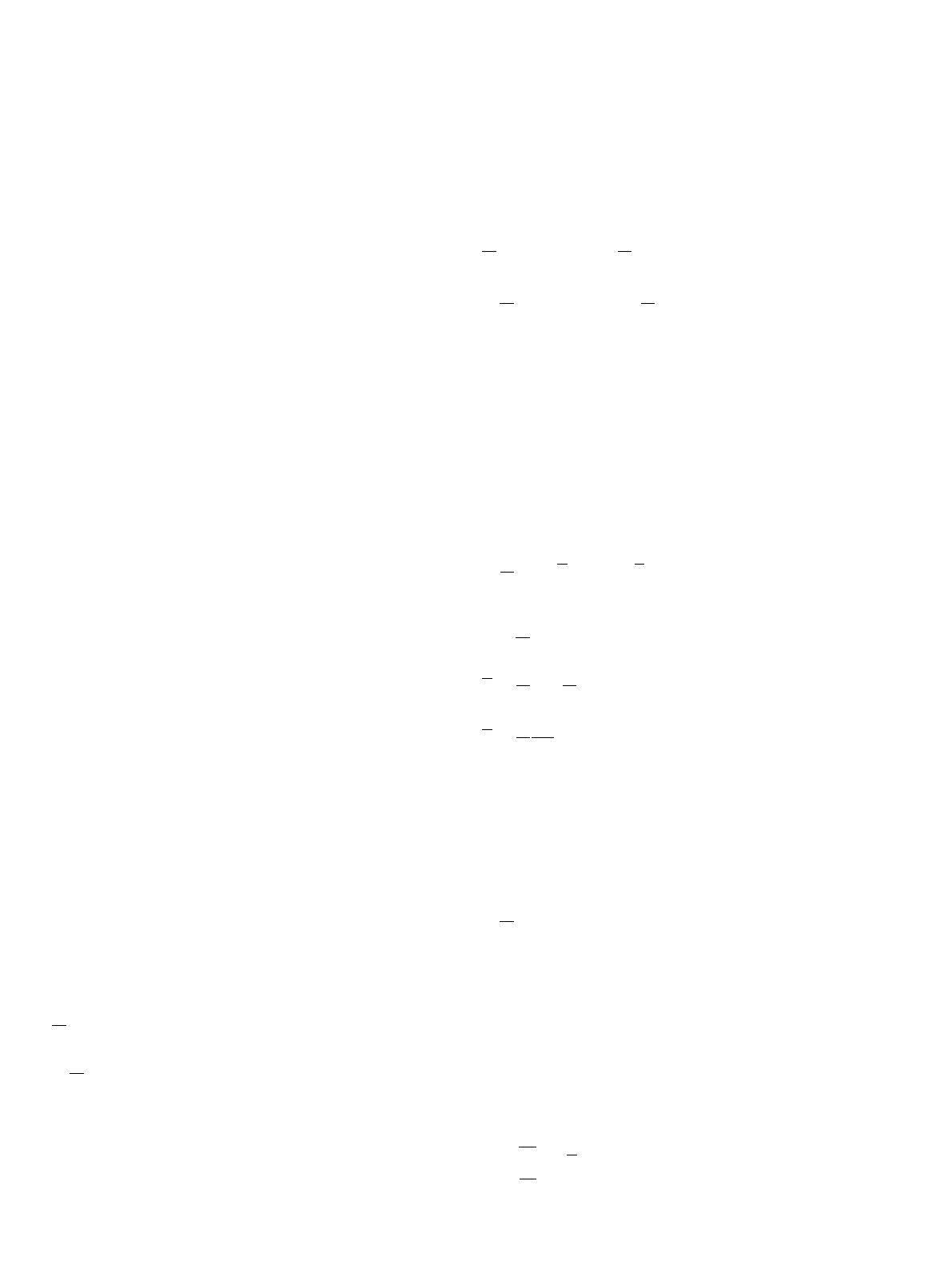
These equations have been widely used as the basis for many
studies in this area with various simplifications according to the
specific physics and geometry of the problem investigated. Some
studies have been done to find the analytical solutions for the
coupled moisture/temperature problem in porous media with
regular geometries [15–17]. In all these studies, the material
transport properties were considered constant in order to obtain
closed-form analytical solutions, even for structures with simple
geometries. Other researchers have alternatively used various
numerical techniques to solve the coupled hygrothermal problem
[18–20]. Several published works are also available regarding the
analysis of the mechanical behavior of the porous structures
caused by the moisture variations through the medium [21–24].
These studies, however, have limitations such as specific simple
geometry, constant material properties, monolithic material, non-
permeability of part of the structure, or one-dimensional moisture
migration analysis.
In spite of these valuable studies, to date, there is little
research that addresses the three-dimensional hygro-thermo-
mechanical problem of a multi-layered structure constructed of
distinctive permeable materials with general moisture/tempera-
ture dependent material properties. Due to the complexity of the
governing equation for the hygro-thermo-mechanical problem as
well as the geometry of these structures, obtaining a closed-form
analytical solution is very difficult, if possible. Simplification of
the equations and the geometry would result in unrealistic
solutions with little or no practical value. On the other hand,
experimental study of the long-term environmental effects on
such structures would be very time consuming and expensive.
Using finite element technique to carry out comprehensive
studies for the long-term durability problem of FRP composites
reinforced masonry structures is a practical alternative.
In this paper, a finite element model, previously presented by
the authors to analyze the hygrothermal behavior of an FPR/
concrete wall structure [25] is augmented to develop a compre-
hensive model for hygro-thermo-mechanical analysis of this type
of structures. The structural analysis formulation is incorporated
into the hygrothermal model to determine the effects of moisture
swelling and thermal expansion on the mechanical response of
the wall structure. The developed hygro-thermo-mechanical
model is then implemented to analyze the behavior of a typical
concrete slab with FRP laminate reinforcement under various
temperature and humidity gradient loads. The phenomenon of
heat-induced moisture movement is particularly investigated to
evaluate its resulting interfacial stresses at the FRP/concrete
bonding surface.
2. Finite element implementation of the hygrothermal
problem
The coupled moisture migration and heat transport problem in
porous media was formulated by Philip and De Vries [13] in the
form of the following system of differential equations:
@
y
@t¼
r
ðDy
ry
Þþ
r
ðD
T
r
TÞ,ð1Þ
r
c@T
@t¼
r
ð
lr
TÞþh
v
r
ðDy
vap
ry
Þ,ð2Þ
where
y
is the moisture content (kg/m
3
), Tis the temperature (K),
D
y
is the moisture diffusion coefficient (m
2
/s), D
T
is the thermal
moisture diffusion coefficient (kg/(m s K)),
r
cis the volumetric
heat capacity (J/(m
3
K)),
l
is the thermal conductivity (W/(m K)),
h
v
is the latent heat of vaporization (J/kg), Dy
vap
is the isothermal
vapor diffusivity (m
2
/s).
The transport coefficients are to be determined experimen-
tally. Among these coefficients, there is a lack of vigorous
definition for the coefficient of thermal moisture diffusion, D
T
.
Therefore, American Society for Testing and Materials (ASTM) in
2001 suggested a modified version for this system of equations as
the standard tool for moisture analysis in building envelopes [26].
In the proposed mathematical model, the governing equations
take the modified form as
@
y
@t¼
r
ðDy
ry
Þþ
r
d
P
mr
ðhP
s
Þ
,ð3Þ
r
c@T
@t¼
r
ð
lr
TÞþh
v
r
d
P
mr
ðhP
s
Þ
,ð4Þ
where his the relative humidity of the surrounding air
(dimensionless),
m
is the vapor resistivity of the porous medium
(dimensionless),
d
P
is the vapor permeability of the air (kg/
(m s Pa)), P
s
¼P
0
exp½ð
D
H=RÞðð1=TÞð1=373:15ÞÞ is the saturation
vapor pressure (Pa), in which P
0
¼101,325 (Pa) is the pressure of a
standard atmosphere, and
D
H/R¼5201 (K) measured for liquid
water.
For a multi-layered structure, since the moisture content is
discontinuous at the interface of different layers of constituent
materials, a change of variable approach was taken by Lin et al.
[27] to substitute moisture content,
y
, with relative humidity, h,
which resulted in the following form for the moisture diffusion
equation:
C
h
@h
@t¼
r
ðD
h
r
hÞþ
r
ðD
T
r
TÞ,ð5Þ
where
C
h
¼@
y
@h,ð6Þ
D
h
¼@
y
@hD
h
þ
d
P
m
P
s
,ð7Þ
D
T
¼
d
p
m
D
H
RT
2
hP
s
,ð8Þ
in which D
h
is the moisture diffusion coefficient of the material
expressed in terms of relative humidity using sorption isotherm
relation.
The second term in the heat transfer equation, Eq. (4), which is
associated with latent heat was shown to be insignificant for the
temperature range considered and, therefore, was omitted. As the
result, the change of variable did not affect this equation. Thus,
the heat equation yields a simple form as
r
c@T
@t¼
r
:ð
lr
TÞ,ð9Þ
The values or functional forms of the various coefficients in the
governing equations as well as sorption isotherm relation for
typical concrete and FRP materials have been experimentally
characterized and collectively summarized [28]. Applying the
Galerkin finite element formulation to the coupled humidity and
heat transport equations yields the following finite element
equation in terms of nodal humidty/temperature vector
h
i
T
i
()
ði¼1,2,...,rÞ, with rbeing the total number of nodes
per element,
½C
e
@h
i
@t
@T
i
@t
8
>
>
<
>
>
:
9
>
>
=
>
>
;
þ½D
e
h
i
T
i
()
¼fQ
e
g,ð10Þ
M. Khoshbakht, M.W. Lin / Finite Elements in Analysis and Design 46 (2010) 783–791784