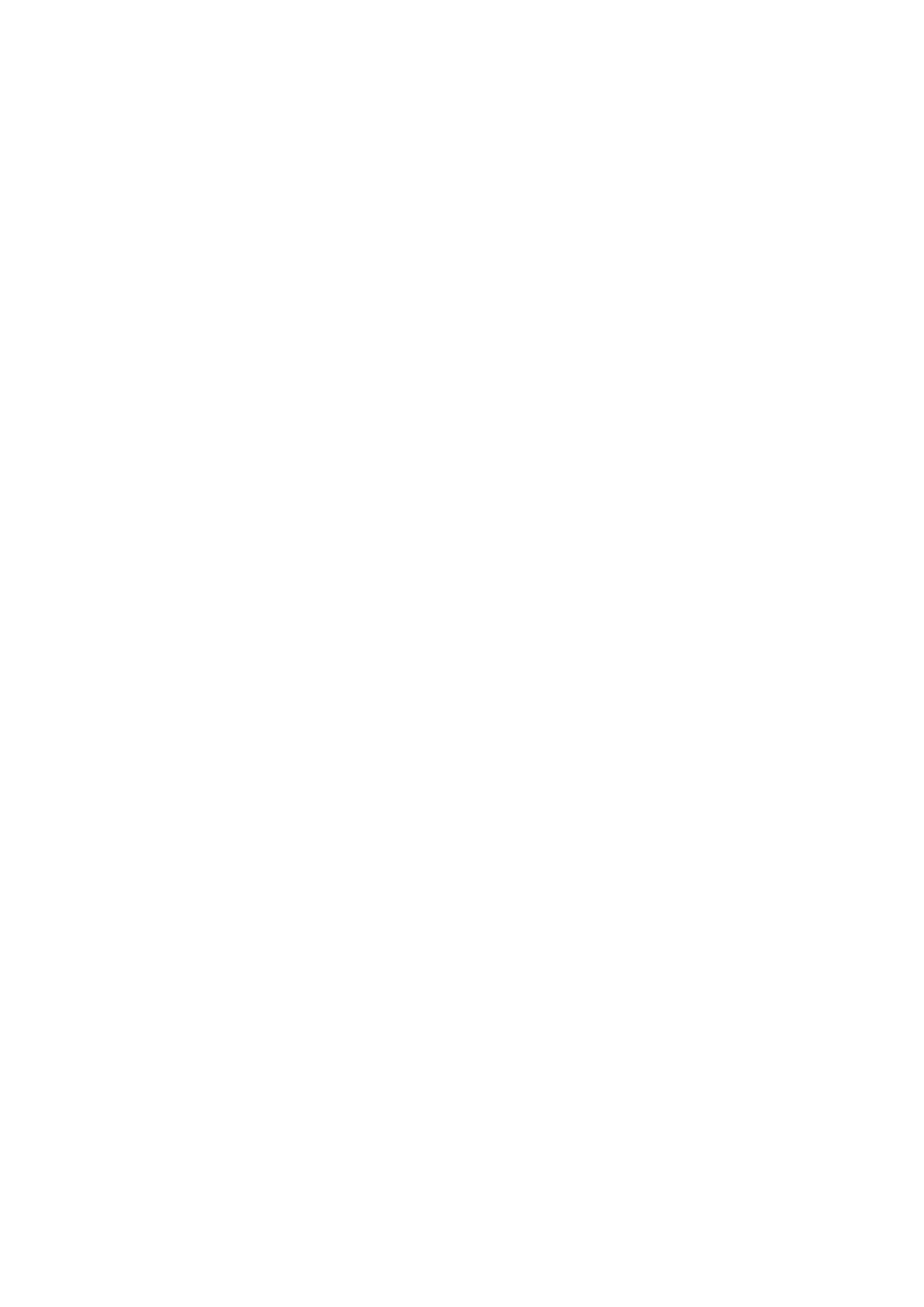
Page | 4
Table des matières
Introduction générale ........................................................................................................................ 8
Chapitre 1 : Recherche bibliographique .................................................................................................. 9
1. Introduction ............................................................................................................................ 9
2. Classification des systèmes d’agitation .................................................................................... 9
2.1. Classification suivant l’état physique des ingrédients à malaxer ....................................... 9
2.1.1. Pour Mélanger liquide à basse ou moyenne viscosité .................................................. 9
2.1.2. Pour Mélanger les poudres sèches et particules solides ............................................. 11
2.2. Calcification des mobiles selon le mouvement du fluide .................................................. 13
2.2.1. Mobiles à écoulement axial ....................................................................................... 14
2.2.2. Les mobiles à écoulement radial ................................................................................ 14
2.2.3. Mobiles à écoulement tangentiel ............................................................................... 15
3. Conclusion ............................................................................................................................. 16
Chapitre 2 : choix de la solution ......................................................................................................... 17
1. Introduction .......................................................................................................................... 17
2. Analyse fonctionnelle ............................................................................................................. 17
2.1. Recherche du besoin fondamental ................................................................................... 17
2.2. Modélisation du système ................................................................................................. 18
2.3. Diagramme de pieuvre .................................................................................................... 18
3. Présentation des solutions ...................................................................................................... 19
3.1. Transmission par poulie-courroie ................................................................................... 19
3.2. Turbine et mobile de proximité ayant deux sens de rotation inversés .............................. 21
3.3. Transmission par poulie-courroie + de rotation de sens inversés ..................................... 22
4. Choix de solution ................................................................................................................... 23
5. Principe de fonctionnement ................................................................................................... 23
6. Conclusion ............................................................................................................................. 23
Chapitre 3 : calcul et dimensionnement du système de malaxage ................................................................. 24
1. Introduction .......................................................................................................................... 24
2. Forces mises en jeux .............................................................................................................. 24
3. Dimensionnement de l'arbre plein ......................................................................................... 26
3.1. Contrainte de torsion ...................................................................................................... 26
3.2. Contrainte de flexion ....................................................................................................... 27
4. Choix des roulements ............................................................................................................ 27
5. Modélisation par éléments finis ............................................................................................. 28