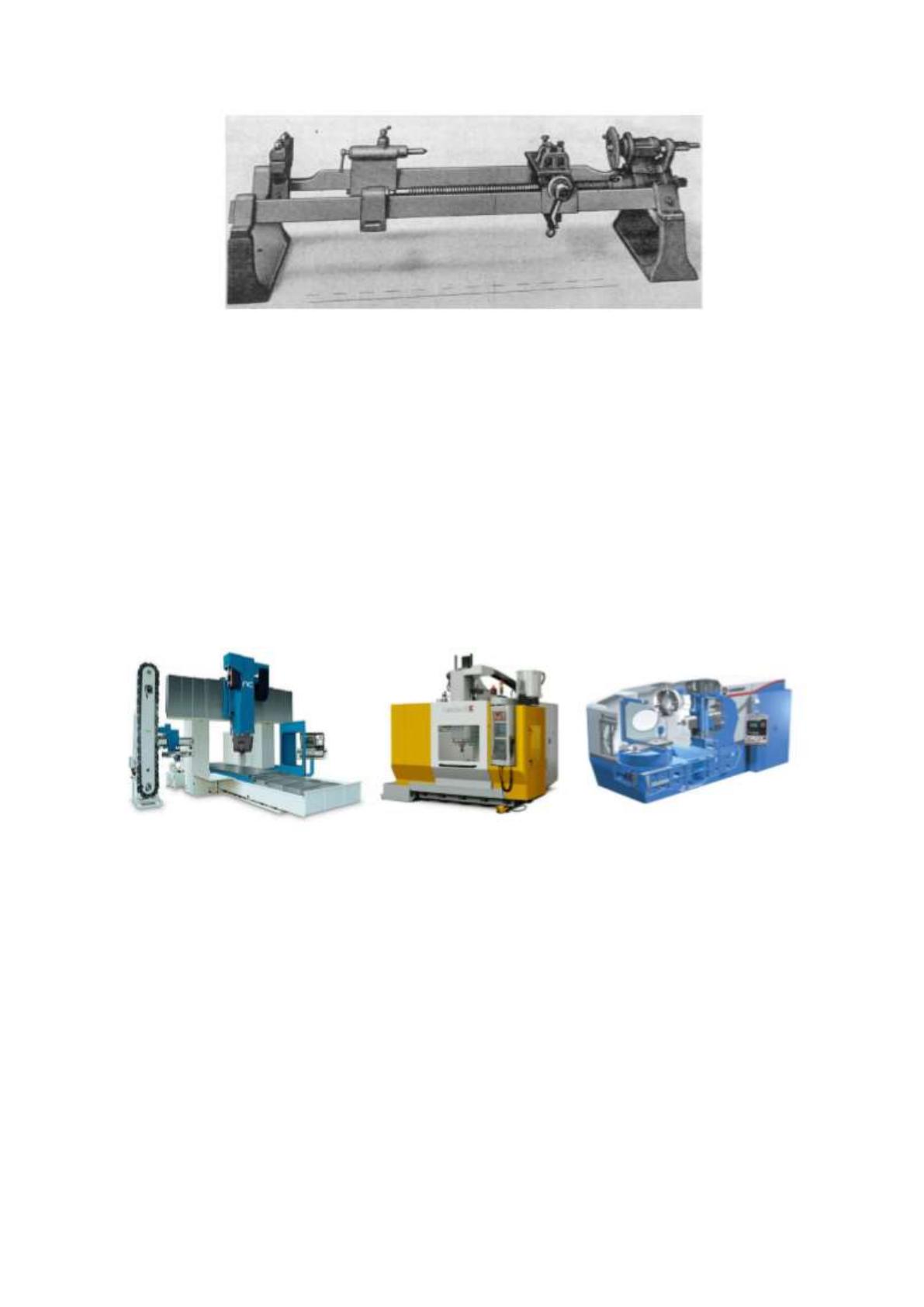
Figure 2 tour à fileter vers 1740
Au début du 20ème siècle, les machines-outils étaient déjà très similaires aux machines
actuelles, d’autant plus que le moteur électrique avait commencé à remplacer le moteur à
vapeur. L’industrie automobile offrit aux fabricants de machines-outils le plus vaste marché
qu’ils aient jamais eu. En effet, la fabrication d’automobiles requiert non seulement des pièces
de grande précision (moteur et transmission) mais surtout des volumes de production
considérables. La fabrication en série, prônée par Henry Ford, allait avoir une grande influence
sur la conception des machines-outils. Celles-ci devaient être de plus en plus spécialisées, voire
même mono-tâche, les pièces étant convoyées automatiquement d’une station à l’autre sur la
ligne de production. L’investissement en capital, très lourd pour ce type de machines, fut
compensé par une cadence de production beaucoup plus grande et, consécutivement, un coût
unitaire moindre.
Figure 3 centres d'usinage modernes
Jusqu’au début du 20ème siècle, les fabricants de machines-outils se trouvaient en Europe
(Angleterre, Allemagne, France et Belgique) et aux Etats-unis. Par la suite, de nombreux pays
s’industrialisèrent rapidement (Japon, Union Soviétique, …). Les deux guerres mondiales
contribuèrent aussi fortement au développement de nouvelles conceptions de machines, de
nouveaux outils et de nouvelles techniques. Ainsi, dans les années vingt, l’entreprise allemande
Krupp mit au point les plaquettes en carbure de tungstène, ce qui représenta un nouveau bond
dans les performances des outils de coupe. A la fin de la seconde guerre mondiale, l’industrie
aéronautique devint un des marchés les plus importants de la machine-outil. Il faut noter que
les besoins des entreprises aéronautiques sont très différents de ceux de l’industrie automobile.
En effet, il s’agit plutôt de petites séries de pièces très complexes pour lesquelles il faut des
machines polyvalentes capables de réaliser toute une gamme d’opérations diverses (fraisage,
rainurage, perçage, taraudage, …). Avec le développement des ordinateurs apparut une des