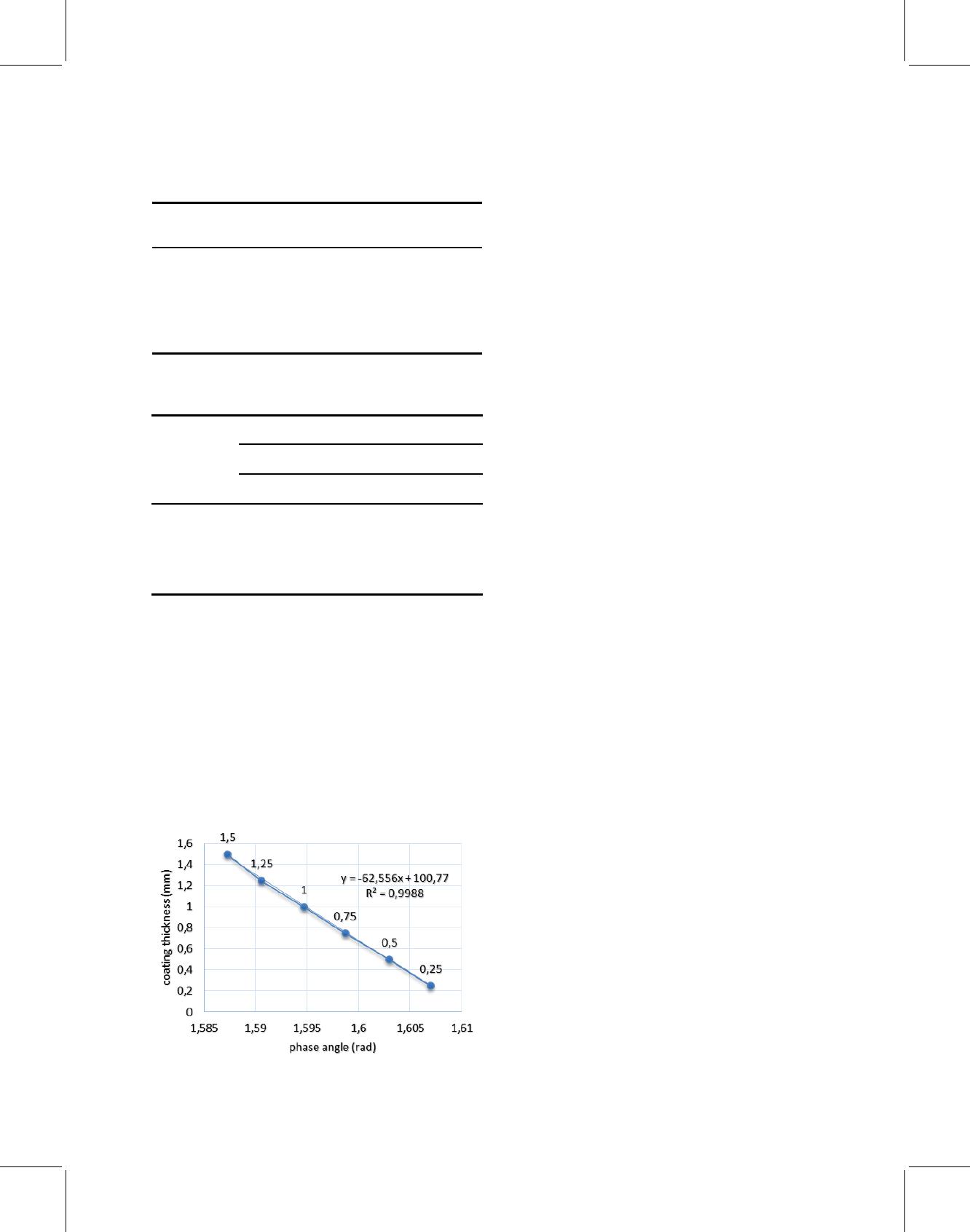
calculated for the di®erent excitation frequencies.
Table 5 shows the found values of the percentage
error. The value of the appropriate frequency is
fe ¼0:2 Hz with R2¼0:9988 and maximum per-
centage error with 2.99%. The correlation between
the coating thickness and the phase angle is per-
formed as shown in Fig. 7, the relationship can be
expressed as Eq. (6)
T¼62:556þ100:77:ð6Þ
The estimated values of the error for the di®erent
thicknesses and di®erent frequency is calculated and
arranged in Table 4.
4. Conclusion
In this study, the method of LIT is applied to a gal-
vanized sample composed of multiple layers with
various thicknesses ranging from 0.25 to 1.25 mm. The
excitation contains a sinusoidal heat °ux contributing
with a convective °ux whose thermal exchange coef-
¯cient is 10 w/m
2
.k, the emissivity of the de¯ned
surface has the value of 0.1. The FEM determines the
temperature evolution as a function of time. Several
values of the excitation frequency ranging from 0.01 to
0.2 Hz are used to evaluate the accuracy of the results.
The phase angle obtained by the Fourier transform
characterizes the value of the coating thickness. The
advantage of the method used is the linear correlation
found between the phase and the thickness, the fre-
quency which gives the good results is fe ¼0:2 Hz.
A simple relation between the coating thickness and
the phase angle is determined and the value of the
estimated thickness is very close to the actual value
with an accuracy of 0.011 to 0.029 mm. LIT proves its
e±ciency in the calculation of the coating thickness.
References
1. O. Breitenstein, W. Warta and M. Langenkamp, Lock-
in Thermography: Basics and Use for Evaluating
Electronic Devices and Materials, seconded., (Springer
Science & Business Media, New York, 2010).
2. A. C. Karaoglanli, K. M. Doleker and Y. Ozgurluk,
State of the Art Thermal Barrier Coating (TBC)
Materials and TBC Failure Mechanisms, Properties
and Characterization of Modern Materials, (Springer,
2017), pp. 441–452.
3. C. Li, Non-destruct. Test. 27 (2005) 454–456.
4. Ptaszek,P.Cawley,D.Almondet al.,NDTE Int.
45 (2012) 71–78.
5. G. U. O. Xing-wang and D. I. N. G. Meng-meng, Acta
Aeronaut. Astronaut. Sin. 31 (2010) 198–203.
6. Y. Zhang, X. Meng and Y. Ma, Infrared Phys. Tech-
nol. 76 (2016) 655–660.
7. J. P. Holman, Heat transfer, Chinese machine press,
2005 J. Mater. Chem. 21 (2011) 5011–5020.
8. J. Liu, J. Dai and W. Yang, Infrared Phys. Technol.
53 (2010) 348–357.
9. D. Peng and R. Jones, Eng. Fail. Anal. 28 (2013) 275–288.
10. C. Ibarra-Castanedo and X. Maldague, Quant. Infra-
red Thermography J. 1(2004) 47–70.
Table 4. Predicted coating thickness and the percentage
error.
Actual
thickness (mm)
Calculated
(rad)
Predictive
(mm) Error (%)
0.25 1.607 0.2425 2.99
0.5 1.603 0.4927 1.45
0.75 1.5987 0.7617 1.56
1 1.5947 1.0119 1.19
1.25 1.5906 1.2684 1.47
1.5 1.5873 1.4748 1.67
Table 5. Percentage error for di®erent coating thickness as a
function of modulation frequency.
Percentage error for di®erent coating thickness
Thickness T(mm)
Frequency (Hz) 0.25 0.5 0.75 1 1.25 1.5
0.01 14.52 12.02 5.18 1.93 2.74 1.25
0.02 16.12 9.92 4.56 1.48 2.41 0.47
0.05 17.12 10.74 4.98 1.12 2.2 0.37
0.1 4.36 2.96 1.86 2.37 2.12 2.9
0.2 2.99 1.45 1.56 1.19 1.47 1.67
Fig. 7. Correlation between coating thickness and phase angle.
A Simple Method for Determining a Thickness of Metal Based on LIT
June 15, 2019 3:56:47pm WSPC/149-SRL 1930003 ISSN: 0218-625X
nd
ea
ng
1930003-5