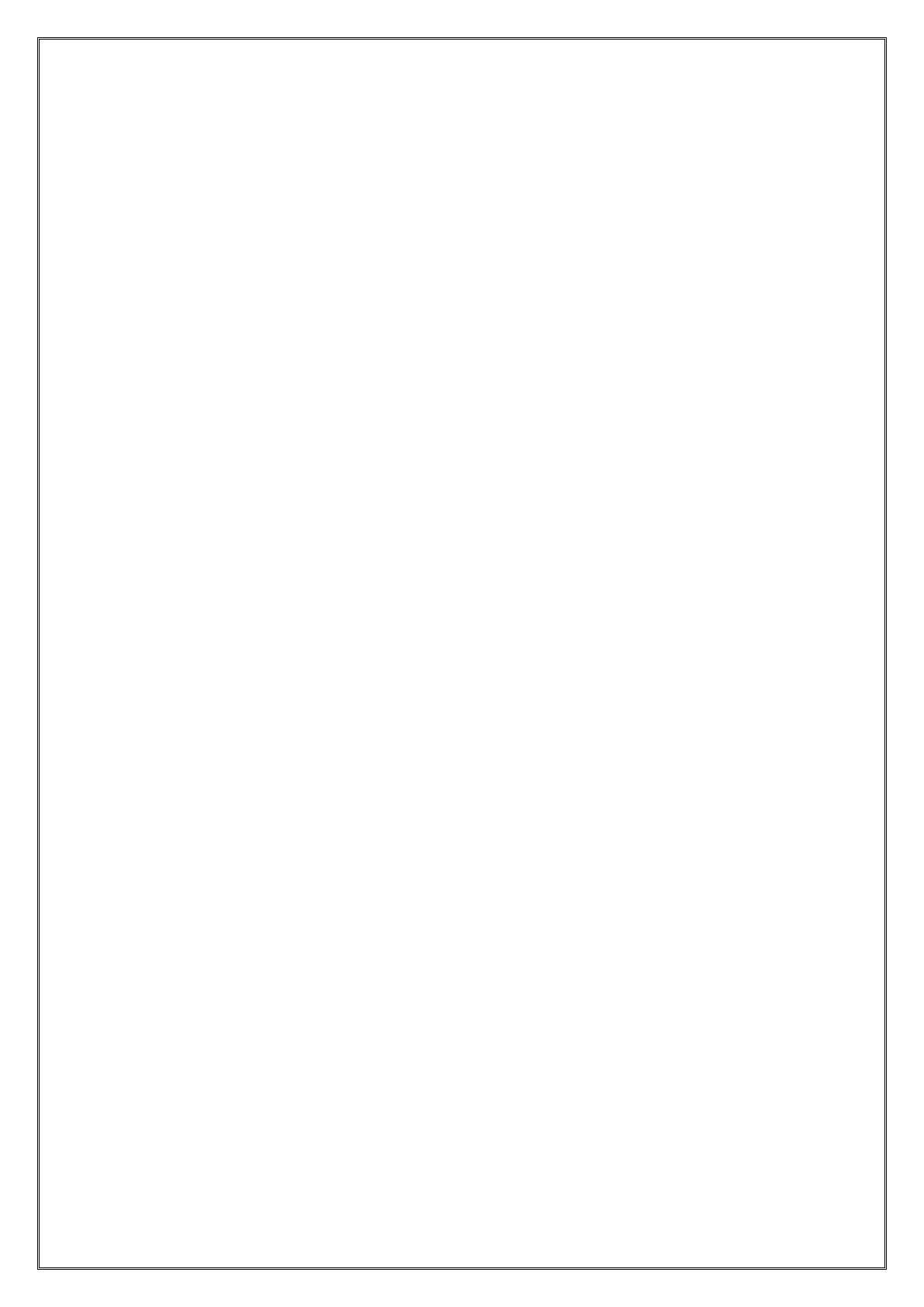
5
1. Les eaux domestiques : .......................................................................................... 36
2. Les eaux industrielles et artisanales : ..................................................................... 37
III. Caractérisation des eaux usées des huileries : ........................................................... 37
1. Caractérisation physico-chimique : ........................................................................ 37
2. Caractéristiques microbiologiques : ....................................................................... 38
IV. Les normes de rejets des eaux usées des huileries : .................................................. 38
V. Impacts environnementaux des rejets des huileries : ................................................. 39
VI. Nécessité de traitement : ............................................................................................ 41
Chapitre 2 : présentation du fonctionnement de la station de traitement des eaux usées type
boue activé ................................................................................................................................ 42
I. Principe de l’épuration des eaux usées part boue activé : ......................................... 42
II. Les composantes d’une station de traitement des eaux usée à boue activé : ............. 43
1. Filière eau : ............................................................................................................ 43
2. Filière boue : .......................................................................................................... 54
3. Filière Gaz : ............................................................................................................ 59
4. Avantage et inconvénient du traitement par boue activé : ..................................... 62
5. Les différents types de dysfonctionnement d’une STEP à boue activé ................ 63
6. Méthodes de lutte contre le dysfonctionnement de la station d’épuration :........... 67
7. Conclusion ............................................................................................................. 69
PARTIE III : Description et diagnostic de la station de traitement des eaux usées de LESIEUR
CRISTAL ................................................................................................................................. 70
Introduction .............................................................................................................................. 71
Chapitre 1 : Présentation de la station de traitement des eaux usée de Lesieur cristal ............ 72
I. Situation géographique : ............................................................................................ 72
II. Historique de la STEP ............................................................................................... 73
III. Objectif de la STEP ................................................................................................... 73
1. Objectif environnemental ....................................................................................... 73
2. Gestion des ressources en eau ................................................................................ 74
Chapitre 2 : Présentation des principaux rejets de Lesieur cristal ............................................ 75