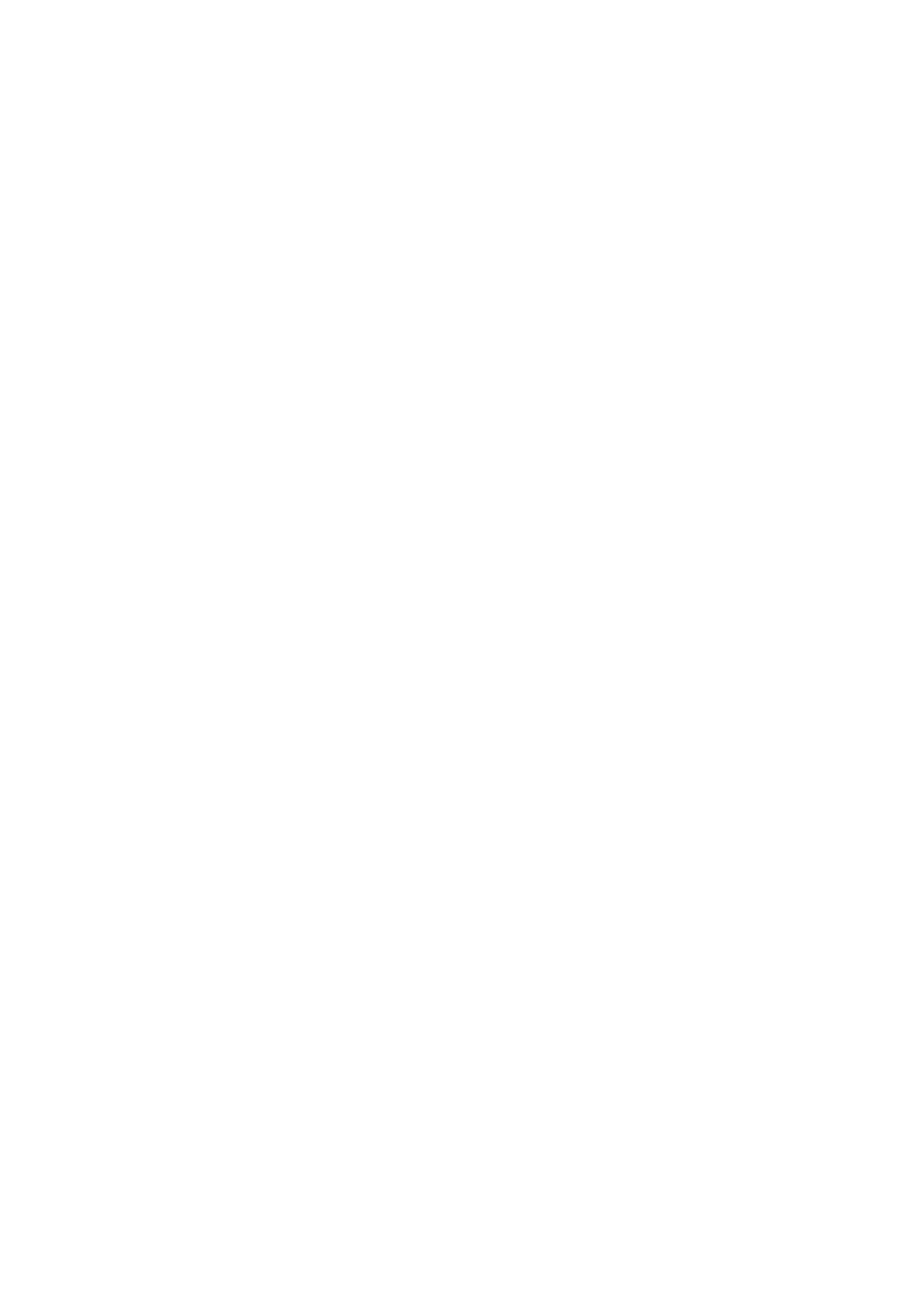
Remerciements
Ce mémoire marque la fin de trois années de recherche au sein de l’équipe maitrise de
l’énergie électrique (MEE) de l’Institut de Recherche en Energie Electrique de Nantes
Atlantique (IREENA), dans le cadre du projet de recherche Hydrol 44 financé par la Région
des Pays de la Loire.
Je tiens en ces quelques lignes à exprimer ma reconnaissance envers tous ceux qui
de près ou de loin y ont contribué.
Tout d’abord, je remercie chaleureusement messieurs Luc LORON professeur à
l’Université de Nantes et Mohamed BENBOUZID professeur à l’Université de Bretagne
Occidentale qui, en plus de diriger cette thèse, m’ont encadré et guidé tout le long de ces
années. Leur patience, conseils et remarques pertinentes ont largement contribué à
l’aboutissement de ce manuscrit.
Travailler avec monsieur Emmanuel SCHAEFFER, qui a encadré ces travaux, aura été
pour moi une expérience très enrichissante. Tant sur le plan professionnel que sur le plan
personnel. Sa grande compétence scientifique, sa disponibilité, son investissement dans cette
thèse, sa rigueur et son organisation ont été très précieux pour l’avancement de ce travail et
pour ma formation personnelle. Qu’il trouve ici l’expression de ma profonde gratitude.
Je remercie très chaleureusement l’ensemble des membres de jury qui ont accepté
d’évaluer mon travail ; messieurs Jean-François BRUDNY et Gérard CHAMPENOIS, pour
l’examen précis de ce mémoire qu’ils ont réalisé lors de la rédaction de leur rapport et les
questions et remarques lors de la soutenance qui ont permis d’éclaircir certains points
difficiles et surtout d’ouvrir le champ des investigations futures. M. Guy CLERC, pour
m’avoir fait l’honneur d’accepter de présider le jury de ma soutenance et pour les échanges
judicieux sur mes travaux.
Je remercie également messieurs Daniel LALOY, Mehdi BELHAJ et Julien CORMIER
de la société Jeumont Electrique Maintenance de m’avoir ouvert les portes de leur entreprise
et d’avoir collaboré activement à ce travail de recherche au travers des nombreux essais
expérimentaux que j’ai pu effectuer dans leurs ateliers sur des machines de fortes puissances,
ainsi que pour avoir fait le déplacement pour assister à ma soutenance.
Mes remerciements vont aussi à tous les membres de l’IREENA : le directeur du
laboratoire Mohamed MACHMOUM, tous les professeurs et les maitres de conférences du
laboratoire, sans oublier Mme Christine BROHAN pour son soutien administratif, M. Franck
JUDIC pour son soutien technique lors de nombreuses réalisations expérimentales durant les
trois années de thèse mais surtout pour sa gentillesse et sa bonne humeur.
Je souhaite remercier M. Mouloud FELIACHI et sa famille de nous avoir toujours réunis
autour d’un verre de thé, un repas ou une soirée conviviale avec des discussions très
enrichissantes dans tous les domaines. Je remercie également mes chers amis ; Ahmed,
Necereddine et sa femme Ryma pour les moments de famille qu’on a passé ensemble durant
ces trois dernières années. Des souvenirs qui resteront à jamais gravés dans ma mémoire.
Je remercie également mes amis de l’IREENA pour la bonne ambiance et les échanges
quotidiens (scientifique et autres), Ouahid, Zhihao, Kien, Quan, Nassim, Jian, Sadok, Fiacre,
Brahim, Alexis, Azeddine et Azza.
Je tiens à faire un clin d’œil à tous mes amis qui n’ont pas de lien avec l’IREENA, mais
qui m’ont toujours soutenus pendant la période de mes études ; Mehdi (El Jack), Samir,
Slimane, Yassine-R, Khaled, Djamel, Idir, Belkacem, Imad et Yassine-M.