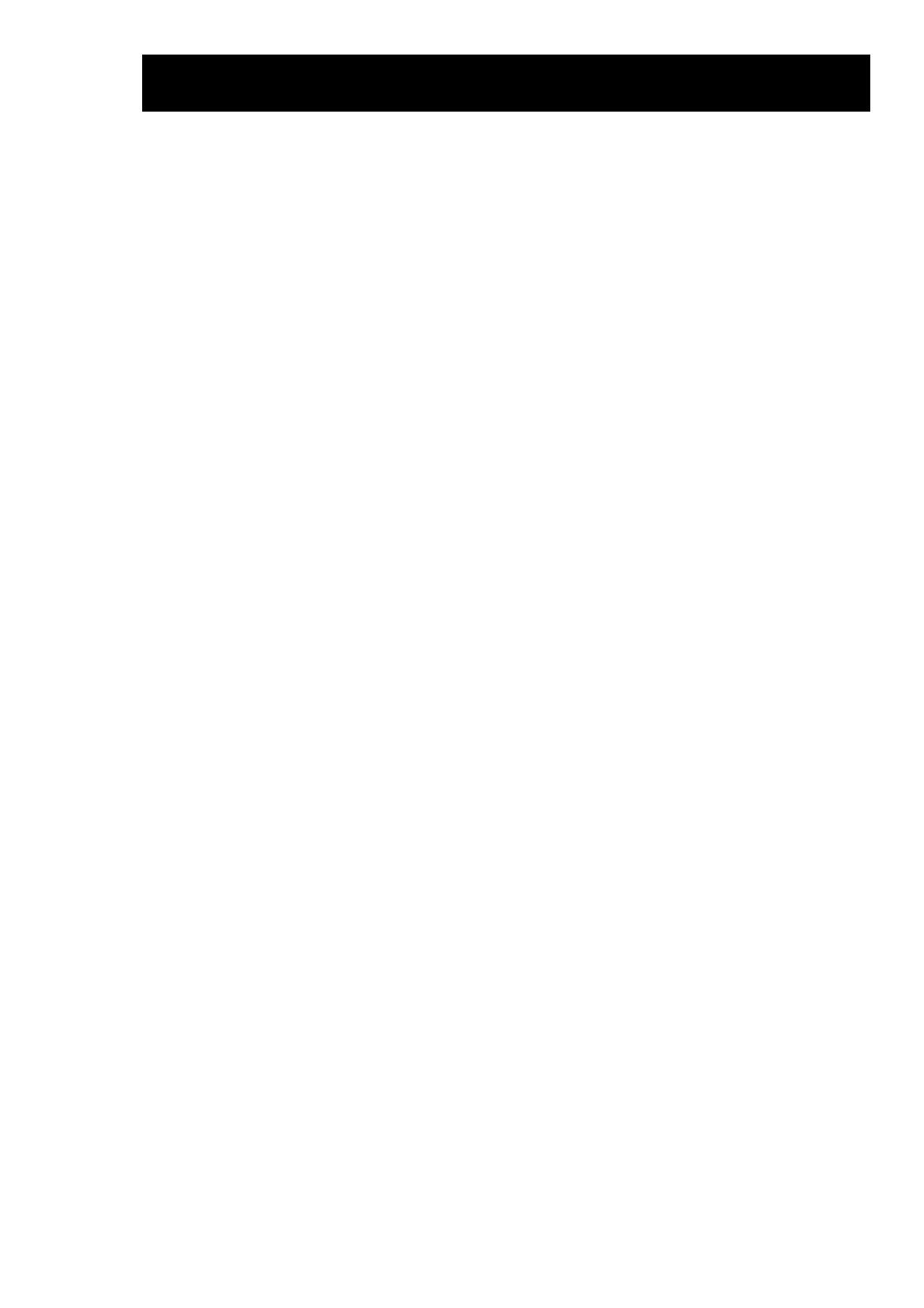
Service Manual iii
Contents
About This Manual ................................................................................................................................... xvii
Overview...................................................................................................................................... xvii
Conventions Used in This Manual.................................................................................................xxi
Instrument Markings and Symbols .............................................................................................. xxii
Using Hydrogen ...........................................................................................................................xxiv
Using the Hydrogen Sensor ............................................................................................xxiv
SECTION I
Introduction
Chapter 1.1
GC Base Unit..................................................................................................................................................3
TRACE GC 2000 System Components ............................................................................................4
Pneumatic Compartment......................................................................................................4
Analytical Unit.....................................................................................................................4
Electronic Compartment ......................................................................................................5
Keypad and Display Panel...................................................................................................5
Chapter 1.2
Pneumatic Systems.......................................................................................................................................7
Gas Control .......................................................................................................................................8
Digital Pneumatics...............................................................................................................8
Analog Pneumatics ..............................................................................................................8
Mixed Pneumatics................................................................................................................8
Carrier Gas Control..............................................................................................................8
Column Evaluation .................................................................................................9
Leak Check ............................................................................................................9
Gas Saver Function...............................................................................................13
Detector Gas Control .........................................................................................................13
Chapter 1.3
Injection Systems ........................................................................................................................................15
Injection Systems Overview ...........................................................................................................16
Split/Splitless Injector........................................................................................................16
On-Column Injector...........................................................................................................16
HOT Cold On-Column Injector .........................................................................................16
Large Volume On-Column Injector...................................................................................17
Packed Column Injector.....................................................................................................17
Purged Packed Column Injector ........................................................................................17
Chapter 1.4
Detection Systems ......................................................................................................................................19
Detectors .........................................................................................................................................20
Flame Ionization Detector..................................................................................................20
Electron Capture Detector..................................................................................................20
Nitrogen Phosphorus Detector ...........................................................................................20
Multidetector System .........................................................................................................21
Detector Base Bodies.........................................................................................................21