stage topology
is an H-bridge that consists of two XHV-6 modules. The three
submodules of each module are paralleled by internal jumpers
within the device package.
This material is based upon research supported by the U.S. Office of Naval
Research under award number N00014-16-1-2939.
Fig. 1. PEBB6000 system architecture diagram.
As seen in Fig. 1, four gate drivers are needed to drive
the four SiC MOSFET switches in two XHV-6 modules. Gate
driver is the critical interface between power semiconductor
devices and control signals. It serves to provide galvanic
isolation and to supply driving current while maintaining
signal integrity under high-noise environment. For the XHV-
6 module, three submodules that contain 18 10 kV, 350
mΩSiC MOSFET dies need to be driven simultaneously.
The driving current magnitude, driving signal synchronization,
driving loop parasitics, and common-mode noises become big
challenges. On top of those basic tasks, a gate driver can
also provide quick, reliable, and configurable protections, as
well as advanced switch-current signal sensing, digital data
processing, and active gate controllability, which define a
“smart” gate driver. Taking those factors into consideration,
Table. I summarizes the specifications and design objectives
of the gate driver for the XHV-6 module.
978-1-4799-7312-5/18/$31.00 ©2018 IEEE 5489
Authorized licensed use limited to: INP TOULOUSE. Downloaded on September 26,2021 at 21:20:31 UTC from IEEE Xplore. Restrictions apply.