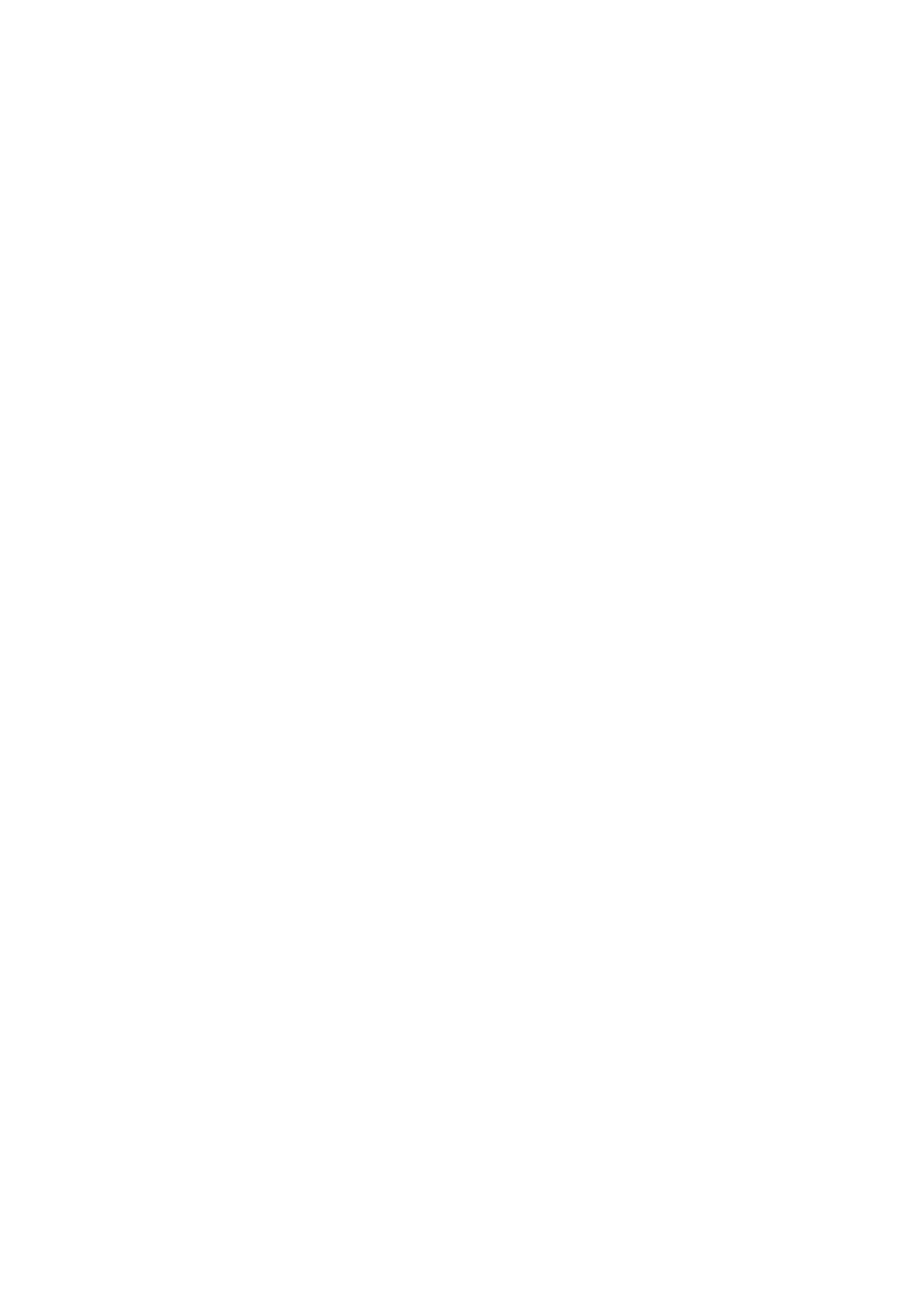
1. PRODUCTION DE CIMENT EN AFRIQUE DU SUD
1.1. PRÉAMBULE
La production de ciment est un processus à forte intensité énergétique, 20 à 40% des coûts totaux
étant alloués à l'énergie et 17% à l'électricité [1.1, 1.2]. En raison de l'augmentation rapide du coût
de l'électricité en Afrique du Sud (voir figure 1) et du coût international du charbon (voir figure 2) -
disproportionnée par rapport à l'inflation - le coût de production augmente. Outre l'augmentation
globale du coût de production du ciment, les ventes de ciment en Afrique du Sud ont chuté de
manière spectaculaire depuis 2006/2007 (comme le montre la figure 3). Ces deux facteurs ont
motivé une étude approfondie des projets réalisables qui peuvent être mis en œuvre pour diminuer
le coût énergétique lors de la production de ciment.
"Diverses nouvelles technologies sont disponibles qui permettent à l'industrie de la fabrication du
ciment de fonctionner plus efficacement [2]. Ces technologies sont disponibles pour divers
composants, notamment les broyeurs, les fours et le transport par convoyeur [2, 19]. La plupart de
ces technologies nécessitent l'installation de nouveaux équipements et offrent des économies
d'énergie électrique moyennes comprises entre 1 kWh et 5 kWh par tonne [20-22]. Dans une analyse
du cycle de vie, Valderrama [18] a indiqué que la mise en œuvre des meilleures technologies
disponibles (MTD) a permis de réduire la consommation d'électricité pour la production de clinker de
76 kWh à 69 kWh par tonne. Ces installations sont toutefois coûteuses et nécessitent des arrêts de
production prolongés [11, 12]. Le temps de retour sur investissement de ces installations est souvent
supérieur à 10 ans [21]..." [1.3].
Une autre technique pour réaliser des économies d'énergie consiste à améliorer les systèmes de
contrôle. Ces systèmes optimisent le fonctionnement de certains composants, assurant ainsi un
fonctionnement stable et optimal [1.7]. Des économies de 1,4 kWh à 6 kWh par tonne peuvent être
réalisées [1.4-1.7]. Valderrama [1.8] a rapporté une réduction de 4 % des émissions de CO2 en
mettant en œuvre les meilleures technologies disponibles (MTD). Des réductions des émissions de
NOx, SO2 et de poussières de 20,5%, 54% et 84% respectivement sont également possibles [1.3].
Les coûts de l'électricité peuvent être réduits en révisant les programmes d'exploitation [1.9]. La
tendance de la consommation nationale d'électricité en Afrique du Sud (voir la figure 4) illustre deux
pics clairs de la demande d'électricité. En réduisant ces pics d'une industrie individuelle, la demande
nationale maximale sera également réduite. Cela contribuera à limiter les émissions nationales. Pour
encourager la réduction de la demande de pointe, la compagnie d'électricité sud-africaine a utilisé
une structure tarifaire basée sur le temps d'utilisation (TOU).
L'optimisation de l'exploitation de l'électricité permettra de réduire les pics de demande et de
diminuer le coût de l'électricité. Cet objectif peut être atteint par la reprogrammation des opérations
et la mise en œuvre efficace du transfert de charge de la production. Le problème devient complexe
en raison des objectifs de production variables, des calendriers de maintenance, des pannes
d'équipement, de la production de l'usine et des contraintes de stockage. Une solution possible est
d'observer les contraintes opérationnelles pour être en mesure de reprogrammer les opérations afin
de réduire le coût énergétique de la production. Cette méthode peut permettre une mise en œuvre
rentable sans aucun arrêt de la production.