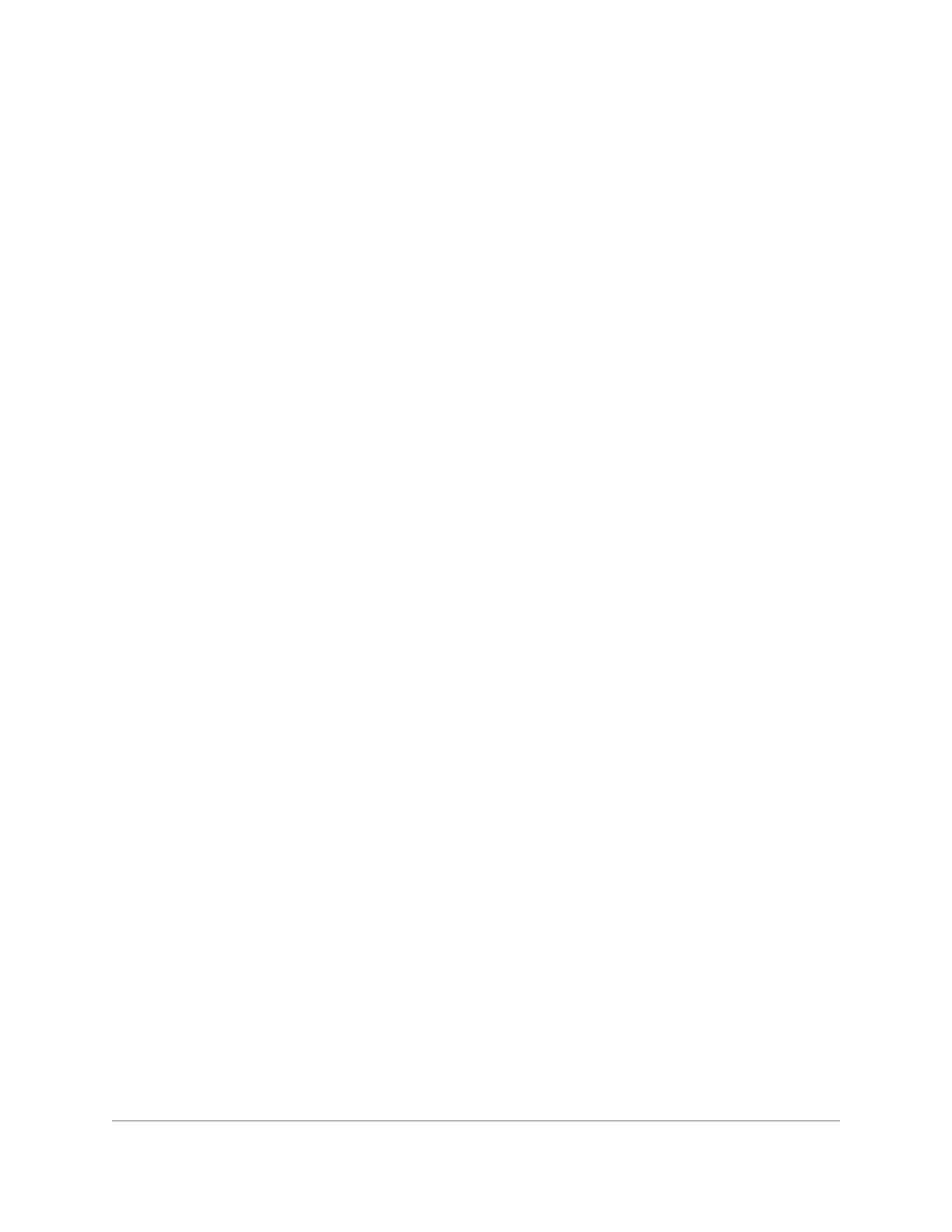
=0;=0>09??3,?8D?30>4>:=/4>>0=?,?4:9,9/,->?=,.?,=08D:=4249,7B:=6$=:;0=,L=4-@?4:93,>-009
24A09?:,77:@?>4/0>:@=.0>@9/0=>?,9/?3,?,8>:707D=0>;:9>4-701:=:-?,49492,9D900/0/.:;D=423?
;0=84>>4:9>3,A0:-?,490/900/0/B=4L09;0=84>>4:9>?,?0809?>1=:8?30:B90=>:10,.3?34=/
;,=?D.:;D=423?0/8,L0=?:-049.7@/0/498DB:=6,77:B492070.?=:94./4>?=4-@?4:941>@.3@>04>9:?
;0=84L0/-D?301,4=@>0/:.?=490B34.3B477-0>@-84L0/?:(9:B70/20,>//4?4:9,7470
30=0
-D2=,9
??:I0(
94A0=>4?D:1
[email protected],9/4?>,
209?>?304==
0A:.,-
709:90C.7@>4A0
,9/=:D,7?D
1=0074.09>0?:,=.34A0,9/8,60,..0>>4-708DB:=649B3:70:=49;,=?49,771:=8>:180/4,9:B:=
30=0,K0=69:B9,2=00?3,??30/:.@809?809?4:90/,-:A08,D-08,/0,A,47,-704880/4,?07D1:=
B:=7/B4/0,..0>>@970>>,908-,=2:,;;740>
=0?,49,77:?30=:B90=>34;=423?>?:?30.:;D=423?:18DB:=6,7>:=0?,49?30=423??:@>0491@?@=0
B:=6>>@.3,>,=?4.70>:=-::6>,77:=;,=?:18DB:=6@9/0=>?,9/?3,?,81=00?:=024>?0=?30
.:;D=423??:8DB:=6
I0/:.@809?809?4:90/,-:A03,>-009=0A40B0/,9/,..0;?0/-D?30>?@/09?F>,/A4>:=:9-03,71:1
?30,/A4>:=D.:884L00,9/-D?304=0.?:=:1=,/@,?0&?@/40>&:9-03,71:1?30;=:2=,8B0
A0=41D?3,??34>4>?30J9,7,;;=:A0/A0=>4:9:1?30>?@/09?F>?30>4>49.7@/492,77.3,920>=0<@4=0/-D?30
,/A4>:=D.:884L00I0@9/0=>4290/,2=00?:,-4/0-D?30>?,?0809?>,-:A0
#7@B,>0@9!60D:&?@/09?
=,9!:907!,5:=$=:10>>:=
=,4.3092 @4=0.?:=:1=,/@,?0&?@/40>