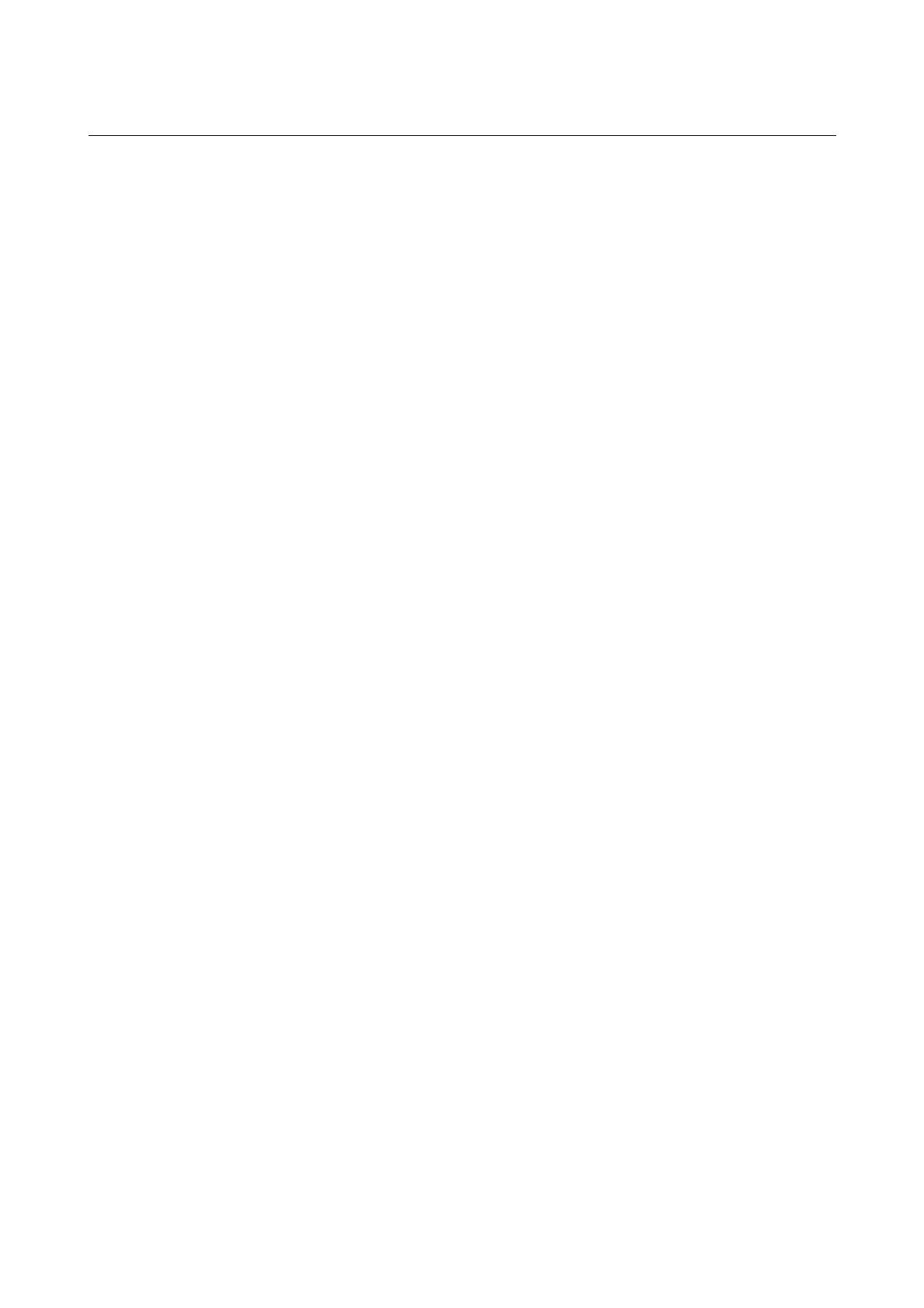
B-63494EN/01 TABLE OF CONTENTS
c-1
TABLE OF CONTENTS
SAFETY PRECAUTIONS
SAFETY PRECAUTIONSSAFETY PRECAUTIONS
SAFETY PRECAUTIONS................................
................................................................
................................................................
................................................................
................................................................
................................................................
.......................................................
..............................................
....................... s-
s-s-
s-1
11
1
1
11
1 OVERVI
OVERVIOVERVI
OVERVIEW
EWEW
EW................................
................................................................
................................................................
................................................................
................................................................
................................................................
................................................................
................................................................
.........................................
..................
......... 1
11
1
1.1
DIRECTIVE AND STANDARDS ..................................................................................................... 3
1.1.1 Directives.................................................................................................................................... 3
1.1.2 Related Safety Standards.......................................................................................................... 3
1.1.3 Risk Analysis and Evaluation................................................................................................... 3
1.1.4 Certification Test ....................................................................................................................... 4
1.2
DEFINITION OF TERMS ................................................................................................................ 5
1.2.1 General Definition of Terms ..................................................................................................... 5
1.2.2 Definition of Terms Related to the Safety Function................................................................ 5
1.3
BASIC PRINCIPLE OF DUAL CHECK SAFETY .......................................................................... 6
1.3.1 Features of Dual Check Safety ................................................................................................. 6
1.3.2 Compliance with the Safety Standard (EN954-1, Category 3) ............................................... 7
1.3.2.1
Latent error detection and cross-check ...........................................................................................8
1.3.2.2
Safety monitoring cycle and cross-check cycle ................................................................................9
1.3.2.3
MCC off Test .....................................................................................................................................9
1.3.2.4
Error analysis .................................................................................................................................10
1.3.2.5
Remaining risks..............................................................................................................................10
1.4
GENERAL INFORMATION........................................................................................................... 12
2
22
2 SYSTEM CONFIGURATIO
SYSTEM CONFIGURATIOSYSTEM CONFIGURATIO
SYSTEM CONFIGURATION
NN
N................................
................................................................
................................................................
................................................................
................................................................
................................................................
...........................................
......................
........... 14
1414
14
3
33
3 SAFETY FUNCTIONS
SAFETY FUNCTIONSSAFETY FUNCTIONS
SAFETY FUNCTIONS ................................
................................................................
................................................................
................................................................
................................................................
................................................................
.....................................................
..........................................
..................... 16
1616
16
3.1
APPLICATION RANGE ................................................................................................................. 17
3.2
BEFORE USING THE SAFETY FUNCTION............................................................................... 20
3.2.1 Important Items to Check Before Using the Safety Function .............................................. 20
3.2.2 MCC off Test of the Safe Stop Function ................................................................................. 20
3.3
STOP ................................................................................................................................................ 21
3.3.1 Stopping the Spindle Motor .................................................................................................... 21
3.3.2 Stopping the Servo Motor........................................................................................................ 22
3.3.3 Stop States ............................................................................................................................... 22
3.4
SAFE-RELATED I/O SIGNAL MONITORING ............................................................................ 24
3.5
EMERGENCY STOP ...................................................................................................................... 29
3.6
SAFE SPEED MONITORING........................................................................................................ 30
3.7
SAFE MACHINE POSITION MONITORING .............................................................................. 31